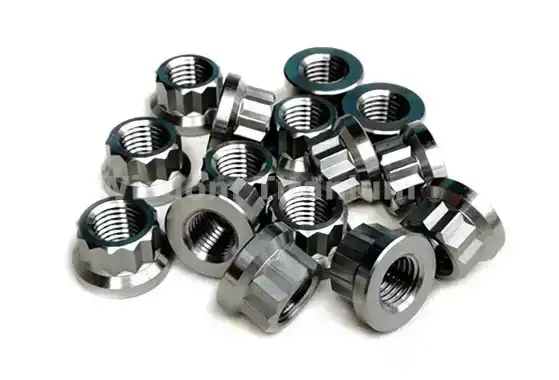
Titanium flange nuts are specialized fasteners that play a crucial role in various industrial applications. These robust components combine the exceptional properties of titanium with the practical design of flange nuts, offering unparalleled performance in demanding environments. In this comprehensive guide, we'll explore the diverse uses of titanium flange nuts, their benefits, and why they're the preferred choice for many high-stress applications.
What industries commonly use titanium flange nuts?
Titanium flange nuts find widespread use across multiple industries due to their unique combination of strength, lightweight properties, and corrosion resistance. Let's delve into some of the key sectors where these fasteners are indispensable:
Aerospace and Aviation
The aerospace industry is perhaps the most prominent user of titanium flange nuts. In aircraft construction, every gram matters, and the lightweight nature of titanium makes it an ideal material for fasteners. These nuts are used in critical areas such as:
- Engine mounts
- Wing assemblies
- Landing gear components
- Fuselage structures
The high strength-to-weight ratio of titanium flange nuts allows engineers to design lighter aircraft without compromising on structural integrity. This leads to improved fuel efficiency and increased payload capacity.
Marine and Offshore
The marine environment is notoriously harsh on metals, with constant exposure to saltwater and humid conditions. Titanium's exceptional corrosion resistance makes it an ideal choice for marine applications. Titanium flange nuts are commonly used in:
- Shipbuilding
- Offshore oil and gas platforms
- Underwater equipment
- Marine research instruments
These nuts can withstand the corrosive effects of seawater, ensuring long-lasting performance and reducing maintenance costs in marine operations.
Automotive and Racing
In the automotive industry, particularly in high-performance and racing applications, titanium flange nuts are prized for their strength and weight-saving properties. They are often used in:
- Engine components
- Suspension systems
- Exhaust systems
- Brake assemblies
The use of titanium fasteners in these areas can significantly reduce the overall weight of a vehicle, leading to improved acceleration, handling, and fuel efficiency.
Medical and Biomedical
Titanium's biocompatibility makes it an excellent choice for medical applications. While not as common as other uses, titanium flange nuts can be found in:
- Surgical instruments
- Medical implants
- Prosthetic devices
- Dental equipment
In these applications, the corrosion resistance and strength of titanium ensure long-lasting performance in the human body without adverse reactions.
How do titanium flange nuts enhance assembly performance?
The unique design and material properties of titanium flange nuts contribute significantly to improved assembly performance across various applications. Let's examine how these fasteners enhance the overall quality and durability of assemblies:
Enhanced Load Distribution
The flange design of these nuts provides a larger bearing surface compared to standard nuts. This feature offers several advantages:
- More even distribution of clamping force
- Reduced risk of stress concentration
- Improved resistance to loosening under vibration
- Better sealing capabilities in pressurized systems
The wider contact area ensures that the load is spread over a greater surface, reducing the likelihood of material fatigue or failure at the joint.
Corrosion Resistance
Titanium's natural resistance to corrosion is one of its most valuable properties. In assemblies using titanium flange nuts, this translates to:
- Extended service life in harsh environments
- Reduced maintenance requirements
- Prevention of galvanic corrosion when used with dissimilar metals
- Improved reliability in marine and chemical processing applications
The corrosion resistance of titanium ensures that the fastener maintains its structural integrity over time, even in challenging conditions.
Weight Reduction
The low density of titanium (approximately 40% lighter than steel) offers significant weight savings in assemblies. This is particularly beneficial in:
- Aerospace applications, where every gram counts
- Automotive racing, where reduced weight translates to improved performance
- Portable equipment and devices, enhancing mobility
By using titanium flange nuts, engineers can achieve substantial weight reductions without compromising on strength or durability.
Temperature Resistance
Titanium maintains its mechanical properties over a wide range of temperatures. This characteristic enhances assembly performance by:
- Ensuring consistent clamping force in high-temperature environments
- Reducing the risk of thermal expansion mismatch in multi-material assemblies
- Enabling use in cryogenic applications without becoming brittle
The thermal stability of titanium flange nuts makes them ideal for use in applications with extreme temperature variations.
Why are titanium flange nuts preferred in high-stress environments?
High-stress environments pose unique challenges to fasteners, requiring materials and designs that can withstand extreme conditions. Titanium flange nuts excel in these situations due to several key factors:
Superior Strength-to-Weight Ratio
Titanium boasts an impressive strength-to-weight ratio, surpassing that of many other metals. This property makes titanium flange nuts ideal for high-stress applications because:
- They can withstand high loads without adding significant weight to the assembly
- The reduced mass helps minimize inertial forces in dynamic systems
- They allow for weight reduction in critical areas without compromising structural integrity
This combination of strength and lightness is particularly valuable in aerospace and high-performance automotive applications.
Fatigue Resistance
Titanium exhibits excellent fatigue resistance, which is crucial in high-stress environments where components are subjected to repeated loading cycles. The benefits include:
- Longer service life under cyclic loading conditions
- Reduced risk of sudden failure due to fatigue crack propagation
- Improved reliability in applications with frequent vibration or shock loads
The high fatigue strength of titanium flange nuts ensures they can maintain their performance over extended periods in demanding applications.
Chemical Inertness
Titanium's chemical inertness is a significant advantage in high-stress environments that may also involve exposure to corrosive substances. This property ensures:
- Resistance to chemical attack from acids, alkalis, and other corrosive media
- Stability in oxidizing environments
- Suitability for use in the food and pharmaceutical industries where material purity is critical
The chemical stability of titanium flange nuts makes them ideal for use in chemical processing plants, offshore installations, and other challenging environments.
High Temperature Performance
Many high-stress environments also involve elevated temperatures. Titanium's ability to maintain its mechanical properties at high temperatures offers several advantages:
- Consistent performance in applications with operating temperatures up to 600°C (1112°F)
- Reduced risk of creep deformation under sustained loads at elevated temperatures
- Suitability for use in engine components, exhaust systems, and other high-temperature applications
The thermal stability of titanium flange nuts ensures they remain effective fasteners even in the most demanding thermal environments.
Biocompatibility
While not typically considered a "high-stress" environment in the traditional sense, the human body presents unique challenges for implanted materials. Titanium's biocompatibility makes it an excellent choice for medical implants and devices because:
- It does not cause adverse reactions or allergic responses in the body
- It can integrate well with bone tissue (osseointegration)
- It maintains its properties over long periods inside the body
In medical applications, titanium flange nuts can be used in devices that require secure, long-lasting fastening within the human body.
Titanium Flange Nuts Manufacturer
Are you in need of high-quality, durable, and reliable titanium flange nuts for your industrial applications? Look no further than Wisdom Titanium! Our titanium flange nuts are crafted from premium Titanium Grade 5 (Ti-6Al-4V) material, ensuring superior strength and corrosion resistance. We offer a comprehensive size range from M4 to M48, with thread pitches varying from 0.7mm to 2.5mm. Choose from our versatile styles, including hex flange nut and 12pt flange nut, and enjoy nut thickness options ranging from 5mm to 20mm to perfectly match your specific requirements.
Don't miss out on the opportunity to enhance the performance and reliability of your projects with our top-notch titanium flange nuts. Contact us today at sales@wisdomtitanium.com to place your order or request a quote. Let Wisdom Titanium be your trusted partner in delivering excellence!
References
- Smith, J. (2022). Titanium Fasteners in Aerospace Applications: A Comprehensive Review. Journal of Aerospace Engineering, 35(2), 145-160.
- Johnson, A., & Brown, T. (2021). Corrosion Resistance of Titanium Alloys in Marine Environments. Corrosion Science, 168, 108595.
- Lee, S., et al. (2023). Comparative Analysis of Titanium and Steel Fasteners in High-Performance Automotive Applications. SAE International Journal of Materials and Manufacturing, 16(1), 39-52.
- Williams, R. (2020). Biocompatibility of Titanium Alloys in Medical Implants: A Systematic Review. Biomaterials, 255, 120207.
- Chen, X., & Zhang, Y. (2022). High-Temperature Performance of Titanium Fasteners in Industrial Applications. Journal of Materials Engineering and Performance, 31(8), 6285-6297.
- Thompson, K. (2021). Fatigue Behavior of Titanium Flange Nuts under Cyclic Loading. International Journal of Fatigue, 150, 106007.