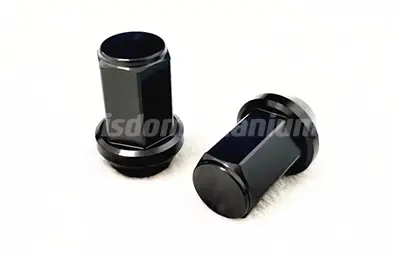
When it comes to automotive aesthetics and performance, every detail matters. Black titanium lug nuts have become increasingly popular among car enthusiasts and professionals alike, offering a perfect blend of style and functionality. However, the surface treatment of these lug nuts plays a crucial role in determining their longevity, performance, and overall appeal. Among the various surface treatment options available, Physical Vapor Deposition (PVD) black coating stands out as a superior choice. This article delves into the reasons why PVD black coating is the preferred surface treatment for black titanium lug nuts, exploring its numerous benefits and advantages.
Improve Durability
One of the primary reasons to choose PVD black coating for black titanium lug nuts is its exceptional durability. PVD coating creates an incredibly hard and wear-resistant surface, significantly enhancing the longevity of the lug nuts. This hardness is achieved through the deposition of thin films of material onto the titanium substrate at the atomic level, resulting in a dense, uniform coating with excellent adhesion.
The hardness of PVD coatings can range from 1000 to 3500 HV (Vickers Hardness), depending on the specific coating composition. This is substantially harder than many other surface treatments, including electroplating or anodizing. The increased hardness translates to superior resistance against scratches, chips, and general wear and tear, ensuring that the black titanium lug nuts maintain their appearance and structural integrity over time.
Moreover, the wear resistance of PVD coatings helps protect the lug nuts from the constant torque and vibration they experience during vehicle operation. This resistance to abrasion and wear ensures that the lug nuts maintain their tight fit and continue to perform their critical function of securing the wheels to the vehicle, even under demanding conditions.
Enhanced Corrosion Resistance
Corrosion is a significant concern for any automotive component, particularly those exposed to the elements. PVD black coating excels in providing superior corrosion resistance to black titanium lug nuts, making them ideal for use in various environmental conditions. The dense, pinhole-free nature of PVD coatings creates an effective barrier against corrosive agents such as moisture, road salt, and other chemicals commonly encountered on the road.
While titanium itself is known for its corrosion resistance, the addition of a PVD coating further enhances this property. The coating acts as a sacrificial layer, protecting the underlying titanium from direct exposure to corrosive elements. This is particularly beneficial in coastal areas or regions where road salt is frequently used, as these environments can be especially harsh on automotive components.
Furthermore, certain PVD coatings, such as titanium nitride (TiN) or chromium nitride (CrN), offer excellent chemical stability, providing resistance against a wide range of corrosive substances. This enhanced corrosion resistance not only preserves the appearance of the black titanium lug nuts but also maintains their structural integrity, ensuring long-term reliability and safety.
Optimize Fuel Efficiency
In the automotive industry, weight reduction is a constant pursuit to improve fuel efficiency and overall vehicle performance. PVD black coating contributes to this goal by allowing the use of lightweight materials like titanium for lug nuts without compromising on durability or aesthetics. The thin nature of PVD coatings, typically ranging from 1 to 5 microns, adds negligible weight to the component while providing substantial performance benefits.
By enabling the use of titanium lug nuts, which are approximately 45% lighter than traditional steel lug nuts, PVD coating indirectly contributes to weight savings. This weight reduction, although seemingly small, can have a cumulative effect when considered across all four wheels and in conjunction with other lightweight components. The resulting decrease in unsprung weight can lead to improved handling, acceleration, and braking performance.
Moreover, the reduced weight contributes to lower fuel consumption and, consequently, decreased carbon emissions. While the impact of lug nuts alone may be minimal, it aligns with the broader automotive industry trend towards lightweight, fuel-efficient vehicles, demonstrating a commitment to environmental responsibility and performance optimization.
Reduce Friction Coefficient
Friction reduction is another significant advantage of choosing PVD black coating for black titanium lug nuts. Certain PVD coating technologies, particularly Diamond-Like Carbon (DLC) coatings, are renowned for their low coefficient of friction. This property is crucial for lug nuts, as it facilitates easier installation and removal while also reducing the likelihood of galling or seizing.
DLC coatings can achieve a coefficient of friction as low as 0.1, significantly lower than uncoated titanium or other common coating materials. This low friction characteristic ensures that the correct torque is applied to the lug nuts during installation, reducing the risk of over-tightening or under-tightening, both of which can compromise wheel security.
Furthermore, the reduced friction leads to less wear on both the lug nuts and the wheel studs during repeated removal and installation cycles. This is particularly beneficial for vehicles that undergo frequent tire changes, such as in racing applications or in regions with distinct winter and summer tire seasons. The improved wear resistance translates to longer service life for both the lug nuts and the wheel studs, potentially reducing maintenance costs over time.
Environmentally Friendly
In an era of increasing environmental awareness, the eco-friendliness of manufacturing processes has become a critical consideration. PVD coating stands out as an environmentally responsible choice for surface treatment of black titanium lug nuts. Unlike traditional coating methods such as electroplating, which often involve hazardous chemicals and generate significant amounts of waste, PVD is a clean, dry process that produces minimal environmental impact.
The PVD process typically operates in a vacuum environment and does not require the use of toxic chemicals or solvents. This eliminates the need for extensive waste treatment and disposal processes associated with wet chemical methods. Additionally, PVD coatings are often composed of inert materials that do not pose environmental risks during use or at the end of the product's life cycle.
Moreover, the efficiency of the PVD process results in minimal material waste. The precise control over the deposition process allows for optimal use of coating materials, reducing unnecessary consumption. This aligns with the principles of sustainable manufacturing and resource conservation, making PVD black coating an environmentally responsible choice for automotive components like black titanium lug nuts.
Black Titanium Lug Nuts Manufacturer
Wisdom Titanium products coating is PVD Black Coating. If you are choosing your black titanium lug nuts manufacturers, welcome to contact us at sales@wisdomtitanium.com.
References
1. Mattox, D. M. (2010). Handbook of Physical Vapor Deposition (PVD) Processing. William Andrew.
2. Martin, P. M. (2009). Handbook of deposition technologies for films and coatings: science, applications and technology. William Andrew.
3. Holmberg, K., & Matthews, A. (2009). Coatings tribology: properties, mechanisms, techniques and applications in surface engineering. Elsevier.
4. Ehiasarian, A. P. (2010). Fundamentals and applications of HIPIMS. In Plasma Surface Engineering Research and Its Practical Applications. Research Signpost.