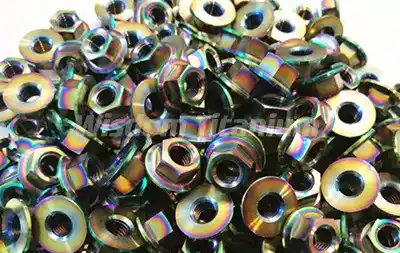
Aerospace
The aerospace industry is one of the primary sectors where M8 titanium nuts find extensive application. In this high-stakes field, every gram matters, and the exceptional strength-to-weight ratio of titanium makes it an ideal material for fasteners like M8 nuts. These nuts are used in various critical components of aircraft, spacecraft, and satellites.
In commercial and military aircraft, these nuts are often employed in the construction of airframes, engine mounts, and landing gear assemblies. Their high strength allows them to withstand the extreme forces experienced during takeoff, landing, and in-flight maneuvers. The weight savings achieved by using titanium nuts instead of steel alternatives can add up significantly across an entire aircraft, contributing to improved fuel efficiency and increased payload capacity.
Space exploration vehicles and satellites also benefit greatly from our product. In the harsh environment of space, where materials are subjected to extreme temperature fluctuations and radiation, titanium's durability and resistance to corrosion are invaluable. These nuts are used in satellite structures, solar panel mounts, and various other components where reliability is paramount.
The use of M8 titanium nuts in aerospace applications goes beyond their mechanical properties. Their resistance to fatigue and crack propagation is crucial in an industry where safety is the top priority. Regular inspections and maintenance procedures in the aerospace sector often involve the removal and replacement of fasteners, and titanium nuts' resistance to galling and seizing makes these operations more manageable and reduces the risk of damage to expensive components.
Automotive
In the automotive industry, M8 titanium nuts have found a niche in high-performance and racing applications where every ounce of weight reduction can translate into improved speed and handling. Formula 1 racing cars, for instance, use titanium fasteners extensively, including M8 nuts, in their chassis, suspension systems, and engine components.
Beyond the racetrack, luxury and sports car manufacturers are increasingly turning to titanium fasteners to enhance the performance of their vehicles. Our product are used in critical areas such as engine mounts, suspension components, and exhaust systems. The weight reduction achieved by using titanium nuts contributes to improved acceleration, better fuel efficiency, and enhanced overall performance.
The automotive industry's push towards electric vehicles (EVs) has also created new opportunities for M8 titanium nuts. In EVs, weight reduction is crucial for extending range and improving efficiency. Titanium nuts are used in battery pack assemblies, motor mounts, and chassis components, helping to offset the weight of heavy battery systems.
Another advantage in automotive applications is their excellent resistance to heat and corrosion. This makes them particularly suitable for use in engine compartments and exhaust systems where temperatures can reach extreme levels. Their corrosion resistance also contributes to the longevity of vehicle components, especially in regions where road salt and other corrosive substances are common.
Marine
The marine industry presents one of the most challenging environments for metal components, with constant exposure to saltwater, humidity, and varying temperatures. M8 titanium nuts excel in these conditions due to their exceptional corrosion resistance, making them a preferred choice for various marine applications.
In boat construction, M8 titanium nuts are used in hull fittings, deck hardware, and engine mounts. Their corrosion resistance ensures that these critical connection points remain secure and easy to maintain over time. This is particularly important in areas that are difficult to access for regular inspection and maintenance.
High-performance sailboats and racing yachts benefit from the lightweight properties of titanium nuts. In these applications, weight reduction is crucial for improving speed and maneuverability. these nuts are often used in rigging components, keel attachments, and other structural elements where high strength and low weight are essential.
The offshore oil and gas industry also utilizes it in various subsea applications. In deep-sea environments, where maintenance and replacement are extremely challenging and costly, the durability and corrosion resistance of titanium fasteners provide significant advantages.
Beyond their functional benefits, M8 titanium nuts in marine applications offer aesthetic advantages. Unlike steel or stainless steel fasteners that may corrode or discolor over time, titanium nuts maintain their appearance, contributing to the overall look and value of high-end marine vessels.
Medical
The medical industry is another significant user of M8 titanium nuts, leveraging titanium's unique properties of biocompatibility and resistance to bodily fluids. These characteristics make titanium fasteners ideal for use in surgical instruments, medical devices, and implants.
In orthopedic and dental implants, it play a crucial role in securing artificial joints, dental prosthetics, and bone plates. The biocompatibility of titanium means that these fasteners can remain in the body for extended periods without causing adverse reactions or being rejected by the immune system. The strength of titanium nuts ensures that implants remain securely in place, even under the stresses of daily movement and activity.
Surgical instruments often incorporate M8 titanium nuts in their construction. The corrosion resistance of titanium is particularly valuable in this context, as it allows instruments to withstand repeated sterilization processes without degradation. The lightweight nature of titanium also contributes to reducing surgeon fatigue during long procedures.
Medical imaging equipment, such as MRI machines, benefit from the non-magnetic properties of titanium. these nuts can be used in these machines without interfering with the magnetic fields essential for imaging. This property also makes titanium fasteners suitable for use in other sensitive medical equipment where magnetic interference could be problematic.
The use of our product extends to external medical devices as well, such as prosthetic limbs and exoskeletons. In these applications, the high strength-to-weight ratio of titanium contributes to creating devices that are both robust and comfortable for patients to use.
M8 Titanium Nuts For Sale
For industries and applications requiring high-quality M8 titanium nuts, Wisdom Titanium company offers a comprehensive range of options. Their M8 titanium nuts, with a thread specification of M8*1.25, are designed to meet the exacting standards of aerospace, automotive, marine, and medical industries.
These titanium nuts are produced under strict quality control measures to ensure consistency and reliability. They undergo rigorous testing to verify their mechanical properties, dimensional accuracy, and surface finish. This attention to detail makes Wisdom Titanium's products suitable for even the most demanding applications in industries where failure is not an option.
Conclusion
To explore Wisdom Titanium's range of M8 titanium nuts or to discuss custom titanium fastener solutions, interested parties are encouraged to contact their sales team at sales@wisdomtitanium.com. Their specialists can offer detailed product information, quotations, and assist with any technical inquiries to ensure customers find the ideal titanium fastening solution for their specific needs.
References
1. Aerospace Materials and Applications. (2018). B. N. Agarwal (Ed.). American Institute of Aeronautics and Astronautics.
2. Titanium in Medical and Dental Applications. (2018). F. H. Froes & M. Qian (Eds.). Woodhead Publishing.
3. Titanium Alloys in Automotive Applications. (2019). Journal of Materials Engineering and Performance, 28(5).
4. Marine Corrosion of Stainless Steels. (2020). C. Carcea & E. Ungureanu. IntechOpen.