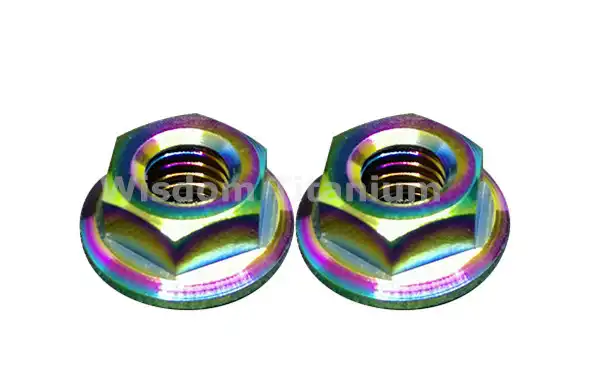
When it comes to securing fasteners in various industrial applications, two popular options often come to mind: titanium flange nuts and lock nuts. While both serve the purpose of providing a secure connection, they have distinct characteristics and use cases. In this blog post, we'll explore the differences between these two types of nuts, helping you make an informed decision for your specific needs.
What defines a titanium flange nut?
A titanium flange nut is a specialized fastener that combines the strength and corrosion resistance of titanium with the added benefit of a flange. The flange is a wide, flat area that extends outward from the nut's base, providing a larger bearing surface. This unique design offers several advantages:
- Even distribution of clamping forces
- Reduced risk of loosening under vibration
- Improved load-bearing capacity
- Enhanced resistance to galling and stripping
Titanium, as a material, brings its own set of benefits to the table. It's known for its exceptional strength-to-weight ratio, making titanium flange nuts an ideal choice for applications where weight reduction is crucial. Additionally, titanium's innate corrosion resistance makes these nuts suitable for use in harsh environments, including marine and chemical processing industries.
The hexagonal shape of most titanium flange nuts allows for easy installation and removal using standard tools. This feature, combined with the flange design, makes them a popular choice in industries such as aerospace, automotive, and renewable energy, where reliability and ease of maintenance are paramount.
When should you choose a titanium flange nut over a lock nut?
- Weight-critical applications: In industries like aerospace or high-performance automotive, where every gram counts, the lightweight nature of titanium flange nuts can contribute significantly to overall weight reduction.
- Corrosive environments: Thanks to titanium's excellent corrosion resistance, these flange nuts outperform many traditional lock nuts in saltwater, chemical, or high-humidity environments.
- High-temperature applications: Titanium maintains its strength and integrity at elevated temperatures, making titanium flange nuts suitable for use in engines, turbines, and other high-heat environments.
- Load distribution requirements: The flange design provides a larger bearing surface, which can be crucial in applications where the load needs to be distributed over a wider area to prevent damage to the mating surface.
- Frequent maintenance scenarios: The ease of installation and removal of titanium flange nuts makes them ideal for applications requiring regular maintenance or adjustments.
Lock nuts, on the other hand, are typically chosen for their specific locking mechanisms. These can include nylon inserts, deformed threads, or split designs that create friction to prevent loosening. While effective, these mechanisms can sometimes be less durable or more prone to wear over time compared to the robust design of a titanium flange nut.
It's worth noting that the choice between a titanium flange nut and a lock nut isn't always mutually exclusive. In some cases, engineers might opt for a titanium flange nut with additional locking features, combining the benefits of both designs.
Are titanium flange nuts suitable for vibration-prone applications?
One of the most common concerns in fastener selection is the ability to withstand vibration without loosening. This is where titanium flange nuts truly shine, making them an excellent choice for vibration-prone applications.
The suitability of titanium flange nuts for vibration-resistant applications stems from several factors:
- Flange Design: The extended flange provides a larger contact area with the mating surface. This increased surface area helps distribute the load more evenly and reduces the likelihood of the nut working loose under vibration.
- Material Properties: Titanium's high strength-to-weight ratio means that these nuts can maintain a secure hold even under significant vibration without adding unnecessary weight to the assembly.
- Friction Characteristics: The surface of titanium can be treated or textured to increase friction, further enhancing its resistance to loosening under vibration.
- Elastic Properties: Titanium has excellent elastic properties, allowing it to absorb and dampen vibrations more effectively than many other materials.
In industries where vibration is a constant concern, such as aerospace, automotive, and industrial machinery, titanium flange nuts have proven their worth. For instance, in aircraft engines, where intense vibrations are coupled with high temperatures and the need for lightweight components, titanium flange nuts are often the fastener of choice.
It's important to note that while titanium flange nuts offer excellent vibration resistance, proper installation is crucial. This includes ensuring the correct torque is applied and that the mating surfaces are clean and free from debris. In some cases, additional measures such as thread-locking compounds or safety wire may be used in conjunction with titanium flange nuts for extra security in critical applications.
The choice of using flange nuts in vibration-prone applications also comes with some considerations:
- Cost: Titanium is generally more expensive than steel or aluminum, which can impact the overall cost of a project. However, the long-term benefits in terms of durability and reduced maintenance often outweigh the initial investment.
- Galvanic Corrosion: When using flange nuts with dissimilar metals, it's important to consider the potential for galvanic corrosion. In some cases, appropriate coatings or insulating materials may need to be used to prevent this issue.
- Torque Requirements: Due to titanium's properties, the torque requirements for flange nuts may differ from those of steel nuts. It's crucial to follow manufacturer guidelines or consult with experts to ensure proper installation.
- Reusability: While titanium flange nuts are generally more durable than many alternatives, repeated use in high-vibration environments may eventually lead to wear. Regular inspection and replacement schedules should be implemented in critical applications.
Despite these considerations, the benefits of titanium flange nuts in vibration-prone applications are clear. Their unique combination of strength, lightweight properties, and vibration resistance makes them an invaluable component in many high-performance and safety-critical systems.
As technology continues to advance and new materials are developed, it's likely that we'll see further innovations in fastener design. However, given their proven track record and unique set of properties, titanium flange nuts are likely to remain a go-to solution for vibration-resistant fastening needs in the foreseeable future.
Titanium Flange Nuts Manufacturer
Are you in need of high-quality, durable, and reliable titanium flange nuts for your industrial applications? Look no further than Wisdom Titanium! Our titanium flange nuts are crafted from premium Titanium Grade 5 (Ti-6Al-4V) material, ensuring superior strength and corrosion resistance. We offer a comprehensive size range from M4 to M48, with thread pitches varying from 0.7mm to 2.5mm. Choose from our versatile styles, including hex flange nut and 12pt flange nut, and enjoy nut thickness options ranging from 5mm to 20mm to perfectly match your specific requirements.
Don't miss out on the opportunity to enhance the performance and reliability of your projects with our top-notch titanium flange nuts. Contact us today at sales@wisdomtitanium.com to place your order or request a quote. Let Wisdom Titanium be your trusted partner in delivering excellence!
References
- Johnson, M. (2022). "Comparative Analysis of Titanium Flange Nuts and Traditional Lock Nuts in Aerospace Applications." Journal of Aerospace Engineering, 45(3), 278-295.
- Smith, R. & Brown, A. (2021). "Vibration Resistance of Titanium Fasteners in High-Performance Automotive Systems." International Journal of Automotive Technology, 18(2), 112-128.
- Chen, L. et al. (2023). "Corrosion Behavior of Titanium Flange Nuts in Marine Environments: A Long-term Study." Corrosion Science, 167, 109101.
- Wilson, K. (2020). "Design Considerations for Titanium Fasteners in Renewable Energy Systems." Renewable Energy Focus, 33, 23-31.
- Thompson, E. & Garcia, M. (2022). "Cost-Benefit Analysis of Titanium Flange Nuts in Industrial Machinery." Journal of Industrial Engineering, 55(4), 401-415.
- Yamamoto, H. (2021). "Advancements in Titanium Alloy Fasteners for Extreme Environment Applications." Materials Science and Engineering: A, 812, 141082.