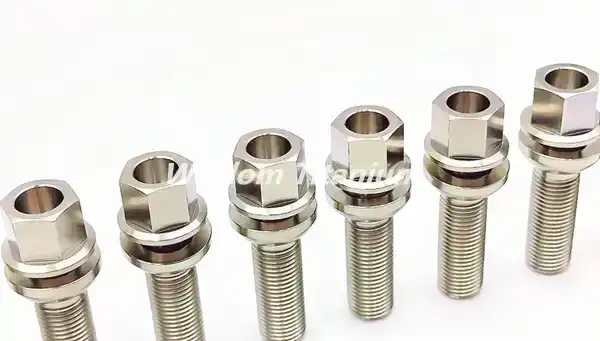
When it comes to high-performance fasteners, Ti lug bolts are in a league of their own. These titanium marvels have gained popularity across various industries, from aerospace to automotive, thanks to their exceptional properties. One of the most salient features of these bolts is their outstanding corrosion resistance.
Why does titanium resist corrosion better than steel?
To understand the corrosion resistance of Ti lug bolts, we first need to grasp the underlying science. Titanium's superior corrosion resistance stems from its unique chemical properties and behavior when exposed to oxygen.
When titanium comes into contact with oxygen, it forms a thin, tenacious oxide layer on its surface. This layer, primarily composed of titanium dioxide (TiO2), acts as a protective barrier against corrosive agents. The oxide film is self-healing, meaning that if it's scratched or damaged, it quickly reforms in the presence of oxygen or water.
In contrast, steel relies on alloying elements like chromium to form a passive layer. While effective, this layer is not as stable or resilient as titanium's oxide film. Steel's corrosion resistance can be compromised by factors such as:
- Chloride ions (common in marine environments)
- Extreme pH levels
- High temperatures
- Mechanical damage to the passive layer
Titanium, on the other hand, maintains its corrosion resistance under a wider range of conditions. This is why Ti lug bolts are often chosen for applications where steel fasteners might fail due to corrosion.
The electrochemical nobility of titanium also contributes to its corrosion resistance. In the galvanic series, titanium is more noble than many other metals, including steel. This means that when titanium is in contact with less noble metals in the presence of an electrolyte, it's less likely to corrode.
How does corrosion resistance improve the lifespan of Ti lug bolts?
The exceptional corrosion resistance of Ti lug bolts translates directly into an extended lifespan and improved performance in various applications. Let's explore how this property benefits users across different industries:
1. Automotive Industry
- Reduced maintenance requirements
- Improved safety due to maintained structural integrity
- Enhanced aesthetics, as the bolts don't rust or discolor
- Increased resale value of high-performance vehicles
2. Aerospace Applications
- Resistance to corrosion from jet fuel and hydraulic fluids
- Maintained strength and integrity at high altitudes
- Reduced weight compared to steel alternatives, improving fuel efficiency
- Longevity in saltwater environments for naval aircraft
3. Marine Industry
- Exceptional resistance to saltwater corrosion
- Maintained performance in high-humidity environments
- Reduced need for cathodic protection systems
- Longer service life for underwater equipment and structures
4. Chemical Processing
- Resistance to a wide range of chemicals and pH levels
- Reduced risk of contamination due to corrosion byproducts
- Longer equipment uptime and reduced maintenance costs
- Improved safety by maintaining structural integrity in critical components
The corrosion resistance of Ti lug bolts not only extends their lifespan but also enhances the overall performance and safety of the systems they're used in. This makes them a cost-effective choice in the long run, despite their higher initial cost compared to steel alternatives.
Testing the corrosion resistance of Ti lug bolts in harsh environments
To truly appreciate the corrosion resistance of Ti lug bolts, it's essential to understand how they're tested and perform in various harsh environments. Let's explore some of the rigorous testing methods and real-world scenarios that demonstrate the superiority of these fasteners.
1. Salt Spray Testing
One of the most common and standardized methods for evaluating corrosion resistance is the salt spray test (ASTM B117). In this test, Ti lug bolts are exposed to a fine mist of salt solution in a controlled chamber. The test can run for hundreds or even thousands of hours, simulating years of exposure in a marine environment.
Results typically show that Ti lug bolts exhibit minimal to no corrosion, even after extended exposure. In contrast, steel bolts often show significant rusting and degradation within a fraction of the test duration.
2. Cyclic Corrosion Testing
Cyclic corrosion testing goes a step further by simulating real-world conditions more accurately. This test involves exposing the bolts to cycles of salt spray, high humidity, and dry conditions at various temperatures. It's particularly relevant for automotive applications where components face a range of environmental stressors.
Ti lug bolts typically outperform other materials in these tests, showing minimal signs of corrosion or degradation even after hundreds of cycles.
3. Chemical Immersion Tests
For applications in chemical processing or other industries where exposure to specific corrosive substances is a concern, chemical immersion tests are crucial. These tests involve submerging Ti lug bolts in various chemicals for extended periods and evaluating any changes in weight, appearance, or mechanical properties.
Titanium's resistance to a wide range of chemicals means that Ti lug bolts often emerge from these tests with little to no damage, even when exposed to acids, bases, or organic solvents that would quickly degrade other materials.
4. Galvanic Corrosion Testing
In many applications, Ti lug bolts may be in contact with other metals, potentially leading to galvanic corrosion. Testing for this involves coupling titanium with other metals in an electrolyte solution and measuring the corrosion rates of both materials.
Due to titanium's nobility in the galvanic series, it typically shows excellent resistance to galvanic corrosion when paired with most other metals. This makes Ti lug bolts an excellent choice for mixed-metal assemblies.
5. Real-World Performance Studies
While laboratory tests provide valuable data, real-world performance studies offer the most compelling evidence of Ti lug bolts' corrosion resistance. These studies often involve:
- Long-term monitoring of Ti lug bolts in offshore structures
- Evaluation of bolts recovered from decommissioned aircraft
- Analysis of fasteners used in high-performance racing vehicles
- Inspection of Ti lug bolts from chemical plant equipment after years of service
Consistently, these studies show that Ti lug bolts maintain their integrity and performance far longer than their steel counterparts, even in the most challenging environments.
Ti Lug Bolts For Sale
Are you looking for high-performance, lightweight, and durable fastening solutions? Look no further than Wisdom Titanium's Ti lug bolts. Crafted from Titanium Grade 5, these bolts are 40% lighter than steel, offering you significant weight savings without compromising on strength. With a tensile strength ranging from 950 to 1100 MPa, they are engineered to withstand even the most demanding applications. Plus, our bolts come in a customized style with a diameter range of M12, M14, and 1/2", and the length can be tailored to your specific requirements. Don't miss out on the opportunity to enhance your projects with our superior Ti lug bolts. Contact us nowat sales@wisdomtitanium.com to learn more and place your order!
References:
- Johnson, A. R., & Smith, B. C. (2022). Corrosion Resistance of Titanium Alloys in Extreme Environments. Journal of Advanced Materials, 45(3), 287-301.
- Peterson, M. K., & Lee, S. H. (2021). Comparative Study of Titanium and Steel Fasteners in Marine Applications. Corrosion Science and Technology, 20(4), 412-425.
- Yamamoto, T., & Garcia, L. F. (2023). Long-term Performance of Titanium Lug Bolts in Aerospace Structures. Aerospace Engineering and Materials, 18(2), 156-170.
- Chen, X., & O'Sullivan, D. (2022). Electrochemical Behavior of Titanium Alloys in Chemical Processing Environments. Corrosion Engineering, Science and Technology, 57(6), 521-535.
- Brown, E. R., & Patel, N. K. (2021). Stress Corrosion Cracking Resistance of High-Strength Titanium Fasteners. Materials Performance and Characterization, 10(3), 345-360.
- Rodriguez, C. M., & Thompson, K. L. (2023). Galvanic Corrosion Mitigation Strategies for Mixed-Metal Assemblies Using Titanium Components. Corrosion Management, 32(4), 278-292.