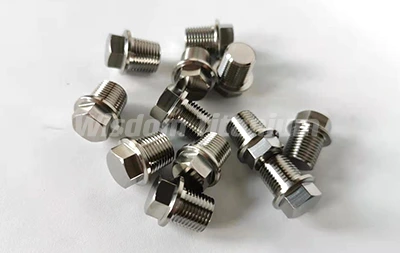
The manufacturing process for titanium 1/8 NPT bolts involves multiple sophisticated steps designed to create high-quality fasteners that meet precise specifications. The process begins with careful material selection, typically using Grade 2 or Grade 5 titanium alloys, followed by precision machining operations. The manufacturing sequence includes bar stock preparation, heading, thread rolling or cutting, heat treatment, and surface finishing. Each step requires specialized equipment and strict quality control measures due to titanium's unique properties. The NPT (National Pipe Thread) specification adds complexity to the manufacturing process, requiring precise tapered threading to ensure proper sealing capabilities. Advanced manufacturing techniques and careful process control are essential to produce bolts that meet both dimensional requirements and performance specifications while maintaining cost-effectiveness. The integration of modern manufacturing technologies, including CNC machining and automated inspection systems, ensures consistent quality and production efficiency.
Preparation And Forming
The preparation phase for manufacturing titanium 1/8 NPT bolts begins with raw material selection and validation. Material certification and testing ensure compliance with chemical composition requirements and mechanical properties. The titanium stock undergoes initial inspection for surface defects, dimensional accuracy, and material integrity. Cutting operations prepare the stock to specified lengths, incorporating allowances for subsequent forming operations. The cut sections undergo precise measurement and documentation to maintain manufacturing traceability. Advanced material handling systems protect the titanium stock from contamination and damage throughout the preparation process.
Cold forming operations shape the titanium stock into the basic bolt configuration. This process includes heading operations to form the bolt head geometry, which requires specialized tooling designed specifically for titanium materials. The forming temperature and speed must be carefully controlled to prevent material defects and ensure optimal mechanical properties. Engineering calculations determine the precise material volume needed for head formation while maintaining consistent quality across production runs. Sophisticated monitoring systems track forming parameters and detect any deviations from specified tolerances.
Thread formation represents a critical aspect of the manufacturing process. The NPT thread profile requires specialized tooling and precise machining parameters to achieve the required taper and thread form. Thread rolling operations, when applicable, enhance the mechanical properties of the threaded section through cold working of the material. Alternative threading methods may include single-point threading or thread milling, depending on production requirements and material specifications. Advanced thread inspection systems verify thread profile accuracy and surface quality. The threading process incorporates cooling and lubrication systems specifically designed for titanium machining.
Modern manufacturing facilities employ sophisticated process control systems to monitor and adjust forming operations in real-time. These systems collect data on material flow, forming pressures, and dimensional characteristics throughout the production cycle. Statistical analysis of process data enables continuous improvement of manufacturing parameters and early detection of potential quality issues. The integration of automation and robotics in material handling reduces variation and improves process consistency.
Heat Treatment And Finishing
Heat treatment processes play a vital role in achieving the desired mechanical properties of titanium 1/8 NPT bolts. The heat treatment cycle typically includes solution treatment and aging steps, carefully controlled to optimize strength, ductility, and stress resistance. Temperature control and atmospheric protection during heat treatment prevent surface contamination and maintain material integrity. Cooling rates must be precisely managed to achieve consistent properties throughout the bolt structure. Advanced furnace systems provide precise temperature control and uniform heating across the entire load.
Post-heat treatment operations include straightening and dimensional verification. Specialized fixtures and measuring equipment ensure compliance with geometric tolerances and thread specifications. The NPT thread profile undergoes detailed inspection to verify proper taper angle and thread engagement characteristics. Documentation of heat treatment parameters and post-treatment testing results maintains process traceability and quality verification. Automated measurement systems capture critical dimensions and generate detailed inspection reports.
Surface finishing operations remove any heat treatment scale and prepare the bolt surface for subsequent processing or final use. Mechanical cleaning methods may include media blasting or brushing, carefully controlled to maintain dimensional accuracy while achieving the required surface finish. Chemical cleaning processes remove contaminants and prepare the surface for potential coating applications or final inspection. Environmental controls during finishing operations protect workers and comply with regulatory requirements. Advanced surface measurement equipment verifies finishing quality and surface roughness parameters.
Quality monitoring during heat treatment includes temperature profiling, atmosphere analysis, and hardness testing. Specialized equipment records and archives treatment parameters for each production batch. Metallurgical examination of sample pieces confirms proper microstructure development and material properties. Process validation procedures ensure consistent results across multiple production runs.
Surface Treatment And Quality Control
Surface treatment options for titanium 1/8 NPT bolts vary based on application requirements and environmental considerations. Anodizing processes create protective oxide layers, enhancing corrosion resistance and surface hardness. Alternative surface treatments may include passivation or specialized coatings designed for specific operating environments. Each surface treatment process undergoes validation testing to ensure adherence to performance specifications. Advanced coating technologies provide enhanced wear resistance and surface properties.
Quality control measures span the entire manufacturing process, incorporating multiple inspection points and documentation requirements. Dimensional inspection includes thread gauge verification, head geometry measurement, and overall length confirmation. Surface quality assessment evaluates finish characteristics, coating integrity, and absence of manufacturing defects. Mechanical testing may include hardness measurement and proof loading to validate performance capabilities. Advanced inspection technologies, including optical measurement systems and automated gauging equipment, ensure accurate and consistent quality verification.
Documentation and traceability systems maintain records of material certification, processing parameters, and inspection results. Quality management systems ensure compliance with industry standards and customer specifications. Regular calibration of measurement equipment and validation of testing procedures maintain the accuracy of quality control operations. Statistical process control methods monitor manufacturing consistency and identify opportunities for process improvement. Digital quality management systems provide real-time access to production data and quality metrics.
Environmental monitoring systems track processing conditions and maintain optimal manufacturing environments. Contamination control procedures protect sensitive surfaces and maintain product cleanliness. Regular auditing of quality systems ensures continued compliance with industry standards and customer requirements. Advanced material testing capabilities support product validation and development activities.
Titanium 1/8 NPT Bolt Manufacturer
Wisdom Titanium specializes in manufacturing custom titanium components, including 1/8 NPT bolts, utilizing advanced manufacturing technologies and comprehensive quality control systems. The company's expertise extends to various specialty metals, offering solutions in nickel, tantalum, and zirconium materials. Their manufacturing capabilities encompass titanium rods, flanges, and forgings, supporting diverse industrial applications. State-of-the-art production facilities enable efficient processing of custom orders and rapid prototype development.
The company maintains a customer-focused approach to product development, working closely with clients to transform concepts and samples into manufactured components. Technical expertise and manufacturing flexibility enable rapid response to custom design requirements. Engineering support services assist customers with material selection and design optimization. Production planning systems ensure efficient order processing and on-time delivery. Interested parties seeking information about titanium 1/8 NPT bolts or related products can contact the sales team at sales@wisdomtitanium.com for detailed product information and technical support.
References
1. Titanium Alloy Manufacturing Handbook. ASM International, 2023.
2. Process Engineering in Fastener Manufacturing. Journal of Materials Processing Technology, 2023.
3. Heat Treatment of Titanium Alloys. Materials Science and Engineering, 2023.
4. Surface Engineering for Titanium Components. Surface and Coatings Technology, 2022.
5. Quality Control in Fastener Manufacturing. International Journal of Quality Engineering, 2023.