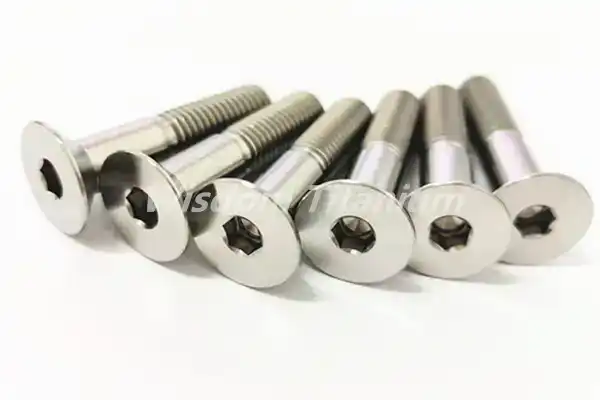
When it comes to high-performance fasteners, DIN 7991 titanium bolts are becoming increasingly popular in various industries. These bolts offer exceptional strength, durability, and corrosion resistance, making them ideal for demanding applications. In this article, we'll explore the materials used in DIN 7991 titanium bolts, their properties, and why they're preferred over other materials.
Grade 2 Titanium: The Commercially Pure Option
One of the materials commonly used for DIN 7991 titanium bolts is Grade 2 titanium. This grade is considered commercially pure titanium and offers an excellent balance of strength and corrosion resistance. Grade 2 titanium is composed of 99.2% pure titanium, with small amounts of other elements like carbon, iron, and oxygen.
Grade 2 titanium bolts are known for their:
- Excellent corrosion resistance, especially in marine environments
- Good ductility and formability
- Moderate strength (yield strength of about 275 MPa)
- Lightweight properties (density of 4.51 g/cm³)
These properties make Grade 2 titanium bolts suitable for applications where corrosion resistance is a primary concern, such as in chemical processing plants, marine equipment, and offshore structures.
Grade 5 Titanium: The High-Strength Alloy
Another material commonly used for DIN 7991 titanium bolts is Grade 5 titanium, also known as Ti-6Al-4V. This is an alpha-beta titanium alloy that contains 6% aluminum and 4% vanadium. Grade 5 titanium is renowned for its high strength-to-weight ratio and excellent mechanical properties.
Grade 5 titanium bolts offer:
- Superior strength (yield strength of about 830 MPa)
- Excellent fatigue resistance
- Good corrosion resistance
- High temperature performance (up to 400°C)
- Lightweight properties (density of 4.43 g/cm³)
These characteristics make Grade 5 titanium bolts ideal for high-stress applications in aerospace, automotive, and medical industries. They're often used in critical components where failure is not an option.
Why is titanium preferred for DIN 7991 bolts over other materials?
Titanium, whether in its commercially pure form (Grade 2) or as an alloy (Grade 5), offers several advantages over other materials commonly used for bolts, such as steel or aluminum. Here's why titanium is often the preferred choice for DIN 7991 bolts:
- Strength-to-Weight Ratio: Titanium has an exceptional strength-to-weight ratio. This means that titanium bolts can provide the same or greater strength as steel bolts while being significantly lighter. This is particularly crucial in applications where weight reduction is essential, such as in aerospace or high-performance automotive industries.
- Corrosion Resistance: Both Grade 2 and Grade 5 titanium offer excellent corrosion resistance. Titanium naturally forms a protective oxide layer when exposed to oxygen, making it highly resistant to various corrosive environments, including saltwater. This property makes titanium bolts ideal for marine applications, chemical processing, and other corrosive environments where steel bolts might fail.
- Temperature Resistance: Titanium maintains its strength at high temperatures better than many other metals. This makes titanium bolts suitable for applications involving elevated temperatures, such as in engines or industrial machinery.
- Biocompatibility: Titanium is biocompatible, meaning it's non-toxic and not rejected by the human body. This makes titanium bolts an excellent choice for medical implants and devices.
- Non-Magnetic Properties: Unlike steel, titanium is non-magnetic. This can be crucial in applications where magnetic interference needs to be minimized, such as in certain electronic or scientific equipment.
- Fatigue Resistance: Titanium, especially Grade 5, has excellent fatigue resistance. This means that titanium bolts can withstand repeated stress cycles without failing, making them ideal for applications with cyclic loading.
- Chemical Resistance: Titanium is resistant to many chemicals that would corrode other metals. This makes titanium bolts suitable for use in chemical processing plants and other harsh chemical environments.
- Low Thermal Expansion: Titanium has a lower coefficient of thermal expansion compared to many other metals. This means that titanium bolts are less likely to loosen or cause stress in joints due to temperature changes.
While titanium bolts may have a higher initial cost compared to steel or aluminum bolts, their long-term performance, durability, and unique properties often make them the most cost-effective choice in the long run, especially in demanding applications.
China DIN 7991 Titanium Bolts
Looking for top-quality titanium bolts that offer superior strength and corrosion resistance? Baoji Wisdom Titanium has got you covered! Our DIN 7991 titanium bolts are crafted from Grade 2 and Grade 5 titanium, ensuring exceptional durability and performance. With screw diameters ranging from M3 to M20 and lengths from 6mm to 250mm, we provide a wide variety of options to meet your specific needs. Whether you're working in marine, chemical, or other demanding environments, our bolts' excellent corrosion resistance guarantees long-lasting reliability. Plus, we offer polished, anodized, and customized coatings to suit your unique requirements. Don't settle for anything less—contact us today at sales@wisdomtitanium.com to learn more and get your hands on these high-performance titanium bolts!
References:
- ASTM International. (2021). ASTM B348 - Standard Specification for Titanium and Titanium Alloy Bars and Billets.
- Donachie, M. J. (2000). Titanium: A Technical Guide. ASM International.
- Boyer, R., Welsch, G., & Collings, E. W. (1994). Materials Properties Handbook: Titanium Alloys. ASM International.
- Peters, M., Kumpfert, J., Ward, C. H., & Leyens, C. (2003). Titanium alloys for aerospace applications. Advanced Engineering Materials, 5(6), 419-427.
- Leyens, C., & Peters, M. (Eds.). (2003). Titanium and titanium alloys: fundamentals and applications. John Wiley & Sons.