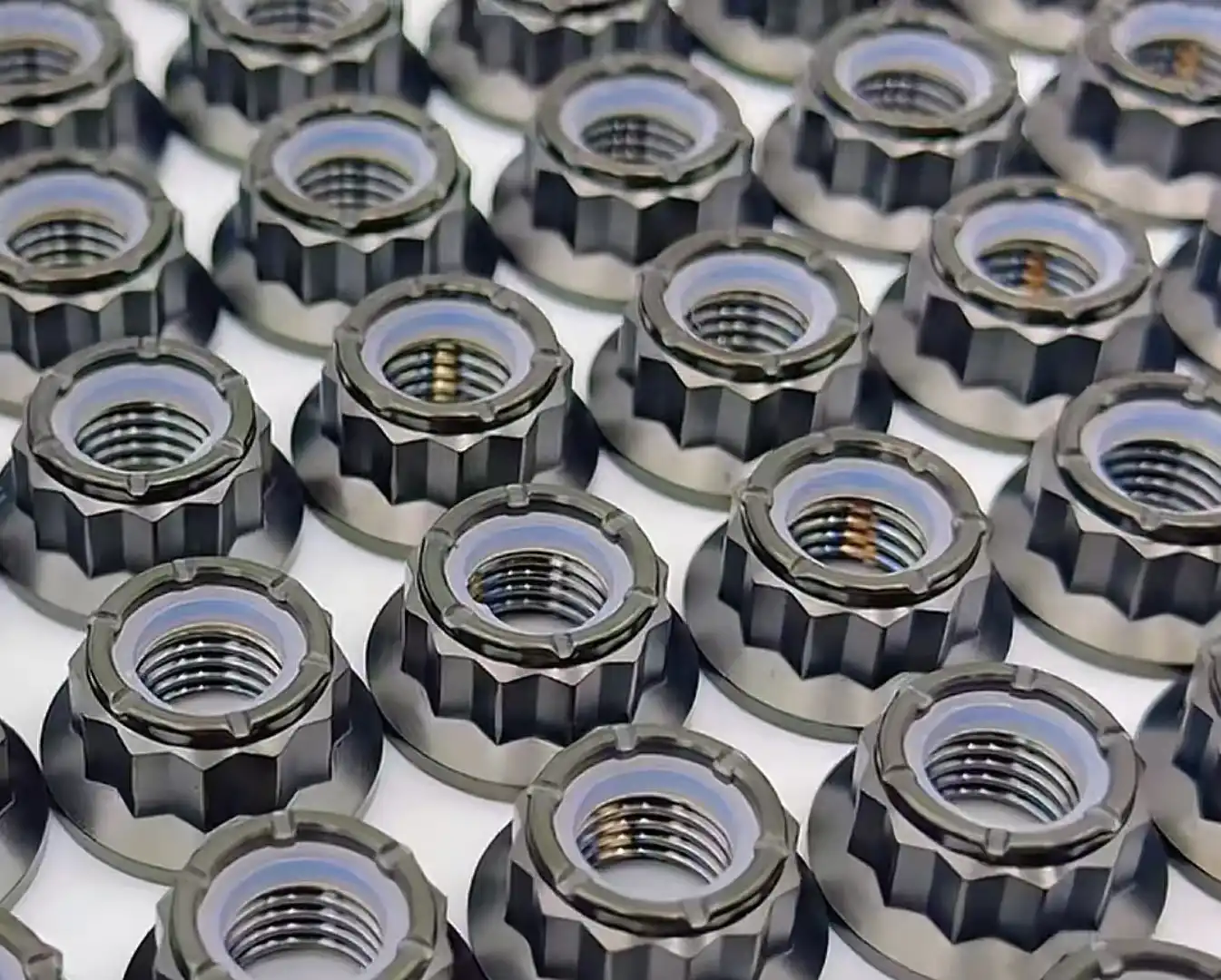
Endurance can frequently be a key concern when picking the correct nuts for your undertaking. Nuts that can endure extreme conditions and large heavy objects are crucial whether you are working on an outstanding performance motor, an aircraft usage, or any other severe industrial objective. We are going to look at some of the strongest nut materials in this post, such as Inconel, Alloy Steel, and Titanium Alloys, to assist you select which one is appropriate for what you require.
Titanium Alloys: The Lightweight Champion
Titanium alloys are renowned for their exceptional strength-to-weight ratio, making them a popular choice in industries where weight reduction is critical. These alloys offer an impressive combination of high strength, corrosion resistance, and low density. Titanium nuts are particularly valuable in aerospace and automotive applications, where every gram counts.
One of the most common titanium alloys used for nuts is Ti-6Al-4V, which offers excellent mechanical properties and fatigue resistance. These nuts can withstand extreme temperatures and harsh environments, making them ideal for use in aircraft engines, racing cars, and high-performance motorcycles. Additionally, titanium's biocompatibility makes it a go-to choice for medical implants and surgical equipment.
At Wisdom Titanium, we specialize in manufacturing high-quality titanium nuts with various thread types, including Metric, UNC, and UNF. Our commitment to safety and quality ensures that each titanium nut meets the highest standards for strength and reliability.
Alloy Steel: The Versatile Powerhouse
Alloy steel nuts have established themselves as indispensable components across a myriad of industries, thanks to their exceptional balance of strength, durability, and cost-effectiveness. These nuts are produced by adding various alloying elements, such as chromium, nickel, and molybdenum, to carbon steel. This combination results in enhanced mechanical properties, including improved tensile strength, hardness, and overall performance characteristics. Common alloy steel grades utilized for nuts include 4140, 8640, and 4340, each designed to meet specific engineering requirements.
One of the primary advantages of alloy steel nuts lies in their ability to undergo heat treatment. This process allows manufacturers to achieve targeted strength levels, tailoring the nuts' properties to suit the precise needs of various applications. For instance, in sectors such as heavy machinery, construction equipment, and automotive manufacturing, high tensile strength and exceptional fatigue resistance are crucial. Alloy steel nuts excel in these environments, ensuring reliable performance even under demanding conditions.
In addition to their mechanical properties, alloy steel nuts can be coated or plated to enhance corrosion resistance. This feature makes them suitable for use in challenging environments, where exposure to moisture and harsh chemicals can compromise the integrity of standard steel components. From bridge construction to offshore oil rigs, alloy steel nuts provide the reliability and strength necessary to secure critical structures and equipment.
Furthermore, the versatility of alloy steel extends to its compatibility with a range of fastening systems and assembly techniques, further solidifying its role as a go-to material in modern engineering. As industries continue to evolve, the demand for high-performance materials like alloy steel nuts is likely to grow, underscoring their importance in future technological advancements.
Inconel: The High-Temperature Specialist
When discussing applications involving extreme temperatures, Inconel nuts emerge as a vital component. Inconel is a family of austenitic nickel-chromium-based superalloys renowned for their remarkable heat resistance and strength at elevated temperatures. These unique properties render Inconel nuts essential in a variety of demanding industries, including aerospace, chemical processing, and nuclear power generation, where conventional materials might fail.
One of the standout features of Inconel nuts is their ability to retain strength and corrosion resistance even when exposed to temperatures exceeding 1000°C (1832°F). This exceptional heat resistance is largely attributed to the formation of a protective oxide layer on the surface of the metal, which acts as a barrier against further oxidation and degradation. Among the various grades of Inconel, Inconel 718 and Inconel 625 are particularly favored for high-temperature applications, each offering specific advantages tailored to diverse operational requirements.
In addition to their impressive thermal properties, Inconel nuts are also highly resistant to creep and stress corrosion cracking. These characteristics make them ideal for use in critical environments such as gas turbines, rocket engines, and other high-performance systems where standard nuts would likely succumb to failure. The ability of Inconel nuts to maintain integrity under such extreme conditions ensures safety and reliability in applications that demand the utmost precision and durability.
While it is true that Inconel nuts may come at a higher cost compared to conventional options, their unparalleled performance and longevity in extreme environments often justify this investment. As industries continue to push the boundaries of technology, the demand for high-performance materials like Inconel will likely grow, solidifying its role as a cornerstone in modern engineering solutions.
Choosing the Right Nut for Your Application
When selecting the strongest nut metal for your project, it's essential to consider various factors beyond just strength. These include:
- Operating temperature range
- Corrosion resistance requirements
- Weight constraints
- Cost considerations
- Compatibility with other materials in the assembly
Each of the metals discussed – Titanium Alloys, Alloy Steel, and Inconel – offers unique advantages that make them suitable for different applications. Titanium nuts in lightweight, high-strength scenarios; alloy steel provides versatility and cost-effectiveness; and Inconel shines in high-temperature environments.
Conclusion
Consulting with specialists in the area is always an excellent way in order to be sure you are selecting the best possible choice for your specific needs. Wisdom Titanium prides immense pride in its customer-focused philosophy and wealth of titanium manufacturing expertise. Our team of employees is always prepared to help you identify the most suitable titanium nuts for your particular job.
Keep in mind that finding an ideal blend of characteristics that fulfill your particular needs is far more significant than simply selecting a particularly powerful nut. A thorough review of the project's specifications and discussion with industry experts will ensure that you have chosen the most appropriate and trustworthy nuts for the task at hand, ensuring security, performance, and longevity. If you're considering titanium nuts for your project, don't hesitate to reach out to our team at sales@wisdomtitanium.com for expert advice and support.