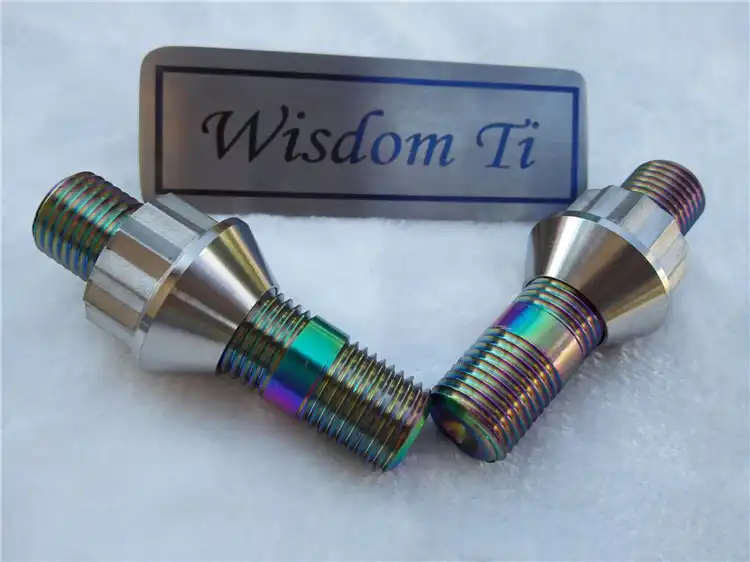
Material strength
When it comes to determining the strongest wheel studs, material composition plays a crucial role. Various materials are used in the manufacturing of the products, each with its own set of properties that contribute to overall strength and durability. Two materials that stand out for their exceptional strength characteristics are chrome moly steel and titanium alloy.
Chrome moly steel, also known as chromium-molybdenum steel or 4140 steel, is a popular choice for high-strength wheel studs. This alloy steel contains chromium and molybdenum, which contribute to its impressive tensile strength and fatigue resistance. Chrome moly steel wheel studs can achieve tensile strengths of up to 200,000 psi (pounds per square inch) when properly heat-treated. This exceptional strength makes them suitable for demanding applications, including racing and high-performance vehicles.
One prominent example of chrome moly steel wheel studs is the NASCAR Speed Studs. These studs are made from heat-treated 200,000 psi chromoly steel, offering superior strength and durability for race cars that experience extreme forces during competition. The high tensile strength of these studs helps prevent failure under the intense stresses of high-speed cornering and rapid acceleration.
Titanium alloy is another material known for its exceptional strength-to-weight ratio. Titanium wheel studs typically offer tensile strengths comparable to or even exceeding those of chrome moly steel studs, while being significantly lighter. The most common titanium alloy used for products is Ti-6Al-4V, which can achieve tensile strengths of up to 170,000 psi. While this is slightly lower than the maximum strength of chrome moly steel, titanium's lower density (about 45% lighter than steel) makes it an attractive option for applications where weight reduction is crucial.
Fatigue resistance is another critical factor in determining the strength of products. Both chrome moly steel and titanium alloys exhibit excellent fatigue resistance, allowing them to withstand repeated stress cycles without failure. Titanium, in particular, has superior fatigue properties compared to most steels, which contributes to its popularity in aerospace and high-performance automotive applications.
Design and manufacturing process
The strength of wheel studs is not solely determined by material composition; the design and manufacturing processes play equally important roles. Heat treatment, precision threading, and forging are key processes that significantly impact the final strength and durability of wheel studs.
Heat treatment is a crucial step in enhancing the mechanical properties of them. For chrome moly steel studs, processes such as quenching and tempering are employed to achieve the desired balance of strength and toughness. The heat treatment process involves heating the studs to a specific temperature, rapidly cooling them (quenching), and then reheating to a lower temperature (tempering). This process alters the microstructure of the steel, resulting in improved strength and durability.
Precision threading is another critical aspect of product manufacturing. The thread profile, pitch, and depth all contribute to the stud's overall strength and its ability to maintain a secure connection with the wheel and hub. Computer Numerical Control (CNC) machining is often used to ensure highly accurate and consistent threading, which is essential for even load distribution and optimal performance.
The forging process can significantly enhance its durability. Forged they are created by shaping heated metal using compressive forces, which aligns the grain structure of the material. This alignment results in improved strength and ductility compared to cast or machined studs. Forged they typically exhibit better fatigue resistance and can withstand higher loads, making them ideal for high-stress applications.
Cold forging is a variation of the forging process that's particularly effective for producing high-strength wheel studs. This method involves shaping the metal at room temperature, which can result in even greater strength improvements due to work hardening of the material. Cold-forged wheel studs often have superior mechanical properties compared to their hot-forged counterparts.
Industry standards and testing
To ensure that the product meet specific performance and safety requirements, they must adhere to industry standards and undergo rigorous testing. The Society of Automotive Engineers (SAE) has established several standards that apply to wheel studs, including SAE J429, which defines mechanical and material requirements for various grades of bolts and studs.
One of the most critical tests for them is the tensile strength test. This test measures the maximum load a stud can withstand before failure. According to SAE J429, Grade 8 bolts and studs (which are commonly used in high-performance applications) must have a minimum tensile strength of 150,000 psi. However, many high-performance them, such as the NASCAR Speed Studs mentioned earlier, significantly exceed this minimum requirement.
Fatigue testing is another crucial aspect of its evaluation. This test involves subjecting the studs to repeated cycles of stress to simulate real-world conditions. The number of cycles a stud can withstand before failure is a key indicator of its durability and suitability for various applications. High-quality products should be able to endure millions of stress cycles without showing signs of fatigue or failure.
Corrosion resistance testing is also important, particularly for them that will be exposed to harsh environmental conditions. Salt spray tests are commonly used to evaluate a stud's ability to resist corrosion. In these tests, studs are exposed to a salt spray environment for a specified period, and then examined for signs of corrosion or degradation.
It's worth noting that while industry standards provide a baseline for performance, many manufacturers of high-performance wheel studs go beyond these minimum requirements. They often conduct additional tests and set higher internal standards to ensure their products meet the demands of the most challenging applications.
Titanium wheel studs for sale
For those interested in upgrading to some of the strongest wheel studs available, they are an excellent option to consider. These high-performance studs offer an impressive combination of strength, light weight, and corrosion resistance, making them ideal for both racing and high-end street applications.
Wisdom Titanium company is one manufacturer that offers a range of titaniumthe product to fit various vehicles and applications. Their product line includes studs with common thread sizes such as M12 x 1.5, M14 x 1.25, and M14 x 1.5. These sizes cover a wide range of vehicles, from compact cars to larger SUVs and trucks.
When selecting titanium about product, it's crucial to choose the correct thread size and length for your specific vehicle. Using studs with incorrect specifications can compromise safety and performance. If you're unsure about the right size for your vehicle, it's advisable to consult with a professional or contact the manufacturer directly.
Wisdom Titanium company invites potential customers to reach out to them at sales@wisdomtitanium.com for more information or assistance in choosing the right titanium the product. Their team can provide guidance on selecting the appropriate studs based on your vehicle specifications and performance requirements.
While titanium wheel studs offer significant advantages in terms of strength and weight reduction, it's important to note that they may not be necessary for every vehicle or driving situation. They are most beneficial for high-performance applications, racing, or for enthusiasts who prioritize weight reduction and durability. As with any significant vehicle modification, it's always recommended to consult with a qualified mechanic or automotive specialist before making changes to critical components like wheel studs.
References
1. Society of Automotive Engineers. Mechanical and Material Requirements for Externally Threaded Fasteners. SAE International.
2. ASM International. ASM Handbook, Volume 1: Properties and Selection: Irons, Steels, and High-Performance Alloys.
3. Budynas, R. G., & Nisbett, J. K. Shigley's Mechanical Engineering Design (9th ed.). McGraw-Hill Education.
4. Donachie, M. J. Titanium: A Technical Guide (2nd ed.). ASM International.
5. Smith, W. F., & Hashemi, J. Foundations of Materials Science and Engineering (4th ed.). McGraw-Hill Education.
6. NASCAR. NASCAR Rule Book.