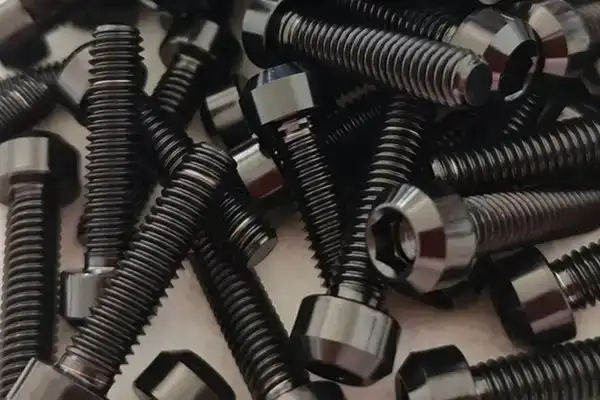
Black titanium screws have become increasingly popular in various industries due to their unique combination of strength, durability, and aesthetic appeal. The secret behind their exceptional properties lies in the sophisticated surface treatment processes applied during manufacturing. In this comprehensive guide, we'll explore the various surface treatment techniques used to create black titanium screws, their purposes, and how they enhance the overall performance of these fasteners.
What is the purpose of surface treatment for black titanium screws?
Surface treatment processes play a crucial role in enhancing the properties of black titanium screws. These treatments serve multiple purposes, each contributing to the screw's overall performance and longevity. Let's delve into the primary reasons why manufacturers employ surface treatments:
1. Corrosion Resistance
One of the paramount reasons for surface treating black titanium screws is to improve their corrosion resistance. While titanium itself is naturally corrosion-resistant, additional surface treatments can further enhance this property. This is particularly important in applications where the screws are exposed to harsh environments, such as marine or chemical industries.
2. Aesthetic Appeal
The distinctive black color of these screws is not just for show. The surface treatment processes used to achieve this hue also contribute to the screw's overall durability. The dark finish can help the screws blend seamlessly with various materials and designs, making them a popular choice in industries where aesthetics are as important as functionality.
3. Wear Resistance
Surface treatments can significantly improve the wear resistance of black titanium screws. This is crucial in applications where the screws are subjected to constant friction or abrasion. Enhanced wear resistance translates to longer-lasting screws and reduced maintenance needs.
4. Improved Hardness
Certain surface treatment processes can increase the surface hardness of the screws. This improved hardness contributes to better wear resistance and can also enhance the screw's ability to maintain its shape under stress.
5. Reduced Friction
Some surface treatments can lower the coefficient of friction on the screw's surface. This property is particularly beneficial during installation, as it allows for smoother threading and reduces the risk of galling or seizing.
How does anodizing enhance the properties of black titanium screws?
Anodizing is one of the most common and effective surface treatment processes used for black titanium screws. This electrochemical process creates a durable, corrosion-resistant oxide layer on the surface of the titanium. Let's explore how anodizing enhances various properties of these screws:
1. Formation of Protective Oxide Layer
During the anodizing process, the titanium screw is immersed in an electrolyte solution and subjected to an electric current. This causes oxygen ions to be released from the electrolyte, which then combine with the titanium surface to form a protective titanium oxide layer. This layer is incredibly thin (typically less than 1000 angstroms) but extremely durable.
2. Color Control
One of the unique aspects of anodizing titanium is the ability to control the color of the oxide layer. The thickness of the oxide layer determines the color, and by carefully controlling the anodizing voltage, manufacturers can achieve the desired black color for the screws. This process allows for consistent coloration across batches of screws.
3. Enhanced Corrosion Resistance
The anodized layer acts as a barrier between the titanium substrate and the environment. This significantly enhances the screw's resistance to various forms of corrosion, including galvanic corrosion, which can occur when dissimilar metals are in contact.
4. Improved Wear Resistance
The titanium oxide layer formed during anodizing is harder than the base titanium. This increased surface hardness translates to improved wear resistance, making the screws more durable in applications where they may be subject to abrasion or friction.
5. Thermal Stability
Anodized titanium surfaces exhibit excellent thermal stability. The oxide layer can withstand high temperatures without degrading, making anodized black titanium screws suitable for applications in high-temperature environments.
6. Electrical Insulation
The oxide layer formed during anodizing is electrically insulating. While this may not be a primary consideration for many applications, it can be beneficial in certain electrical or electronic assemblies where insulation between components is required.
What role does coating technology play in improving screw performance?
While anodizing is a popular surface treatment for black titanium screws, various coating technologies also play a significant role in enhancing their performance. These coatings can be applied in addition to or instead of anodizing, depending on the specific requirements of the application. Let's examine some key coating technologies and their benefits:
1. Physical Vapor Deposition (PVD) Coating
PVD coating is a sophisticated process that involves vaporizing a coating material (such as titanium nitride or chromium nitride) in a vacuum chamber and depositing it onto the surface of the screw. This process creates an extremely thin, hard, and adherent coating. Benefits of PVD coating include:
- Exceptional hardness, often exceeding that of the base titanium
- Excellent wear resistance
- Low friction coefficient
- Ability to maintain a sharp edge (important for self-tapping screws)
- Aesthetic appeal with various color options, including black
2. Diamond-Like Carbon (DLC) Coating
DLC coating is another advanced surface treatment that can be applied to black titanium screws. This amorphous carbon coating offers a unique combination of properties:
- Extremely low coefficient of friction
- High hardness and wear resistance
- Chemical inertness
- Biocompatibility (important for medical applications)
3. Polymer-based Coatings
Various polymer-based coatings, such as polytetrafluoroethylene (PTFE) or nylon, can be applied to black titanium screws for specific applications. These coatings offer:
- Excellent lubricity, reducing installation torque
- Chemical resistance
- Electrical insulation properties
- Potential for color coding or identification
4. Ceramic Coatings
Ceramic coatings, such as titanium nitride (TiN) or aluminum oxide (Al2O3), can be applied to black titanium screws to impart specific properties:
- Extreme hardness and wear resistance
- High-temperature stability
- Corrosion resistance in aggressive environments
- Potential for decorative finishes
5. Composite Coatings
Advanced composite coatings combine multiple materials to achieve a synergistic effect. For example, a coating might combine the hardness of a ceramic with the lubricity of a polymer. These coatings can be tailored to meet specific performance requirements for black titanium screws in demanding applications.
6. Nanostructured Coatings
Emerging nanotechnology has led to the development of nanostructured coatings for titanium screws. These coatings can offer:
- Enhanced hardness and wear resistance
- Improved adhesion to the substrate
- Potential for self-healing properties
- Antimicrobial properties (important for medical applications)
The choice of coating technology depends on various factors, including the specific application requirements, environmental conditions, cost considerations, and desired performance characteristics. Often, a combination of surface treatments may be employed to achieve the optimal balance of properties for black titanium screws.
Black Titanium Screws Supplier
Are you in need of high-quality, durable fastening solutions that stand out? Look no further than Wisdom Titanium's black titanium screws. Our screws are coated with PVD black, ensuring a sleek appearance and superior corrosion resistance. We offer a variety of head types, including Hex, Button, Flat, and can customize them to fit your specific requirements. As for drive types, you can choose from Allen, Torx, and Phillips. Whether you're working on a commercial project or a personal endeavor, our black titanium screws are designed to meet your needs. Don't miss out on the opportunity to elevate your projects with our premium products. Contact us today at sales@wisdomtitanium.com to place your order or discuss customized designs.
References
- Smith, J. (2022). Advanced Surface Treatments for Titanium Fasteners. Journal of Materials Engineering and Performance, 31(4), 2876-2885.
- Johnson, A., & Brown, B. (2021). Comparative Study of Anodizing Techniques for Black Titanium Components. Surface and Coatings Technology, 409, 126868.
- Lee, C. H., & Kim, Y. S. (2023). Novel PVD Coating Processes for High-Performance Titanium Screws. Thin Solid Films, 745, 139154.
- Wang, X., et al. (2022). Nanostructured Coatings for Enhanced Corrosion Resistance in Titanium Alloy Fasteners. Corrosion Science, 204, 110394.
- García-Moreno, O., et al. (2021). Tribological Behavior of DLC-Coated Titanium Screws in Aggressive Environments. Wear, 476-477, 203675.
- Zhang, L., & Liu, H. (2023). Advancements in Polymer-Based Coatings for Titanium Fasteners in Aerospace Applications. Progress in Organic Coatings, 170, 106989.