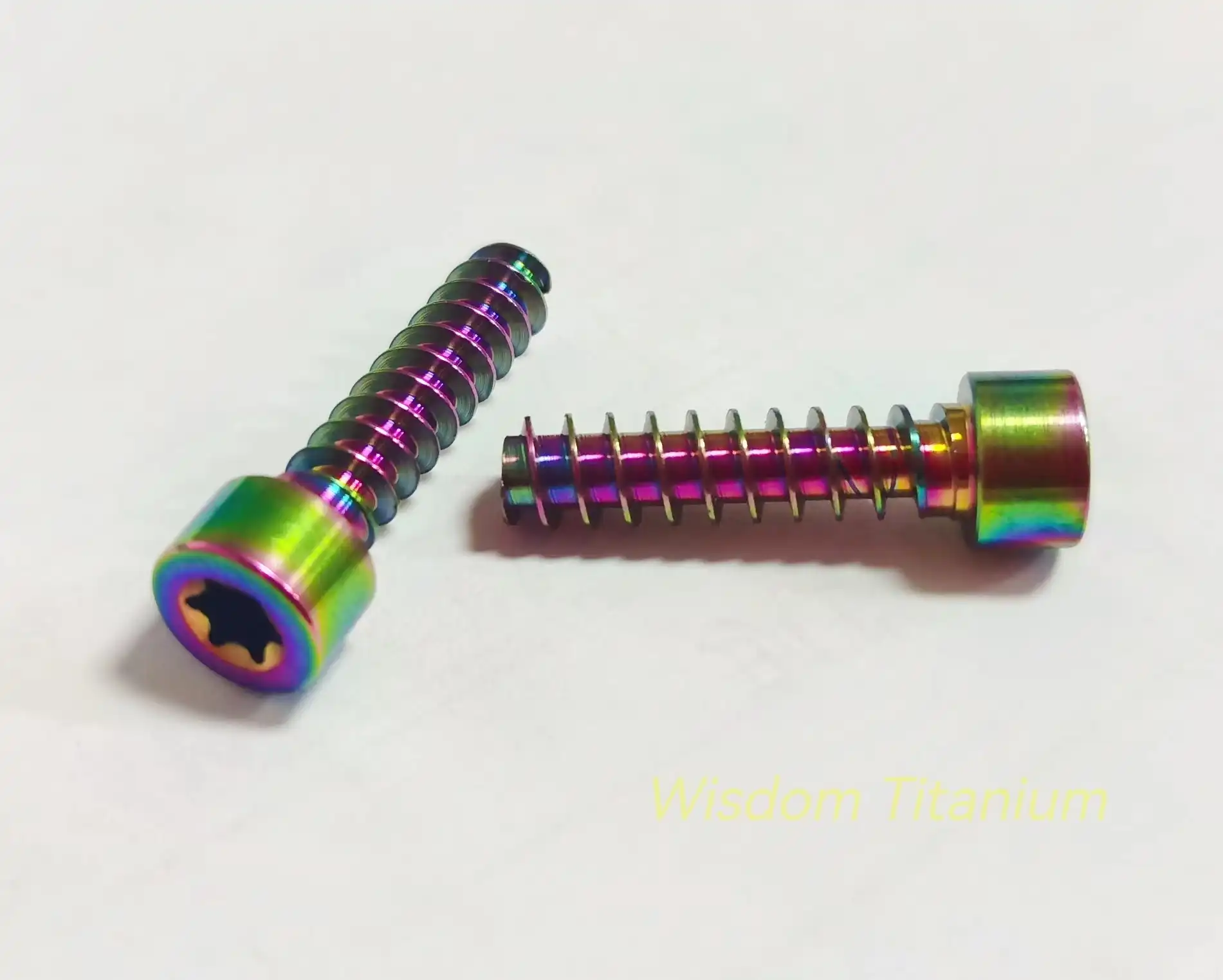
What Are the Manufacturing Processes for Titanium Screws?
Titanium screws are made using precise processes based on materials science and engineering principles that take advantage of the metal's unique properties. In the beginning, titanium is extracted from rutile and ilmenite ores using the Kroll method. In order to attain the high purity required for high-quality screws, this procedure involves reducing and purifying the titanium.
After being cleaned, titanium can be shaped into screws by turning, milling, or drilling. These procedures require specialized equipment due to titanium's inherent hardness and tendency to work harden. Tools made of hard alloys or ceramics are needed to keep precision and avoid excessive wear.
For the purpose of preserving mechanical compatibility and mechanical integrity, thread forming or cutting is extensively utilized in the production of titanium screws. Subsequent to machining, heat treatment can be utilized to further develop material properties like durability and strength while lessening stresses.
To ensure that the dimensions, surface finish, and metallurgical properties meet industry standards, rigorous checks are performed throughout the manufacturing process. Non-destructive testing methods like ultrasonic or radiographic inspection verify structural integrity, while chemical analysis ensures that the titanium's composition satisfies specifications.
Coating and anodizing are two common ways to treat a surface to make it look better and prevent corrosion. Because of these treatments, titanium screws can be used in aerospace, for instance, where they need to be resistant to fatigue and the environment.
In conclusion, cutting-edge metallurgical techniques are combined with precise machining and quality control measures in the production of titanium screws. These screws are required for aerospace components and medical implants due to their strength, lightness, and durability. They accomplish this by utilizing the distinctive properties of titanium through precise processes.
Introduction to Titanium Screws
Because of their exceptional combination of strength and lightness, titanium screws are an essential part of modern engineering and manufacturing. In industries like aerospace, where every ounce saved translates into improved fuel efficiency and performance, these properties are crucial. Due to titanium's hardness and tendency to work harden, manufacturing titanium screws requires precise machining techniques, requiring specialized tools and procedures to maintain accuracy.
Titanium screws are used in aerospace because they can withstand extreme conditions like high temperatures and corrosive environments while also reducing overall weight. In crucial parts like engine assemblies and aircraft frames, their high strength-to-weight ratio ensures structural integrity. In addition, aerospace applications require titanium because of its fatigue resistance and ability to maintain mechanical properties at high temperatures.
Due to their biocompatibility and resistance to bodily fluids, titanium screws are preferred for implants in the medical field, reducing the likelihood of rejection or infection. In order to ensure implant stability over time and promote healing, these screws seamlessly integrate with bone tissue. These screws are made with precision to meet strict medical standards, ensuring their dependability and safety during orthopedic and dental implant surgeries.
In general, advanced metallurgical techniques and stringent quality control are combined in the production of titanium screws to produce components that meet stringent performance requirements across a variety of industries. Understanding these processes demonstrates titanium's adaptability and dependability, supporting innovation and technological advancement in crucial global sectors.
Raw Material Selection
The manufacturing process of titanium screws begins with the selection of high-quality titanium alloys. Titanium alloys are chosen based on the specific requirements of the screw's intended use, taking into account factors such as strength, corrosion resistance, and compatibility with other materials. Common titanium alloys used include Ti-6Al-4V (Grade 5), Ti-6Al-4V ELI (Extra Low Interstitial), and commercially pure titanium grades, each tailored to meet different performance criteria.
Manufacturing Processes
Titanium Ingot Production
The manufacturing journey starts with the production of titanium ingots through a process called the Kroll process or the more modern and efficient Armstrong process. These processes involve reducing titanium tetrachloride with magnesium or sodium in a high-temperature reactor, resulting in titanium sponge. The sponge is then processed into titanium ingots through vacuum arc melting or electron beam melting (EBM) techniques to achieve high purity and precise alloy compositions required for screws.
Titanium Bar Production
Once titanium ingots are produced, they undergo extrusion or forging processes to form titanium bars. Extrusion involves forcing the titanium through a die under high pressure to create a uniform cross-section. Forging, on the other hand, uses compressive forces to shape the titanium into bars. Both methods improve the mechanical properties of titanium, ensuring it meets the stringent standards required for manufacturing screws.
Machining
Titanium bars are then machined into screw blanks using advanced CNC (Computer Numerical Control) machines. Machining involves precise cutting, milling, drilling, and threading operations to achieve the desired screw dimensions and thread profiles. This step requires expertise to mitigate the challenges associated with titanium's low thermal conductivity and tendency to work harden, which can affect machining efficiency and tool life.
Surface Treatment
Surface treatment processes are crucial to enhance the performance and longevity of titanium screws. Techniques such as passivation, anodizing, and chemical etching are employed to improve corrosion resistance, biocompatibility, and aesthetic appeal. Anodizing, in particular, forms a durable oxide layer on the titanium surface, offering protection against wear and environmental exposure.
Quality Control
Throughout the manufacturing process, rigorous quality control measures ensure that titanium screws meet exacting standards. Non-destructive testing (NDT) techniques, including ultrasonic testing and X-ray inspection, are used to detect internal defects and ensure dimensional accuracy. Mechanical testing such as tensile testing verifies the strength and elasticity of screws, confirming their suitability for demanding applications.
Conclusion
In conclusion, the manufacturing processes for titanium screws involve a series of intricate steps designed to harness the unique properties of titanium alloys. From the initial production of titanium ingots to the final machining and surface treatment, each stage contributes to the exceptional quality and performance of titanium screws. By understanding these processes, professionals in various industries can make informed decisions regarding the selection and application of titanium screws, ensuring optimal performance and reliability.
For more information on titanium screws or to discuss specific requirements, please contact us at: sales@wisdomtitanium.com.
References
- ASM International. (2000). ASM Handbook Volume 14B: Metal Working: Sheet Forming. Materials Park, OH: ASM International.
- Boyer, R. R. (1996). An overview on the use of titanium in the aerospace industry. Materials Science and Engineering: A, 213(1-2), 103-114.
- Davis, J. R. (Ed.). (1997). Handbook of Materials for Medical Devices. Materials Park, OH: ASM International.