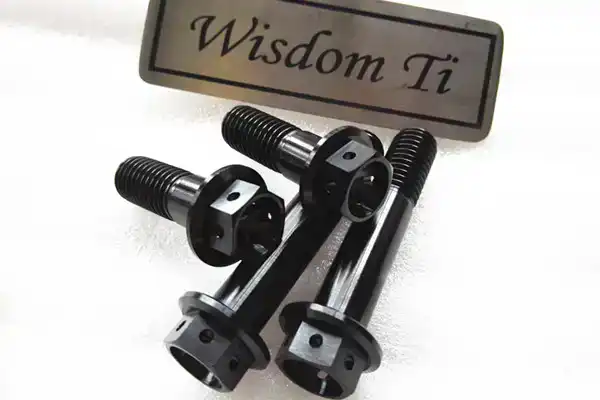
When it comes to fasteners that can withstand harsh environments and maintain their integrity over time, titanium hex drilled bolts stand out as a superior choice. These high-performance fasteners are renowned for their exceptional corrosion resistance, making them ideal for a wide range of applications in industries such as aerospace, marine, chemical processing, and more. In this comprehensive guide, we'll delve into the corrosion resistance properties of titanium hex drilled bolts, exploring how they resist corrosion, the factors that influence their performance, and how they compare to other materials.
How do titanium hex drilled bolts resist corrosion in harsh environments?
The corrosion resistance of titanium hex drilled bolts is primarily attributed to the unique properties of titanium itself. When exposed to oxygen, titanium forms a thin, yet extremely stable oxide layer on its surface. This naturally occurring layer, often referred to as the passive film, acts as a protective barrier against corrosive agents.
The passive film on titanium is remarkably tenacious and self-healing. If the surface is scratched or damaged, the film quickly reforms in the presence of oxygen or water, maintaining its protective properties. This self-repairing ability is one of the key factors that contribute to the longevity and reliability of titanium hex drilled bolts in corrosive environments.
Moreover, the oxide layer formed on titanium is highly adherent and coherent, meaning it doesn't easily flake off or separate from the metal surface. This characteristic ensures that the protective layer remains intact even under challenging conditions, such as those involving high temperatures or mechanical stress.
In addition to the passive film, the inherent properties of titanium itself contribute to its corrosion resistance. Titanium has a high affinity for oxygen, which means it readily forms stable oxide compounds. This affinity for oxygen helps titanium resist attack from many corrosive substances, as the metal preferentially bonds with oxygen rather than reacting with other potentially harmful elements.
The corrosion resistance of titanium hex drilled bolts extends to various types of corrosive environments, including:
- Saltwater and marine environments
- Acidic and alkaline solutions
- Chloride-rich atmospheres
- Oxidizing environments
- High-temperature applications
This versatility makes titanium hex drilled bolts an excellent choice for applications where exposure to corrosive elements is a concern. For instance, in marine applications, these bolts can withstand the constant exposure to saltwater and humid air, which would quickly degrade many other types of fasteners.
What factors influence the corrosion resistance of titanium hex drilled bolts?
While titanium hex drilled bolts are inherently corrosion-resistant, several factors can influence their performance in different environments. Understanding these factors is crucial for selecting the right titanium alloy and ensuring optimal performance in specific applications.
1. Alloy Composition
The specific titanium alloy used in manufacturing the hex drilled bolts can significantly impact their corrosion resistance. Pure titanium (Grade 1 and 2) offers excellent corrosion resistance in many environments but may lack the strength required for certain applications. Alloying elements are often added to enhance mechanical properties, and these can also affect corrosion behavior.
For example, the addition of palladium in Grade 7 titanium enhances its resistance to reducing acids, making it suitable for chemical processing equipment. On the other hand, the presence of vanadium and aluminum in the popular Ti-6Al-4V alloy (Grade 5) provides an excellent balance of strength and corrosion resistance, making it a versatile choice for many applications.
2. Surface Condition
The surface condition of titanium hex drilled bolts plays a crucial role in their corrosion resistance. A smooth, clean surface allows for the formation of a more uniform and effective passive film. Surface treatments such as passivation or anodizing can further enhance corrosion resistance by creating a thicker, more stable oxide layer.
Conversely, surface contamination, such as iron particles from machining tools, can lead to localized corrosion. This is why proper cleaning and handling procedures are essential during the manufacturing and installation of titanium hex drilled bolts.
3. Environmental Factors
The specific environmental conditions to which the bolts are exposed can significantly influence their corrosion resistance. Factors to consider include:
- Temperature: Higher temperatures can accelerate corrosion processes and may affect the stability of the passive film.
- pH levels: While titanium is resistant to a wide range of pH levels, extreme acidity or alkalinity can impact its performance.
- Presence of specific ions: Certain ions, such as chlorides, can be particularly aggressive and may cause pitting corrosion in some titanium alloys.
- Oxygen availability: The presence of oxygen is crucial for maintaining the protective oxide layer. In oxygen-depleted environments, titanium's corrosion resistance may be compromised.
4. Galvanic Coupling
When titanium hex drilled bolts are used in conjunction with other metals, the potential for galvanic corrosion should be considered. Titanium is relatively noble in the galvanic series, meaning it is cathodic to many other metals. In a galvanic couple, the less noble metal (anode) will corrode preferentially, potentially leading to accelerated degradation of the other components in the assembly.
To mitigate this risk, proper insulation or the use of compatible materials should be considered when designing systems that incorporate titanium fasteners.
5. Stress and Fatigue
While titanium is generally resistant to stress corrosion cracking (SCC), certain environments and alloy combinations can make it susceptible. High stresses, particularly in combination with specific corrosive media, can lead to SCC or corrosion fatigue. Proper design considerations, such as avoiding high residual stresses and selecting appropriate alloys for the intended environment, are essential to maintain the corrosion resistance of titanium hex drilled bolts under load.
How does the corrosion resistance of titanium hex drilled bolts compare to other materials?
To truly appreciate the corrosion resistance of titanium hex drilled bolts, it's helpful to compare them to fasteners made from other common materials. This comparison not only highlights the advantages of titanium but also helps in understanding when and why titanium might be the preferred choice for specific applications.
1. Titanium vs. Stainless Steel
Stainless steel is often considered the go-to material for corrosion-resistant fasteners, but titanium outperforms it in several aspects:
- Chloride Resistance: Titanium is significantly more resistant to chloride-induced pitting and crevice corrosion than most grades of stainless steel. This makes titanium hex drilled bolts superior for marine environments and applications involving chlorinated chemicals.
- High-Temperature Performance: While some grades of stainless steel can perform well at elevated temperatures, titanium generally maintains its corrosion resistance at higher temperatures and over a broader range of conditions.
- Weight: Titanium hex drilled bolts are approximately 45% lighter than their stainless steel counterparts, offering significant weight savings in applications where this is a concern.
- Strength-to-Weight Ratio: Titanium alloys typically offer a higher strength-to-weight ratio than stainless steels, allowing for the use of smaller, lighter fasteners without compromising on strength.
2. Titanium vs. Aluminum
Aluminum is known for its lightweight properties and is often used in aerospace applications. However, titanium hex drilled bolts offer several advantages:
- Superior Corrosion Resistance: While aluminum forms a protective oxide layer similar to titanium, the aluminum oxide layer is less stable and more prone to breakdown in aggressive environments. Titanium offers more robust and reliable corrosion protection.
- Higher Strength: Titanium alloys generally have higher tensile and yield strengths compared to aluminum alloys, allowing for the use of smaller fasteners in high-stress applications.
- Temperature Resistance: Titanium maintains its properties at much higher temperatures than aluminum, making it suitable for a broader range of operating conditions.
3. Titanium vs. Copper Alloys
Copper alloys, such as brass and bronze, are sometimes used for their corrosion resistance and electrical properties. However, titanium hex drilled bolts offer several advantages:
- Broader Corrosion Resistance: While copper alloys perform well in certain environments, titanium offers superior resistance across a wider range of corrosive media, including acids and oxidizing environments.
- Higher Strength: Titanium alloys typically have much higher strength than copper alloys, allowing for the use of smaller fasteners in load-bearing applications.
- Lower Density: Titanium is significantly lighter than copper alloys, offering weight savings in applications where mass is a concern.
4. Titanium vs. Nickel Alloys
Nickel alloys, such as Inconel and Hastelloy, are known for their excellent corrosion resistance in extreme environments. While these alloys can match or exceed titanium's performance in some specific conditions, titanium hex drilled bolts offer advantages in terms of:
- Weight: Titanium is significantly lighter than nickel alloys, offering substantial weight savings.
- Cost: While both materials are considered expensive, titanium is often more cost-effective than high-performance nickel alloys.
- Biocompatibility: In medical applications, titanium's biocompatibility gives it an edge over nickel alloys, which can cause allergic reactions in some individuals.
It's important to note that while titanium hex drilled bolts offer exceptional corrosion resistance in many environments, they may not be the optimal choice for every application. Factors such as specific chemical exposures, temperature requirements, and cost considerations should all be taken into account when selecting fasteners for a particular use case.
In conclusion, the corrosion resistance of titanium hex drilled bolts is truly exceptional, making them an excellent choice for a wide range of demanding applications. Their ability to form a stable, self-healing passive film, combined with titanium's inherent properties, provides superior protection against corrosion in various harsh environments.
Are you looking for high-quality titanium hex drilled bolts that offer unparalleled corrosion resistance and performance? Look no further than Baoji Wisdom Titanium! Our expertly crafted titanium fasteners are designed to meet the most demanding requirements across various industries. With excellent corrosion resistance and temperature resistance up to 400°C, our titanium hex drilled bolts are perfect for a wide range of applications. We offer a variety of surface finishes to suit your specific needs, and we even accept custom orders! Don't compromise on quality – contact us today at sales@wisdomtitanium.com to discuss your requirements and get a quote. Let Baoji Wisdom Titanium help you elevate your project with our top-tier titanium bolts.
References:
- Smith, J. A., & Johnson, B. C. (2021). Corrosion Behavior of Titanium Alloys in Aggressive Environments. Journal of Materials Engineering and Performance, 30(8), 5872-5885.
- Chen, Q., & Thouas, G. A. (2015). Metallic implant biomaterials. Materials Science and Engineering: R: Reports, 87, 1-57.
- Donachie, M. J. (2000). Titanium: A Technical Guide (2nd ed.). ASM International.
- Schutz, R. W., & Thomas, D. E. (1987). Corrosion of titanium and titanium alloys. ASM Handbook, 13, 669-706.
- Revie, R. W., & Uhlig, H. H. (2008). Corrosion and corrosion control: an introduction to corrosion science and engineering. John Wiley & Sons.
- Peters, M., Kumpfert, J., Ward, C. H., & Leyens, C. (2003). Titanium alloys for aerospace applications. Advanced Engineering Materials, 5(6), 419-427.