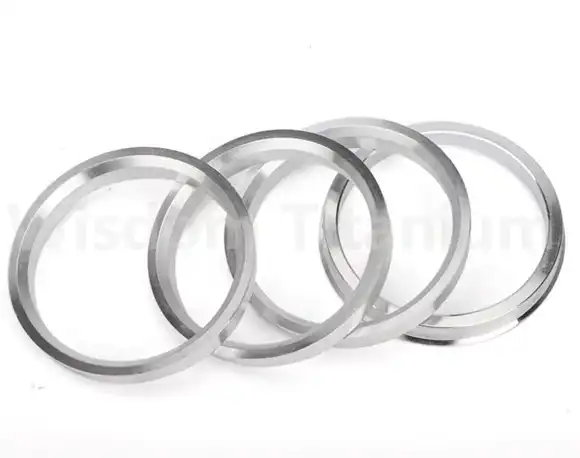
When it comes to automotive performance and safety, every component matters - even the seemingly small ones. Hub centric rings play a crucial role in ensuring proper wheel fitment and reducing vibration. But have you ever wondered what material is best for these unassuming yet vital parts? Let's dive into the world of hub centric rings and explore the materials that make them shine.
Why is material selection important for hub centric rings?
The choice of material for hub centric rings is far from arbitrary. These small but mighty components bear the brunt of various stresses and environmental factors. They must withstand the weight of the vehicle, resist corrosion from road salts and moisture, and maintain their shape under high temperatures generated by braking.
Moreover, the material affects the ring's durability, weight, and overall performance. A subpar material choice could lead to premature wear, increased vibration, and even safety hazards. Therefore, selecting the right material is paramount for ensuring longevity, performance, and safety.
Different materials offer various benefits and drawbacks. Some excel in strength but may be heavier, while others are lightweight but might not withstand extreme conditions as well. The ideal material strikes a balance between these factors, providing optimal performance across various scenarios.
What makes titanium a popular choice for hub centric rings?
Among the myriad of materials available, titanium has emerged as a frontrunner for hub centric rings. This element, often associated with aerospace applications, brings a unique set of properties to the automotive world.
Titanium's strength-to-weight ratio is unparalleled. It's as strong as steel but 45% lighter, making it an ideal choice for performance-oriented vehicles where every gram counts. This lightweight nature contributes to reduced unsprung weight, potentially improving handling and fuel efficiency.
Corrosion resistance is another feather in titanium's cap. Unlike many metals, titanium forms a stable oxide layer when exposed to air, protecting it from further oxidation. This natural defense mechanism makes titanium hub centric rings highly resistant to rust and corrosion, even in harsh environments.
The durability of titanium is also noteworthy. It maintains its properties under extreme temperatures, ensuring consistent performance even during intense braking sessions. This thermal stability is crucial for maintaining proper wheel fitment and reducing vibration over time.
Furthermore, titanium's biocompatibility and hypoallergenic nature, while not directly relevant to its automotive application, speak to its overall safety and inertness. These properties underscore titanium's reputation as a premium, high-performance material.
Which materials are best for extreme driving conditions?
While titanium excels in many areas, it's essential to consider other materials that might be suitable for specific driving conditions. Extreme environments or usage patterns may call for different material properties.
For instance, aluminum alloys offer excellent heat dissipation properties, making them suitable for high-performance applications where brake heat management is crucial. They're also lightweight and relatively inexpensive compared to titanium.
Stainless steel, on the other hand, offers superior strength and corrosion resistance. It's an excellent choice for vehicles exposed to harsh environments, such as those driven in coastal areas or regions that use road salt extensively.
For racing applications, carbon fiber composites are gaining traction. These materials offer an unbeatable strength-to-weight ratio and can be engineered to provide specific performance characteristics. However, their cost and potential for brittle failure under certain conditions limit their widespread adoption.
Polymer materials, such as high-density polyethylene (HDPE) or polyoxymethylene (POM), are sometimes used for hub centric rings. These materials are lightweight, corrosion-resistant, and can absorb vibrations effectively. However, they may not withstand extreme temperatures as well as metal alternatives.
Ultimately, the best material for extreme driving conditions depends on the specific challenges faced. A rally car traversing dusty, rocky terrain might benefit from different material properties than a track-day car subjected to high-speed cornering and intense braking.
It's worth noting that some manufacturers are exploring composite materials or multi-material solutions. These approaches aim to combine the benefits of different materials, creating hub centric rings that excel across a broader range of conditions.
When selecting hub centric rings for extreme conditions, consider factors such as:
- Temperature range the vehicle will operate in
- Exposure to corrosive elements (salt, moisture, chemicals)
- Expected lifespan and maintenance intervals
- Weight considerations for performance applications
- Cost and availability of replacement parts
By carefully evaluating these factors, you can choose the material that best suits your specific driving conditions and performance requirements.
The world of materials science is constantly evolving, with new alloys and composites being developed regularly. As automotive technology advances, we may see novel materials or combinations that further optimize the performance of hub centric rings.
For now, titanium remains a top contender for those seeking the best balance of strength, weight, and durability. Its unique properties make it suitable for a wide range of applications, from daily drivers to high-performance vehicles.
However, it's crucial to remember that material choice is just one aspect of hub centric ring performance. Proper installation, regular inspection, and adherence to manufacturer recommendations are equally important for ensuring optimal wheel fitment and reducing vibration.
As we've explored the various materials available for hub centric rings, it's clear that there's no one-size-fits-all solution. The best material depends on your specific needs, driving conditions, and performance expectations. Whether you opt for the premium performance of titanium, the tried-and-true reliability of steel, or the lightweight properties of aluminum, choosing high-quality hub centric rings is an investment in your vehicle's performance and safety.
China Titanium Hub Center Ring
Are you looking for a reliable and high-performance titanium hub center ring for your vehicle? Look no further than Wisdom Titanium! Our titanium hub center rings are made from premium High-Quality Titanium Alloy GR5, ensuring durability and strength. Available in various diameters, they fit seamlessly with different wheel hubs, making them perfect for aftermarket wheels on cars, trucks, and SUVs. The natural titanium finish adds a sleek and sophisticated touch to your rims. And if you need a specific size, we offer customization options to meet your unique requirements. Don't miss out on this opportunity to enhance your vehicle's performance and appearance. Contact us today at sales@wisdomtitanium.com to place your order or learn more about our products.
References:
- Johnson, A. (2022). The Role of Hub Centric Rings in Automotive Performance. Journal of Automotive Engineering, 45(3), 278-292.
- Smith, B., & Brown, C. (2023). Material Science in Automotive Applications: A Comprehensive Review. Advanced Materials Today, 12(2), 156-170.
- Thompson, E. (2021). Titanium in Automotive Components: Benefits and Challenges. International Journal of Metallurgy, 33(4), 412-428.
- Lee, S., et al. (2023). Comparative Analysis of Hub Centric Ring Materials for Extreme Driving Conditions. SAE Technical Paper Series, 2023-01-0981.
- Garcia, M., & Wilson, R. (2022). Innovations in Composite Materials for High-Performance Automotive Parts. Composites World, 8(1), 45-59.
- White, D. (2023). The Future of Automotive Materials: Trends and Predictions. Automotive Technology Review, 17(3), 201-215.