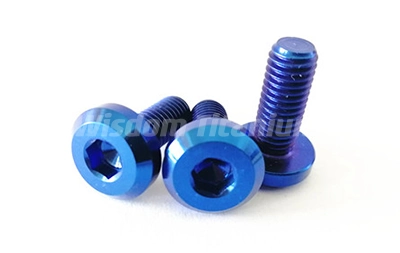
When it comes to high-performance fasteners, titanium bolts are often the go-to choice for industries ranging from aerospace to medical implants. These lightweight yet incredibly strong components are prized for their excellent strength-to-weight ratio and corrosion resistance. However, not all bolts are created equal. One crucial factor that sets apart superior titanium bolts is the method used to create their threads – specifically, rolled threads. In this article, we'll explore the significance of rolled threads in titanium bolts and why they're preferred over cut threads in many applications.
Titanium bolts with rolled threads offer several advantages over their cut-thread counterparts. These benefits stem from the unique manufacturing process that shapes the threads without removing material. Instead, the thread profile is formed by applying pressure to the bolt blank, causing the metal to flow into the desired shape. This process results in a stronger, more durable fastener that outperforms cut-thread bolts in various ways.
Increased Strength And Durability
One of the primary advantages of rolled threads in titanium bolts is the significant increase in strength and durability they provide. When threads are cut into a bolt, the process removes material and interrupts the natural grain flow of the metal. This can create weak points and stress concentrations that may lead to premature failure under load.
In contrast, the rolling process used to create threads in titanium bolts actually strengthens the material. As the metal is compressed and shaped, its grain structure is realigned and condensed. This results in a denser, more uniform structure that can withstand higher loads and resist fatigue better than cut threads. The cold working effect of thread rolling also increases the bolt's tensile strength and hardness, further enhancing its performance under stress.
For applications where reliability is critical, such as in aerospace or automotive industries, the increased strength and durability of rolled-thread titanium bolts can make a significant difference. These bolts can maintain their integrity under extreme conditions, providing peace of mind and reducing the risk of catastrophic failures.
Better Surface Finish
Another significant advantage of rolled threads in titanium bolts is the superior surface finish they provide. The rolling process creates a smooth, polished surface on the threads, which is far superior to the rougher finish typically found on cut threads. This smooth surface has several benefits that contribute to the overall performance and longevity of the bolt.
Firstly, the improved surface finish reduces friction between the bolt and nut during assembly and operation. This lower friction makes it easier to achieve proper preload during installation and helps maintain the desired clamping force over time. The smooth surface also minimizes the risk of galling, a common issue with titanium fasteners where the surfaces can cold-weld together under pressure.
Additionally, the polished surface of rolled threads provides better resistance to corrosion and wear. With fewer microscopic imperfections for corrosive agents to attack, rolled-thread titanium bolts can maintain their integrity even in harsh environments. This is particularly important in marine or chemical processing applications where exposure to corrosive substances is common.
The enhanced surface finish of rolled threads also contributes to better load distribution across the entire thread profile. This even distribution of forces helps prevent localized stress concentrations that could lead to premature failure, further enhancing the bolt's overall strength and durability.
Improved Fatigue Resistance
Fatigue resistance is an essential factor in determining the performance and reliability of fasteners, particularly in applications that involve cyclic loading or continuous vibration. In such demanding environments, the choice of materials and manufacturing processes becomes critical. Rolled threads in titanium bolts provide a notably improved fatigue resistance compared to traditional cut threads, making them an excellent option for dynamic applications where failure is not an option.
The enhanced fatigue resistance of rolled-thread titanium bolts can be attributed to several interrelated factors. First and foremost, the cold working effect that occurs during the rolling process significantly increases the metal's yield strength. This enhancement means that the bolts can endure higher levels of stress without experiencing plastic deformation under repeated loads, which is crucial for maintaining structural integrity over time.
Moreover, the smooth surface finish achieved through the rolling process reduces stress concentrations that often act as initiation points for fatigue cracks. A smoother surface allows for more uniform stress distribution, minimizing the likelihood of crack formation and subsequent failure.
In addition, the compressive stresses generated during the rolling process create a favorable residual stress pattern within the thread roots. These beneficial compressive stresses work against the tensile stresses that typically contribute to fatigue failure, thereby effectively increasing the bolt's resistance to both crack initiation and propagation.
In industries where components face constant vibration or cyclic loading—such as aerospace, automotive, and high-performance machinery—the improved fatigue resistance of rolled-thread titanium bolts can lead to significant extensions in the service life of assemblies. This not only reduces the frequency of maintenance interventions but also enhances overall safety and operational efficiency, making these bolts a preferred choice in high-stakes applications.
High-Quality Titanium Bolts
The significance of rolled threads in titanium bolts cannot be overstated. From increased strength and durability to better surface finish and improved fatigue resistance, rolled threads offer a host of benefits that make them the preferred choice for demanding applications. As industries continue to push the boundaries of performance and reliability, the superior characteristics of rolled-thread titanium bolts will undoubtedly play a crucial role in meeting these challenges.
For those in search of high-quality titanium bolts with rolled threads, Wisdom Titanium stands out as a reliable manufacturer. Their commitment to quality, combined with advanced manufacturing techniques, ensures that their bolts meet the highest standards of performance and durability. Whether you need standard fasteners or custom solutions, Wisdom Titanium's expertise in titanium bolt production, including anodizing, PVD coating, and precision etching, makes them an excellent choice for your fastening needs. For more information or to discuss your specific requirements, don't hesitate to reach out to their sales team at sales@wisdomtitanium.com.
References
1.Budynas, R. G., & Nisbett, J. K. (2015). Shigley's Mechanical Engineering Design. McGraw-Hill Education.
2. Campbell, F. C. (2006). Manufacturing Technology for Aerospace Structural Materials. Elsevier.
3. Fastenal Engineering & Design Support. (2009). Rolled Thread vs. Cut Thread.
4.ASM International. (2000). ASM Handbook, Volume 18: Friction, Lubrication, and Wear Technology.