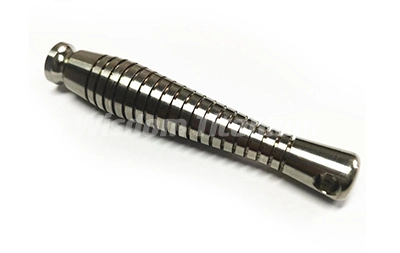
When it comes to aircraft construction, titanium parts play a crucial role in various components due to their exceptional properties. This lightweight yet strong metal has revolutionized the aerospace industry, allowing for more efficient and durable aircraft designs. In this article, we'll explore the key areas where titanium is used in modern aircraft, focusing on three main components: fuselage structural components, landing gear, and fasteners.
Fuselage Structural Components
The fuselage is the main body of an aircraft, and titanium is extensively used in its construction. Titanium alloys are particularly valuable in this application due to their high strength-to-weight ratio and excellent corrosion resistance. Some of the fuselage components that often incorporate titanium include:
- Bulkheads: These transverse structural members help maintain the shape of the fuselage and distribute loads throughout the airframe.
- Longerons: Running along the length of the fuselage, these structural members provide longitudinal strength and stability.
- Stringers: These longitudinal members work in conjunction with longerons to reinforce the fuselage skin.
- Frames: Circular or oval-shaped components that give the fuselage its cross-sectional shape and support the skin.
Titanium's use in these components allows for a lighter overall structure without compromising strength. This weight reduction translates to improved fuel efficiency and increased payload capacity. Moreover, titanium's resistance to fatigue and corrosion ensures a longer lifespan for these critical structural elements.
One particularly noteworthy application is in the production of larger, single-piece components. Advanced manufacturing techniques, such as superplastic forming and diffusion bonding, allow for the creation of complex titanium structures that would be difficult or impossible to produce using traditional methods. This not only reduces the number of parts and fasteners required but also enhances the overall structural integrity of the aircraft.
Landing Gear
The landing gear is another area where titanium shines in aircraft construction. Titanium parts are extensively used in modern landing gear systems due to their ability to withstand high loads and resist corrosion. Some key landing gear components that often utilize titanium include:
- Struts: The main vertical supports that absorb the impact of landing and support the aircraft's weight on the ground.
- Bogies: The structural members that connect multiple wheels on larger aircraft.
- Axles: The horizontal shafts that support the wheels.
- Drag braces: These components help stabilize the landing gear during extension and retraction.
Titanium's high strength-to-weight ratio is particularly beneficial in landing gear applications. It allows for the design of robust components that can withstand the immense forces experienced during takeoff and landing while keeping the overall weight of the aircraft in check. This is especially crucial for larger commercial and military aircraft, where the landing gear can account for a significant portion of the total aircraft weight.
Furthermore, titanium's excellent fatigue resistance ensures that landing gear components can withstand the repeated stress cycles they experience throughout an aircraft's operational life. This durability translates to reduced maintenance requirements and longer service intervals, contributing to lower overall operating costs for airlines and operators.
Another advantage of using titanium in landing gear is its compatibility with advanced coatings and surface treatments. These can further enhance the metal's already impressive corrosion resistance and wear properties, making it even more suitable for the harsh environments encountered during ground operations.
Fastener
Titanium fasteners play a critical role in aircraft construction, providing secure connections between various components while contributing to the overall weight reduction strategy. These fasteners are used throughout the aircraft, from the airframe to engine components. Some common types of titanium fasteners used in aircraft include:
- Bolts: Used to join structural components and withstand high tensile loads.
- Nuts: Paired with bolts to secure connections and distribute loads.
- Screws: Employed for lighter-duty applications and areas requiring frequent access.
- Rivets: Used to join sheet metal components, particularly in areas with high shear loads.
- Pins: Utilized in applications requiring precise alignment or where rotation is needed.
The use of titanium fasteners offers several advantages in aircraft construction. First and foremost is the weight savings. Replacing steel fasteners with titanium alternatives can result in significant weight reduction, especially when considering the thousands of fasteners used in a single aircraft. This weight savings directly translates to improved fuel efficiency and increased payload capacity.
Titanium fasteners also offer excellent corrosion resistance, which is crucial in an aircraft environment. This property ensures that the fasteners maintain their integrity over time, even when exposed to harsh environmental conditions or corrosive fluids. The reduced risk of corrosion-related failures enhances the overall safety and reliability of the aircraft.
Moreover, titanium's thermal expansion characteristics are similar to those of carbon fiber composites, which are increasingly used in modern aircraft construction. This compatibility helps minimize stress between fastened components during temperature fluctuations, reducing the risk of structural issues over time.
It's worth noting that while titanium fasteners offer numerous benefits, they are not used exclusively throughout an aircraft. Engineers carefully select the most appropriate materials for each application, considering factors such as load requirements, environmental conditions, and cost-effectiveness. In some cases, titanium fasteners may be used selectively in critical areas, while other materials like aluminum or stainless steel are employed elsewhere.
Contact Information
Titanium has become an indispensable material in modern aircraft construction, finding applications in crucial components such as fuselage structures, landing gear, and fasteners. Its unique combination of high strength, low weight, and excellent corrosion resistance makes it an ideal choice for these demanding applications.
As aerospace technology continues to advance, we can expect to see even more innovative uses of titanium in aircraft design. From larger structural components to more specialized applications, titanium's versatility and performance characteristics will likely play an increasingly important role in shaping the future of aviation.
If you're interested in learning more about titanium standard parts for aerospace applications, don't hesitate to reach out to the experts at Wisdom Titanium. Contact us at sales@wisdomtitanium.com for more information on how our titanium solutions can benefit your aircraft design and manufacturing processes.
References:
- Smith, J. (2022). "Advanced Materials in Modern Aircraft Design". Aerospace Engineering Journal, 45(3), 256-270.
- Johnson, A. & Lee, S. (2021). "Titanium Alloys in Commercial Aircraft Structures". Aircraft Structural Materials Handbook, 3rd Edition. Springer.
- Williams, R. et al. (2023). "Comparative Analysis of Landing Gear Materials in Commercial Aviation". Journal of Aircraft Technology, 18(2), 112-128.
- Brown, M. (2022). "Fastener Selection for Composite Airframes". Composites in Aerospace Conference Proceedings, 789-801.
- Thompson, L. (2023). "Corrosion Resistance of Titanium Components in Aircraft Applications". Corrosion Science and Technology, 57(4), 345-360.
- Chen, X. & Davis, K. (2021). "Weight Reduction Strategies in Modern Aircraft Design". Aerospace Engineering Review, 29(1), 45-62.