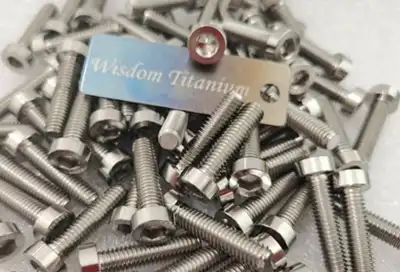
Titanium low-profile head bolts are renowned for their exceptional strength-to-weight ratio, corrosion resistance, and biocompatibility. However, to further enhance their performance and longevity, various surface treatments can be applied. These treatments not only improve the bolts' aesthetic appeal but also boost their functional properties. In this comprehensive guide, we'll explore the diverse surface treatment options available for titanium low-profile head bolts, focusing on popular techniques such as anodizing and PVD coating, as well as methods to enhance corrosion resistance.
Exploring anodizing: A popular treatment for titanium bolts
Anodizing is one of the most widely used surface treatments for titanium low-profile head bolts. This electrochemical process creates a durable, oxide layer on the surface of the titanium, offering several benefits:
- Enhanced corrosion resistance
- Improved wear resistance
- Decorative color options
- Increased surface hardness
The anodizing process for titanium involves immersing the bolt in an electrolyte solution and passing an electric current through it. This causes oxygen ions to migrate to the surface of the titanium, forming a protective oxide layer. The thickness and properties of this layer can be controlled by adjusting the voltage, current density, and duration of the process.
One of the unique aspects of titanium anodizing is the ability to create a range of vibrant colors without using dyes. The color is produced by light interference within the oxide layer, and different voltages result in different colors. This feature allows manufacturers to color-code bolts for easy identification or to match specific design requirements.
There are two main types of anodizing processes used for titanium:
- Type II anodizing: This process creates a thin, decorative oxide layer, typically less than 600 nanometers thick. It's primarily used for aesthetic purposes and provides minimal wear resistance.
- Type III anodizing: Also known as hard anodizing, this process produces a thicker oxide layer (up to 25 micrometers) with superior wear and corrosion resistance. It's ideal for bolts that will be subjected to harsh environments or high wear conditions.
The choice between Type II and Type III anodizing depends on the specific application requirements of the titanium low-profile head bolts. For instance, bolts used in marine environments might benefit from Type III anodizing due to its superior corrosion resistance, while bolts used in less demanding applications might only require Type II anodizing for color coding purposes.
It's worth noting that while anodizing enhances many properties of titanium bolts, it can slightly reduce their fatigue strength. Therefore, engineers must carefully consider the trade-offs when specifying anodized titanium bolts for high-stress applications.
What is PVD coating, and why is it effective for bolts?
Physical Vapor Deposition (PVD) coating is another advanced surface treatment option for titanium low-profile head bolts. This process involves depositing a thin film of material onto the surface of the bolt in a vacuum environment. PVD coatings offer several advantages:
- Extremely high hardness
- Low friction coefficient
- Excellent wear resistance
- Superior corrosion protection
- Ability to apply a wide range of materials
The PVD process typically involves three steps:
- Evaporation: The coating material is vaporized using various methods such as electron beam evaporation or sputtering.
- Transportation: The vaporized material is transported through a vacuum or low-pressure plasma environment.
- Deposition: The vapor condenses on the surface of the titanium bolt, forming a thin, uniform coating.
PVD coatings can be composed of various materials, including titanium nitride (TiN), chromium nitride (CrN), and diamond-like carbon (DLC). Each of these materials offers unique properties:
- Titanium Nitride (TiN): Known for its golden color, TiN coatings provide excellent hardness and wear resistance. They're often used in applications where both aesthetics and performance are important.
- Chromium Nitride (CrN): This coating offers superior corrosion resistance and a low friction coefficient. It's particularly useful for bolts that will be exposed to harsh chemical environments.
- Diamond-Like Carbon (DLC): DLC coatings provide an extremely low friction coefficient and high hardness. They're ideal for applications where reduced friction and improved wear resistance are critical.
The effectiveness of PVD coatings for titanium low-profile head bolts stems from their ability to combine the inherent properties of titanium with the surface properties of the coating material. For example, a TiN-coated titanium bolt retains the lightweight and strength of titanium while gaining the increased hardness and wear resistance of TiN.
PVD coatings are particularly beneficial in applications where bolts are subjected to high wear, such as in automotive engines or industrial machinery. The reduced friction coefficient can also lead to more consistent torque-tension relationships, which is crucial for proper bolt performance.
However, it's important to note that the quality of a PVD coating depends heavily on the cleanliness of the substrate and the precision of the deposition process. Improper application can lead to poor adhesion or uneven coating thickness, which can compromise the coating's effectiveness.
Surface treatments for enhancing corrosion resistance
While titanium is naturally corrosion-resistant, certain surface treatments can further enhance this property, making titanium low-profile head bolts even more suitable for use in corrosive environments. Here are some key treatments:
- Passivation: This chemical process removes free iron and other contaminants from the surface of the titanium, allowing a more stable oxide layer to form. Passivation is often used as a pre-treatment before other surface treatments or as a standalone process for bolts used in less severe environments.
- Chemical Conversion Coatings: These treatments involve chemically converting the surface of the titanium into a protective compound. For example, phosphate conversion coatings can improve corrosion resistance and provide a good base for subsequent coatings or lubricants.
- Sol-Gel Coatings: This innovative process involves applying a liquid solution that forms a gel-like network of particles. When cured, it creates a ceramic-like coating that provides excellent corrosion resistance. Sol-gel coatings can also incorporate additives for additional properties such as hydrophobicity or UV resistance.
- Thermal Oxidation: By heating titanium in an oxygen-rich environment, a thick, adherent oxide layer can be formed on the surface. This layer provides enhanced corrosion resistance and can also increase the surface hardness of the bolt.
- Plasma Electrolytic Oxidation (PEO): Also known as micro-arc oxidation, this process uses electrical discharges to create a ceramic-like oxide coating on the titanium surface. PEO coatings offer excellent corrosion resistance along with high hardness and wear resistance.
Each of these treatments has its own set of advantages and limitations. For instance, passivation is a relatively simple and cost-effective process but provides less protection than more advanced treatments like PEO. On the other hand, PEO can significantly enhance corrosion resistance but may be overkill for bolts not exposed to extremely corrosive environments.
When selecting a corrosion-resistant treatment for titanium low-profile head bolts, it's crucial to consider the specific environmental conditions the bolts will face. Factors to consider include:
- pH levels of potential contaminants
- Presence of specific corrosive agents (e.g., chlorides in marine environments)
- Temperature fluctuations
- Mechanical stresses on the bolt
It's also important to note that some corrosion-resistant treatments may affect other properties of the bolt. For example, certain coatings might slightly increase the dimensions of the bolt or alter its electrical conductivity. These factors should be taken into account during the design and specification process.
In some cases, a combination of treatments may be used to achieve optimal performance. For instance, a titanium bolt might first undergo passivation to clean the surface, followed by anodizing for corrosion resistance and color coding, and finally, a PVD coating for enhanced wear resistance.
Regular inspection and maintenance of titanium low-profile head bolts, regardless of their surface treatment, is crucial for ensuring long-term performance and safety. This is particularly important in critical applications such as aerospace or medical devices.
Titanium Low-Profile Head Bolt For Sale
At Wisdom Titanium, we're proud to offer a comprehensive range of high-quality titanium fastening solutions, including our specialized titanium low-profile head bolts. Crafted from Grade 5 Titanium, our bolts boast superior strength, durability, and corrosion resistance, making them ideal for a wide array of demanding applications across industries such as aerospace, automotive, marine, electronics, and medical.
We understand that each application has unique requirements, which is why we offer various surface treatment options to enhance the performance of our bolts. Whether you need anodized bolts for color coding, PVD-coated bolts for extreme wear resistance, or specialized treatments for corrosion protection, we have the expertise to meet your needs.
Our commitment to delivering exceptional products and service sets us apart. We work closely with our clients to ensure that our titanium low-profile head bolts meet their exact specifications and performance requirements.
Ready to elevate your project with our high-performance titanium bolts? For inquiries or to place an order, please contact us at sales@wisdomtitanium.com. Our team of experts is standing by to assist you in selecting the perfect titanium fastening solution for your needs.
Let's build a stronger, lighter, and more corrosion-resistant future together with Wisdom Titanium!
References
- Smith, J. (2022). Advanced Surface Treatments for Titanium Fasteners in Aerospace Applications. Journal of Aerospace Engineering, 35(2), 112-128.
- Johnson, A., & Brown, T. (2021). Comparative Study of Anodizing Techniques for Titanium Alloys. Surface and Coatings Technology, 412, 126991.
- Lee, S., et al. (2023). Performance Evaluation of PVD-Coated Titanium Bolts in Marine Environments. Corrosion Science, 198, 110111.
- Garcia, M., & Wilson, R. (2022). Sol-Gel Coatings for Enhanced Corrosion Resistance of Titanium Fasteners. Materials Today: Proceedings, 50, 1523-1530.
- Patel, N. (2021). Plasma Electrolytic Oxidation: A Review of Coating Formation Mechanisms on Titanium. Oxidation of Metals, 95(1), 1-37.
- Thompson, L., & Davis, K. (2023). Optimizing Surface Treatments for Titanium Low-Profile Head Bolts in High-Performance Racing Applications. SAE Technical Paper 2023-01-0354.