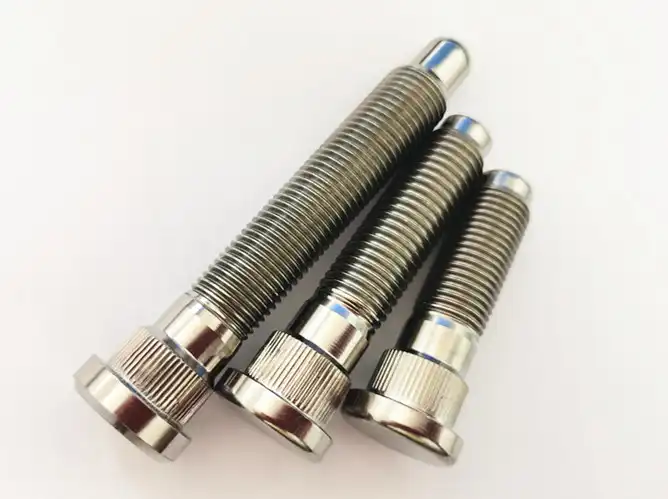
In the ever-evolving automotive industry, lightweighting has become a crucial focus for manufacturers worldwide. The push for lighter vehicles stems from the urgent need to improve fuel economy, enhance performance, and reduce environmental impact. As automakers strive to meet stringent emissions regulations and consumer demands for more efficient vehicles, every component of a car is scrutinized for potential weight reduction.
Among these components, wheel hub bolts play a critical role in the overall performance and safety of a vehicle. These seemingly small parts serve as the vital connection between the wheel hub and the axle, bearing significant responsibility in maintaining the integrity of the wheel assembly. The lightweighting of wheel hub bolts, particularly through the use of titanium alloys, has emerged as a promising avenue for achieving substantial weight savings without compromising structural integrity.
Titanium stud lug bolts, being significantly lighter than their steel counterparts, contribute to reducing the unsprung weight of a vehicle. This reduction in unsprung mass leads to improved handling, better acceleration, and enhanced fuel efficiency. Moreover, the superior strength-to-weight ratio of titanium alloys ensures that these lightweight bolts maintain, and in some cases exceed, the performance characteristics of traditional steel bolts.
Titanium Stud Lug Bolts In Automobiles
The application of titanium alloy wheel hub bolts in automotive lightweighting spans various sectors of the industry, from high-performance racing to luxury consumer vehicles and the aftermarket modification scene.
In the racing field, titanium alloy wheel hub bolts have found widespread adoption, particularly in premier motorsport categories such as Formula 1 and endurance racing series like Le Mans. In these high-stakes environments, where every gram of weight can impact lap times, the use of titanium bolts provides a significant advantage. For instance, in Formula 1, where cars are subject to extreme forces during cornering, acceleration, and braking, titanium wheel hub bolts offer the necessary strength while contributing to the overall weight reduction strategy. This weight saving, though seemingly small, can translate to measurable improvements in acceleration, cornering speed, and fuel consumption over the course of a race.
The benefits observed in racing have not gone unnoticed by manufacturers of high-end civilian vehicles. Luxury and performance car brands have begun incorporating titanium alloy wheel hub bolts into their top-tier models. For example, certain models from manufacturers like Porsche, Ferrari, and McLaren have adopted titanium bolts as part of their lightweighting strategies. This adoption serves a dual purpose: it contributes to the overall performance of the vehicle while also aligning with the premium positioning of these brands. The use of advanced materials like titanium in components as specific as wheel hub bolts underscores the attention to detail and pursuit of performance that these brands are known for.
In the automotive modification market, titanium stud lug bolts have gained popularity among enthusiasts seeking to optimize their vehicles' performance. The aftermarket scene, often at the forefront of adopting racing technologies for street use, has embraced titanium bolts for their weight-saving properties and aesthetic appeal. Many modification enthusiasts view titanium wheel hub bolts as a way to reduce unsprung weight, potentially improving handling and acceleration. Additionally, the distinctive appearance of titanium bolts, often featuring anodized colors, adds a visual element that appeals to those looking to customize their vehicles.
Technical Challenges
Despite the clear advantages of titanium stud lug bolts in automotive lightweighting, several technical challenges need to be addressed for their wider adoption.
Cost remains a significant barrier to the widespread use of titanium alloy wheel hub bolts. Titanium is inherently more expensive than steel due to its rarity and the complex extraction and refining processes required. This higher material cost translates directly to increased component prices, which can be prohibitive for mass-market vehicle applications. Manufacturers and suppliers are continually working to optimize production processes and explore new titanium alloy formulations to reduce costs while maintaining performance benefits. However, balancing the performance gains against the increased cost remains a crucial consideration for automotive designers and engineers.
The processing difficulty associated with titanium alloys presents another significant challenge. Titanium is known for its high strength-to-weight ratio, but this strength also makes it more difficult to machine and form compared to steel. The material's high melting point and reactivity with oxygen at elevated temperatures require specialized manufacturing techniques and equipment. These processing challenges can lead to longer production times and higher manufacturing costs. To address this, research is ongoing into improved machining techniques, such as high-speed cutting and advanced coating technologies for cutting tools, to enhance the efficiency of titanium stud lug bolt processing.
Standardization is another crucial aspect that needs attention for the broader adoption of titanium alloy wheel hub bolts. The automotive industry relies heavily on standardized components to ensure interchangeability and ease of maintenance. While steel wheel hub bolts have well-established standards, the relatively new application of titanium in this area means that industry-wide standards are still evolving. Ensuring that titanium alloy bolts are compatible with existing wheel designs and can be easily integrated into current manufacturing and assembly processes is essential. This standardization process involves collaboration between material scientists, automotive engineers, and industry regulatory bodies to establish guidelines that ensure safety, performance, and interoperability.
Future Development Trend
The future of titanium alloy wheel hub bolts in automotive lightweighting looks promising, with ongoing research and technological advancements paving the way for new possibilities.
The development of new materials is at the forefront of efforts to enhance the performance and reduce the cost of titanium alloy components. Research is underway to create new titanium alloys that offer improved strength, ductility, and machinability while potentially lowering material costs. For instance, beta titanium alloys are being explored for their excellent combination of strength and formability. These new alloys could make titanium wheel hub bolts more accessible to a broader range of vehicle segments, extending the benefits of lightweighting beyond high-end and performance vehicles.
Additive manufacturing, particularly 3D printing technology, is poised to revolutionize the production of titanium stud lug bolts. This technology offers several advantages over traditional manufacturing methods. Firstly, it allows for the creation of complex geometries that can further optimize the strength-to-weight ratio of the bolts. Secondly, 3D printing can significantly reduce material waste, which is particularly beneficial when working with expensive materials like titanium. Moreover, the ability to produce parts on-demand could lead to more efficient inventory management and customization options.
The application of 3D printing in manufacturing titanium wheel hub bolts also opens up possibilities for design optimization. Engineers can use advanced simulation software in conjunction with 3D printing to iterate quickly on designs, testing and refining bolt geometries to achieve the optimal balance of strength, weight, and manufacturability. This rapid prototyping capability could accelerate the development of new, more efficient bolt designs.
Furthermore, the customization potential offered by 3D printing aligns well with the growing trend of vehicle personalization. In the future, we might see options for custom-designed wheel hub bolts tailored to specific vehicle models or even individual customer preferences, all while maintaining the lightweight and high-strength properties of titanium alloys.
Titanium Stud Lug Bolts supplier
For those in the market for titanium stud lug bolts, Wisdom Titanium offers a range of options to meet various automotive needs. Their titanium stud lug bolts are available in thread sizes M12 and M14, catering to different vehicle specifications. Customers can choose from various surface finishes, including polished, anodized, or customized options to match their aesthetic preferences or functional requirements.
The use of titanium in these stud lug bolts aligns with the industry's push towards lightweighting, offering a significant weight reduction compared to traditional steel bolts while maintaining the necessary strength and durability. This makes them particularly suitable for high-performance applications or for enthusiasts looking to optimize their vehicle's weight distribution.
If you're considering titanium stud lug bolts for your automotive project, Wisdom Titanium welcomes inquiries at sales@wisdomtitanium.com. Their team can provide more detailed information about specifications, customization options, and how their products can contribute to your vehicle's performance and lightweighting goals.
References
1. Lutsey, N. (2010). Review of technical literature and trends related to automobile mass-reduction technology. Institute of Transportation Studies, University of California, Davis.
2. Ghassemieh, E. (2011). Materials in automotive application, state of the art and prospects. New trends and developments in automotive industry, 365-394.
3. Jambor, A., & Beyer, M. (1997). New cars—new materials. Materials & design, 18(4-6), 203-209.
4. Elahinia, M. H., Hashemi, M., Tabesh, M., & Bhaduri, S. B. (2012). Manufacturing and processing of NiTi implants: A review. Progress in materials science, 57(5), 911-946.
5. Faller, K., & Froes, F. H. (2001). The use of titanium in family automobiles: Current trends. JOM, 53(4), 27-28.