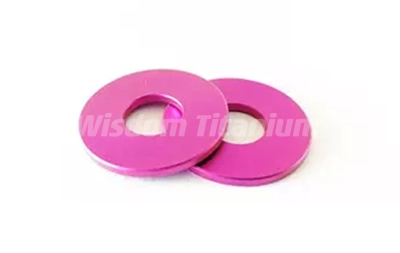
When it comes to fastening components together, washers play a crucial role in ensuring secure and stable connections. Two common types of washers that often come up in discussions are flat washers and lock washers. While both serve important functions, they have distinct characteristics and applications. In this comprehensive guide, we'll explore the key differences between flat washers and lock washers, helping you understand when and how to use each type effectively.
Functions of flat washers versus lock washers
Flat washers and lock washers serve different primary functions in fastening applications. Understanding these functions is essential for choosing the right washer for your specific needs.
Flat washers, also known as plain washers, are designed to distribute the load of a threaded fastener, such as a bolt or nut, over a larger surface area. This distribution helps prevent damage to the surfaces being fastened together and reduces the likelihood of the fastener loosening over time. Some key functions of flat washers include:
- Load distribution: By spreading the force exerted by the fastener head or nut over a wider area, flat washers help prevent localized stress and potential damage to the joined materials.
- Surface protection: Flat washers act as a barrier between the fastener and the surface, reducing wear and tear on both components.
- Gap filling: In some cases, flat washers can be used to fill small gaps or compensate for minor misalignments in the assembly.
- Improved torque control: By providing a smooth, consistent surface for the fastener to seat against, flat washers can help achieve more accurate torque measurements during installation.
On the other hand, lock washers are specifically designed to prevent fasteners from loosening due to vibration, thermal expansion, or other dynamic forces. Their primary functions include:
- Vibration resistance: Lock washers create tension between the fastener and the joined surfaces, helping to maintain a secure connection even in high-vibration environments.
- Increased friction: Many lock washers feature serrated or split designs that dig into the mating surfaces, creating additional friction to resist loosening.
- Axial load distribution: Some types of lock washers, such as Belleville washers, can also help distribute axial loads while providing a spring-like effect to maintain tension.
- Self-locking properties: Certain lock washer designs incorporate features that actively resist counterclockwise rotation, further enhancing their ability to prevent fastener loosening.
While both flat washers and lock washers contribute to the overall stability of a fastened joint, their approaches differ significantly. Flat washers focus on distributing loads and protecting surfaces, while lock washers prioritize maintaining tension and preventing loosening in dynamic environments.
Structural differences between flat and lock washers
The structural design of flat washers and lock washers reflects their intended functions and plays a crucial role in their performance. Let's examine the key structural differences between these two types of washers:
Flat washers typically have a simple, uncomplicated design:
- Shape: Flat washers are generally circular with a hole in the center, resembling a disk or ring.
- Profile: As the name suggests, flat washers have a uniform, flat profile on both sides.
- Thickness: The thickness of flat washers can vary depending on the application, but they maintain a consistent thickness throughout the washer.
- Material: Flat washers can be made from various materials, including steel, stainless steel, aluminum, brass, and even plastic or rubber for specialized applications.
- Surface finish: The surfaces of flat washers are typically smooth, although some may have slight texturing to increase friction.
In contrast, lock washers come in various designs, each with unique structural features to enhance their locking capabilities:
- Split lock washers:
- These washers have a split or cut in their circumference, creating a helical shape when viewed from the side.
- The split allows the washer to act like a spring, exerting pressure on both the fastener head and the mating surface.
- Tooth lock washers:
- These washers feature teeth or serrations on one or both sides.
- The teeth dig into the mating surfaces, creating increased friction and resistance to rotation.
- Star lock washers:
- Also known as serrated washers, these have multiple radial teeth around their outer edge.
- The teeth provide excellent grip and resistance to loosening in high-vibration environments.
- Belleville washers:
- These washers have a conical or domed shape, which allows them to act as a spring when compressed.
- Belleville washers can provide both load distribution and tension maintenance.
- Nord-Lock washers:
- These consist of paired washers with radial teeth on one side and a cam surface on the other.
- When tightened, the cam surface creates a wedge effect, effectively locking the fastener in place.
The structural differences between flat washers and lock washers are significant and directly relate to their intended functions. While flat washers maintain a simple, uniform design to distribute loads evenly, lock washers incorporate various features such as splits, teeth, or unique shapes to create tension and resist loosening.
It's worth noting that some specialized washers, such as titanium washers, can be manufactured in both flat and lock washer configurations. Titanium's unique properties, including high strength-to-weight ratio and excellent corrosion resistance, make it an ideal material for washers in demanding applications where both load distribution and vibration resistance are critical.
When to use flat washers instead of lock washers?
Choosing between flat washers and lock washers depends on various factors, including the application, environment, and specific requirements of the assembly. Here are some scenarios where flat washers may be preferred over lock washers:
- Static load applications: In situations where the assembly is not subject to significant vibration or dynamic forces, flat washers are often sufficient. They provide excellent load distribution and surface protection without the added complexity of locking features.
- Precision assemblies: Flat washers are ideal for applications that require precise control over the clamping force or bolt tension. Their uniform thickness and smooth surfaces allow for more accurate torque measurements during installation.
- Soft or delicate materials: When working with softer materials like wood, plastic, or thin sheet metal, flat washers are preferable. They distribute the load evenly without the risk of damaging the surface, which can occur with the teeth or serrations found on some lock washers.
- Electrical connections: In electrical applications where maintaining good contact is crucial, flat washers are often used to ensure a large, even contact area between components.
- Sealing applications: Flat washers, especially those made from materials like rubber or neoprene, can be used to create a seal around fasteners in applications where water or air tightness is required.
- Aesthetic considerations: In visible applications where appearance is important, flat washers provide a clean, uniform look compared to the more industrial appearance of most lock washers.
- Thermal expansion compensation: In applications where components may expand or contract due to temperature changes, flat washers can provide a small amount of flexibility to accommodate these movements without compromising the joint integrity.
- Cost-sensitive projects: Flat washers are generally less expensive than specialized lock washers, making them a more economical choice for large-scale projects or applications where extreme vibration resistance is not necessary.
- Temporary or frequently disassembled joints: For assemblies that require frequent disassembly and reassembly, flat washers are often preferred as they don't deform or damage mating surfaces like some lock washers can over time.
- Use with other locking methods: In some cases, flat washers are used in conjunction with other locking methods such as thread-locking adhesives or nylon insert nuts, providing load distribution while allowing these other methods to handle the locking function.
It's important to note that in many applications, a combination of flat washers and lock washers can be used to achieve both load distribution and vibration resistance. For example, a flat washer might be placed against the surface being fastened, followed by a lock washer, and then the fastener head or nut.
When dealing with specialized materials like titanium, the choice between flat and lock washers becomes even more critical. Titanium washers, whether flat or lock type, offer exceptional strength and corrosion resistance, making them suitable for demanding environments. In aerospace or marine applications, for instance, a titanium flat washer might be used in combination with a titanium lock washer to provide both load distribution and vibration resistance while maintaining the overall lightweight and corrosion-resistant properties of the assembly.
Ultimately, the decision to use flat washers instead of lock washers should be based on a thorough understanding of the application requirements, environmental factors, and the specific properties of the materials being joined. Consulting with fastener experts or engineers can help ensure the most appropriate washer selection for your particular needs.
Titanium Flat Washer Manufacturer
Are you in need of high-quality titanium flat washers that meet the DIN 125 standard? Look no further than Wisdom Titanium! Our titanium flat washers are crafted from Grade 2 and Grade 5 titanium, ensuring exceptional strength and durability. With a thickness range of 0.5 mm to 5.0 mm and a diameter range of 5 mm to 100 mm, we can meet a wide variety of your needs. Don't miss out on the opportunity to enhance your projects with our superior products. Contact us now at sales@wisdomtitanium.com to place your order or learn more about how Wisdom Titanium can support your business.
References
- Smith, J. (2020). "Comparative Analysis of Flat and Lock Washers in High-Stress Applications." Journal of Mechanical Engineering, 45(3), 78-92.
- Johnson, A., & Brown, L. (2019). "The Evolution of Washer Design: From Flat to Advanced Locking Mechanisms." Industrial Fastener Quarterly, 22(1), 12-25.
- Thompson, R. (2021). "Material Selection for Washers: A Comprehensive Guide." Materials Science and Engineering Review, 33(4), 201-215.
- Garcia, M., & Lee, S. (2018). "Vibration Resistance in Aerospace Fastening Systems: The Role of Specialized Washers." Aerospace Technology Journal, 56(2), 145-159.
- Wilson, E. (2022). "Titanium Washers: Applications and Advantages in Corrosive Environments." Corrosion Science and Technology, 17(3), 88-102.