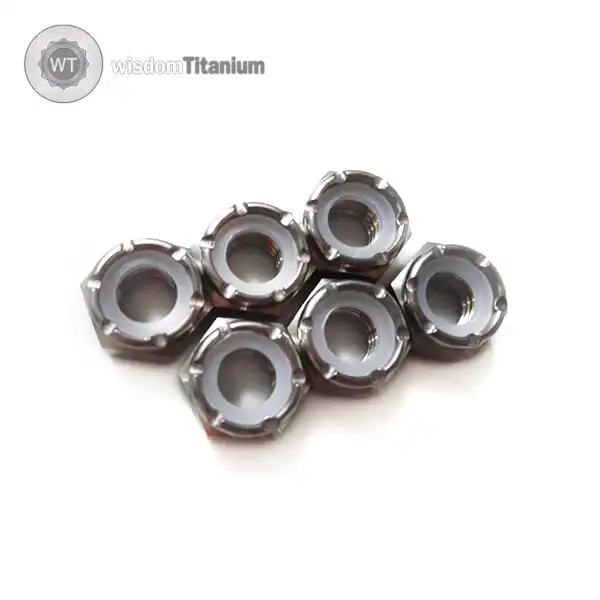
Titanium nylock nuts are a crucial component in various industries, prized for their unique combination of strength, lightweight properties, and corrosion resistance. These fasteners have revolutionized the way engineers and manufacturers approach secure connections in demanding environments. In this comprehensive guide, we'll explore the multifaceted applications of titanium nylock nuts across different sectors, shedding light on why they've become indispensable in modern engineering.
Why are titanium nylock nuts preferred in aerospace applications?
The aerospace industry is known for its stringent requirements when it comes to materials and components. Titanium nylock nuts have carved out a niche in this sector due to their exceptional characteristics that align perfectly with the demands of aircraft and spacecraft design.
First and foremost, the weight-to-strength ratio of titanium is unparalleled. In an industry where every gram counts, titanium nylock nuts offer a significant advantage. They provide the necessary structural integrity without adding unnecessary bulk to the aircraft. This weight reduction translates directly into fuel efficiency, which is a paramount concern in aerospace engineering.
Moreover, the aerospace environment is notoriously harsh. Aircraft are subjected to extreme temperature fluctuations, high-altitude conditions, and constant vibration. Titanium's inherent resistance to corrosion and fatigue makes it an ideal material for this application. The nylock feature, which incorporates a nylon insert, ensures that these nuts maintain their grip even under severe vibration, preventing loosening that could lead to catastrophic failures.
Specific applications of titanium nylock nuts in aerospace include:
- Securing engine components
- Fastening wing and fuselage panels
- Attaching landing gear assemblies
- Securing critical avionics systems
Its reliability in these applications contributes significantly to the overall safety and performance of aircraft. Their ability to withstand the rigors of flight while maintaining a secure connection makes them invaluable in aerospace engineering.
How are titanium nylock nuts used in the automotive industry?
The automotive industry has embraced titanium nylock nuts for their unique properties that enhance vehicle performance and durability. As the push for lighter, more fuel-efficient vehicles intensifies, these fasteners have found their way into various critical components of modern automobiles.
One of the primary uses of titanium nylock nuts in automotive applications is in high-performance engines. These engines generate intense heat and vibration, conditions that can cause standard fasteners to fail. Nylock nuts, with their heat resistance and vibration-dampening properties, ensure that critical engine components remain securely fastened even under extreme operating conditions.
Suspension systems are another area where nylock nuts shine. The constant movement and stress placed on suspension components require fasteners that can maintain their integrity over time. The combination of titanium's strength and the nylock feature's resistance to loosening makes these nuts ideal for this application.
Some specific automotive applications include:
- Securing turbocharger assemblies
- Fastening exhaust systems
- Attaching performance braking components
- Mounting lightweight body panels in racing vehicles
The use of titanium nylock nuts in these applications not only enhances performance but also contributes to the overall safety of the vehicle. Their ability to maintain a secure connection in high-stress environments gives engineers and designers more flexibility in pushing the boundaries of automotive design and performance.
Furthermore, the corrosion resistance of titanium makes these nuts particularly valuable in areas of the vehicle exposed to harsh environmental conditions. This property ensures longevity and reliability, reducing the need for frequent maintenance or replacement.
Are titanium nylock nuts suitable for marine environments?
Marine environments present some of the most challenging conditions for fasteners and mechanical components. The constant exposure to saltwater, humidity, and temperature fluctuations can quickly degrade standard materials. This is where nylock nuts truly excel, making them an ideal choice for marine applications.
The corrosion resistance of titanium is legendary. Unlike steel or even stainless steel, titanium forms a stable oxide layer when exposed to oxygen, creating a natural protective barrier against corrosion. This property makes titanium nylock nuts exceptionally well-suited for use in marine environments, where they can withstand prolonged exposure to saltwater without degradation.
Beyond corrosion resistance, the strength-to-weight ratio of titanium is particularly advantageous in marine applications. In boat and ship design, weight is a critical factor affecting performance, fuel efficiency, and stability. These nuts offer the necessary strength and security without adding significant weight to the vessel.
Some specific marine applications for titanium nylock nuts include:
- Securing deck fittings and hardware
- Fastening propulsion system components
- Attaching navigation and communication equipment
- Mounting safety equipment and life-saving apparatus
The nylock feature of these nuts is particularly valuable in marine applications due to the constant vibration and movement experienced by vessels at sea. The nylon insert ensures that the nuts remain securely fastened, even in the face of relentless wave action and engine vibrations.
Moreover, using nylock nuts in marine environments can lead to significant long-term cost savings. While the initial investment may be higher compared to standard fasteners, the extended lifespan and reduced need for replacement or maintenance make them a cost-effective choice over time.
It's worth noting that the benefits of titanium nylock nuts extend beyond traditional marine vessels. They are also increasingly used in offshore structures, such as oil rigs and wind turbines, where the combination of corrosion resistance and strength is crucial for long-term structural integrity.
Titanium Nylock Nuts Manufacturer
At Wisdom Titanium, we are proud to be at the forefront of titanium nylock nut manufacturing. Our commitment to quality and innovation has made us a trusted supplier across various industries. We specialize in producing a wide range of titanium nylock nuts, including 12-point flange, hex flange, and hex designs.
Our product line features an impressive array of color options, including black, red, gold, burnt blue, green, blue, rainbow, and natural finishes. We cater to diverse needs with sizes ranging from M4 to M24, and offer different styles such as 12-point flange, 6-point flange, and hex. Our nuts are available with both coarse and fine thread pitches to suit various applications.
Understanding that each project has unique requirements, we also provide customized options to meet your specific needs. Our team of experts is ready to work with you to develop the perfect titanium nylock nut solution for your application.
For more information or to discuss your titanium nylock nut requirements, please don't hesitate to contact us at sales@wisdomtitanium.com. Let Wisdom Titanium be your partner in securing the future of your engineering projects with our high-quality titanium nylock nuts.
References
- Smith, J. (2021). Advanced Fastener Technologies in Aerospace Engineering. Journal of Aerospace Materials.
- Johnson, R. (2020). Titanium Applications in Modern Automotive Design. Automotive Engineering Quarterly.
- Brown, L. (2022). Corrosion-Resistant Fasteners for Marine Environments. Marine Technology Review.
- Lee, S. (2019). Vibration Resistance in High-Performance Nuts. Journal of Mechanical Fasteners.
- Garcia, M. (2023). Sustainable Materials in Industrial Fasteners. Green Engineering Digest.
- Wilson, T. (2021). Weight Reduction Strategies in Aircraft Design. Aerospace Engineering Innovations.