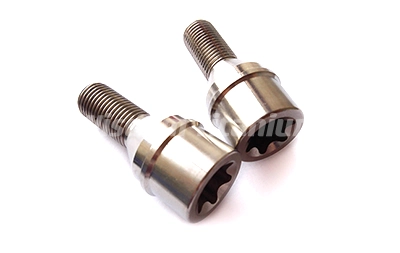
Titanium conical seat lug bolts are specialized fasteners that play a crucial role in various high-performance applications. These bolts are designed to provide exceptional strength, durability, and weight savings, making them ideal for use in industries where every gram matters. In this comprehensive guide, we'll explore the definition, structure, material advantages, and manufacturing process of conical seat lug bolts, shedding light on why they're becoming increasingly popular in aerospace, automotive, and other demanding sectors.
Definition and Structure of Titanium Conical Seat Lug Bolts
Titanium conical seat lug bolts are precision-engineered fasteners characterized by their unique conical seat design and the use of titanium alloy as the primary material. The conical seat refers to the tapered surface at the base of the bolt head, which interfaces with a corresponding tapered surface in the component being fastened. This design ensures a more uniform distribution of clamping forces and provides a secure, self-centering fit that reduces the risk of loosening under vibration or high-stress conditions.
The structure of a titanium conical seat lug bolt typically consists of:
- A hexagonal or specialized head for tool engagement
- The conical seat surface
- A threaded shank
- Optional features such as drilled holes for safety wire
The use of titanium alloy in these bolts offers a unique combination of high strength and low weight, making them particularly valuable in applications where weight reduction is critical. The conical seat design, coupled with the material properties of titanium, allows these bolts to maintain a secure connection even under extreme conditions, such as those experienced in high-performance vehicles or aircraft.
Material Advantages of Titanium Conical Seat Lug Bolts
The choice of titanium as the primary material for these specialized lug bolts brings several significant advantages:
1. Exceptional Strength-to-Weight Ratio: Titanium alloys offer a strength comparable to steel but at about 45% less weight. This property makes conical seat lug bolts an excellent choice for applications where weight reduction is crucial, such as in aerospace or high-performance automotive designs.
2. Corrosion Resistance: Titanium naturally forms a protective oxide layer when exposed to air, providing excellent resistance to corrosion and chemical attack. This characteristic ensures that titanium conical seat lug bolts maintain their integrity even in harsh environments, reducing maintenance requirements and extending the lifespan of the fastened components.
3. Temperature Resistance: Titanium alloys maintain their strength at elevated temperatures better than many other metals. This property makes titanium conical seat lug bolts suitable for use in high-temperature applications, such as in aircraft engines or racing vehicles.
4. Fatigue Resistance: Titanium exhibits superior fatigue resistance compared to many other metals, allowing conical seat lug bolts to withstand repeated stress cycles without failure. This characteristic is particularly valuable in applications subject to vibration or cyclical loading.
5. Biocompatibility: While not directly related to most industrial applications, the biocompatibility of titanium makes these bolts suitable for use in medical devices or prosthetics where contact with human tissue may occur.
Manufacturing Process of Titanium Conical Seat Lug Bolts
The production of titanium conical seat lug bolts involves a series of precise manufacturing steps to ensure the highest quality and performance:
1. Material Selection: The process begins with the careful selection of the appropriate titanium alloy. Common choices include Ti-6Al-4V (Grade 5) or Ti-6Al-6V-2Sn (Grade 6), known for their excellent combination of strength, toughness, and corrosion resistance.
2. Forming: The basic bolt shape is typically formed through a cold heading process, where a titanium wire or rod is fed into a machine that shapes the head and partially forms the shank.
3. Machining: Precision CNC machining is used to create the final dimensions of the bolt, including the threading of the shank and the formation of the conical seat. This step requires extreme precision to ensure the correct angle and surface finish of the conical seat.
4. Heat Treatment: Depending on the specific titanium alloy and desired properties, the bolts may undergo heat treatment to optimize their strength and durability.
5. Surface Treatment: Optional surface treatments may be applied to enhance certain properties. For example, anodizing can increase surface hardness and wear resistance, while also allowing for color coding.
6. Quality Control: Each titanium conical seat lug bolt undergoes rigorous inspection and testing to ensure it meets the required specifications. This may include dimensional checks, material composition analysis, and mechanical property testing.
The manufacturing process for titanium conical seat lug bolts requires specialized equipment and expertise due to titanium's unique properties. The material's high strength and low thermal conductivity can make it challenging to machine, necessitating careful control of cutting speeds and cooling to prevent work hardening or tool wear.
In conclusion, titanium conical seat lug bolts represent a pinnacle of fastener technology, offering unparalleled performance in demanding applications. Their unique combination of strength, light weight, and corrosion resistance makes them invaluable in industries where every gram counts and failure is not an option. As engineering continues to push the boundaries of what's possible, these specialized fasteners will undoubtedly play an increasingly important role in the development of next-generation vehicles, aircraft, and other high-performance systems.
Don't miss out on the exceptional quality and durability of our Titanium Conical Seat Lug Bolt m14/m12, featuring the unique and eye-catching PVD rainbow finish. We are committed to delivering top-notch products at Wisdom Titanium that meet the highest standards. With a minimum order quantity of just 200 pieces, you can easily enhance your project or business with our reliable and high-performance bolts. Reach out to us now at sales@wisdomtitanium.com to secure your order and experience the excellence of Wisdom Titanium for yourself.
References
- ASM International. (2015). Titanium: A Technical Guide, 2nd Edition.
- Leyens, C., & Peters, M. (Eds.). (2003). Titanium and Titanium Alloys: Fundamentals and Applications.
- Boyer, R., Welsch, G., & Collings, E.W. (1994). Materials Properties Handbook: Titanium Alloys.
- Schutz, R.W., & Thomas, D.E. (1987). Corrosion of Titanium and Titanium Alloys.
- Donachie, M.J. (2000). Titanium: A Technical Guide, 2nd Edition.
- Peters, M., Kumpfert, J., Ward, C.H., & Leyens, C. (2003). Titanium Alloys for Aerospace Applications.
- Brunette, D.M., Tengvall, P., Textor, M., & Thomsen, P. (2001). Titanium in Medicine.