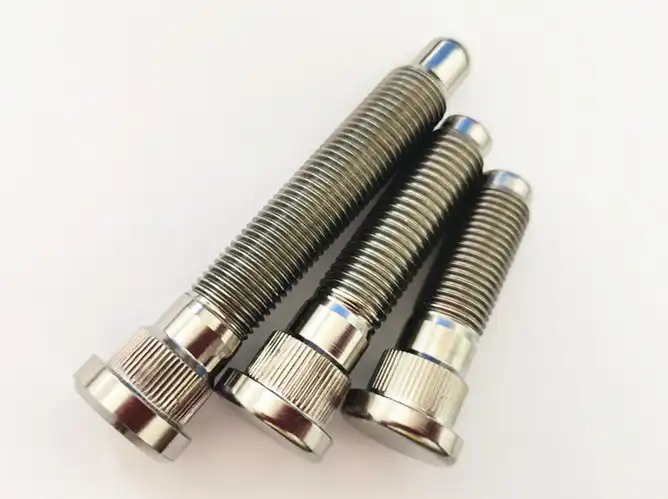
Titanium stud lug bolts are crucial components in various industries, including automotive, aerospace, and construction. These high-strength fasteners are prized for their excellent strength-to-weight ratio, corrosion resistance, and durability. Understanding the manufacturing processes involved in producing it is essential for engineers, manufacturers, and end-users alike. This article will delve into the intricate steps involved in crafting these precision components, from raw material selection to the final product.
Prepare The Blank
The manufacturing process for titanium stud lug bolts begins with the careful selection of raw materials. Titanium alloys, such as Ti-6Al-4V (Grade 5) or Ti-6Al-2Sn-4Zr-2Mo (Grade 6), are commonly used due to their superior mechanical properties. The choice of alloy depends on the specific requirements of the application, such as strength, temperature resistance, and weight considerations.
The raw material comes in the form of titanium rods or bars with various diameters. The selection of the appropriate rod diameter is crucial as it directly influences the final dimensions of the stud lug bolt. Manufacturers typically use computer-aided design (CAD) software to determine the optimal starting diameter based on the desired specifications of the finished product. This step ensures minimal material waste and efficient use of resources.
Once the appropriate raw material is selected, it is cut into blanks of the required length. This process often involves precision cutting equipment such as CNC (Computer Numerical Control) saws or wire EDM (Electrical Discharge Machining) machines. The cutting process must be carefully controlled to ensure consistent blank lengths, which is crucial for maintaining quality and uniformity in the final product.
Upsetting
Upsetting is a critical step in the manufacturing process of it. This forging technique involves heating the titanium blank to temperatures between 600-700°C (1112-1292°F). At these elevated temperatures, titanium becomes more malleable, enabling easier shaping without risking material failure.
The heated blank is then placed into a specially designed mold or die. Hydraulic or mechanical presses apply force to the blank, deforming it to fill the mold cavity. This forms the bolt’s basic shape, including the rod, head, and radius (R) angle under the head.
Often, a single upsetting operation is insufficient to achieve the desired shape and properties. Multiple upsetting steps may be needed, each with a different mold configuration. This sequential process enables complex geometries and optimizes material flow, improving strength and grain structure in the final product.
Upsetting distributes material evenly, ensures proper head formation, creates a necessary fillet radius, and enhances the titanium stud lug bolts's grain structure. Precise temperature control prevents overheating and maintains quality, often managed by advanced forging equipment with integrated monitoring systems.
Cleaning
After the upsetting process, titanium stud lug bolts need thorough cleaning to eliminate surface contaminants, scale, or lubricants accumulated during forging. This cleaning is crucial to ensure proper surface quality for subsequent steps, remove potential contamination affecting performance or appearance, and prepare the surface for heat treatment and further machining.
The cleaning process typically involves immersing the bolts in a heated degreasing solution, usually between 80-100°C (176-212°F). This elevated temperature effectively breaks down and removes oils, greases, and other contaminants.
Common degreasing agents include alkaline cleaners, which remove organic contaminants without damaging the titanium. The cleaning process often includes:
1. Initial rinse to remove loose debris;
2. Immersion in the heated degreasing solution;
3. Ultrasonic cleaning for stubborn contaminants;
4. Final rinse with clean water;
5. Drying with compressed air or in a controlled environment.
Titanium’s high reactivity with oxygen at elevated temperatures necessitates minimizing exposure to air. Some manufacturers clean in an inert atmosphere or promptly transfer bolts to the next step to avoid oxidation.
Heat Treatment
Heat treatment is a crucial step in manufacturing products, significantly enhancing their mechanical properties through solution treatment and aging (STA). This process begins with heating the bolts in a vacuum water quenching furnace to prevent oxidation and contamination. The temperature ranges from 600°C to 900°C (1112°F to 1652°F), depending on the titanium alloy and desired properties.
During the solution treatment phase, the bolts are held at the target temperature for 1-2 hours. This allows:
1. Dissolution of alloying elements into the titanium stud lug bolts matrix
2. Homogenization of the microstructure
3. Relief of internal stresses from forming operations.
After this, the bolts are rapidly quenched in water, "freezing" the homogeneous structure and preventing undesirable phases. This increases hardness and strength but may introduce internal stresses. An aging step follows, heating bolts to 480°C to 595°C (896°F to 1103°F) to control precipitation of strengthening phases. This process results in bolts with an excellent balance of strength, hardness, and toughness, ideal for demanding applications.
Grind The Rod Diameter
After heat treatment, the products undergo precision grinding to achieve the final rod diameter and a smooth surface finish, crucial for tight tolerances and proper fit. This step uses a centerless grinder, which is ideal for cylindrical workpieces. The centerless grinding method provides high precision and consistency, excellent surface finish, high production rates, and efficient handling of various lengths.
In centerless grinding, the bolt is placed between a larger grinding wheel and a smaller regulating wheel, with support from a work rest blade. The grinding wheel removes material while the regulating wheel controls rotation and feed rate. Multiple grinding passes are used, starting with coarse wheels for material removal and finishing with finer wheels for precise dimensions and surface quality.
Attention is given to wheel speed, feed rate, coolant application, wheel dressing, and in-process gauging. This results in bolts with diameters typically within ±0.013 mm (±0.0005 inches), ensuring precise fit and function in final assembly.
R Angle Strengthening
The R angle, or fillet radius, between the bolt head and shank is crucial due to high stress concentrations. To strengthen this area, manufacturers use R angle strengthening or fillet rolling. In this process, bolts are placed in a specialized rolling R machine with hardened steel rollers that apply pressure to the fillet area while the bolt rotates. The rollers match the desired fillet radius.
The rollers induce localized plastic deformation, which improves the fillet's strength and hardness through work hardening, introduces compressive residual stresses to counteract tensile stresses, smooths minor surface irregularities, and refines the grain structure for better fatigue resistance. Key parameters include rolling pressure, number of revolutions, feed rate, and roller profile. This process enhances the fatigue strength of the bolt, increasing its fatigue life by 30% or more compared to non-rolled bolts. However, care must be taken to avoid excessive rolling, which can cause brittleness or surface damage.
Thread Making
The final major step in manufacturing titanium stud lug bolts is thread creation. While traditional machining can cut threads, thread rolling is preferred for high-strength fasteners. This process improves strength, surface finish, and production rates. Threads are rolled by heating the bolt to 200°C–500°C (392°F–932°F), which reduces the force needed and prevents work hardening, allowing better material flow for uniform threads.
In thread rolling, heated bolts are processed using flat-die or cylindrical-die machines. Flat-die machines use two plates with thread profiles, while cylindrical-die machines employ rotating dies. Benefits include increased strength, improved grain structure, better surface finish, and tight dimensional accuracy. Post-rolling, bolts cool and may undergo final inspection and finishing processes.
Titanium Stud Lug Bolts Supplier
Wisdom Titanium is a reputable supplier of it, offering a range of options to meet various industry needs. Their product line includes bolts with thread sizes of M12 and M14, catering to different application requirements.
For those in need of high-quality titanium stud lug bolts or seeking a reliable product manufacturer, Wisdom Titanium welcomes inquiries. Interested parties can reach out to their sales team at sales@wisdomtitanium.com for more information on product specifications, customization options, or to discuss specific project requirements.
References
1. Leyens, C., & Peters, M. (2003). Titanium and titanium alloys: fundamentals and applications. John Wiley & Sons.
2. Boyer, R., Welsch, G., & Collings, E. W. (1994). Materials properties handbook: titanium alloys. ASM international.
3. Joshi, V. A. (2006). Titanium alloys: An atlas of structures and fracture features. CRC Press.
4. Yang, X., & Liu, C. R. (1999). Machining titanium and its alloys. Machining Science and Technology, 3(1), 107-139.
5. Wagner, L. (1999). Mechanical surface treatments on titanium, aluminum and magnesium alloys. Materials Science and Engineering: A, 263(2), 210-216.