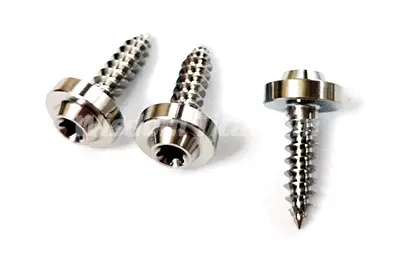
What Are the Key Differences Between Titanium and Aluminum Screws?
When it comes to industrial fasteners, choosing between materials like titanium and aluminum can have a significant impact on performance, durability, and overall effectiveness. Because I am a mechanical engineer with a background in materials science, I frequently compare these metals, particularly when they are used as screws. It is essential to comprehend the distinctions between titanium and aluminum in order to select the ideal applications.
Titanium screws are well-known for their corrosion resistance, biocompatibility, and high strength-to-weight ratio. Because it naturally forms a protective oxide layer (TiO2) when exposed to oxygen, titanium is ideal for applications where dependability and longevity are crucial, such as aerospace, medical implants, and marine environments. The material's strength allows for robust fastening while reducing weight in industries where every ounce counts.
On the other hand, aluminum screws are lightweight and possess excellent mechanical properties like high electrical and thermal conductivity. Because of its low density, aluminum is ideal for use in industries like electronics and automobiles where weight reduction is of the utmost importance. Aluminum, on the other hand, is more susceptible to corrosion than titanium, so it sometimes needs protective coatings or alloys to keep its integrity.
Which screw to use—aluminum or titanium—will ultimately be determined by the application's specific requirements. Titanium shines in environments that require high strength, corrosion resistance, and biocompatibility, whereas aluminum shines when lightweight construction and good conductivity are prioritized. The environment, mechanical stresses, and how long it will last in use are important considerations when choosing between the two materials, which each have their own advantages.
I always look at these things as a mechanical engineer with a focus on materials science to make sure industrial fasteners work well and last as long as possible. I want to match the right material to every application's particular necessities to guarantee most extreme productivity and trustworthiness.
Titanium Screws: Lightweight and Exceptionally Strong
Titanium is the material of choice for industries that place an emphasis on lightweight yet durable materials because of its exceptional strength-to-weight ratio. Steel screws are much heavier, but titanium screws are just as strong, if not stronger. This quality is particularly helpful in aviation applications, where lessening weight straightforwardly brings about superior airplane and rocket execution and eco-friendliness.
Titanium has a weight advantage as well as exceptional consumption opposition, which is fundamental in conditions where dampness, synthetics, or outrageous temperatures are available. This resilience is due to the surface formation of a protective oxide layer (TiO2) that prevents corrosion and maintains structural integrity over time. As a result, titanium screws are ideal for outdoor applications like the construction and marine industries, which frequently encounter harsh conditions.
Titanium's biocompatibility, which makes it an excellent material for medical implants, is another outstanding quality. Because the metal works well with human tissue, patients are less likely to have adverse reactions or reject the implant, which improves patient outcomes and extends the implant's lifespan. Titanium is often used in dental implants, orthopedic implants, and other surgical instruments where long-term viability and compatibility with the human body are important because of its biocompatibility.
All in all, titanium screws succeed not just as far as solidarity to-weight proportion yet additionally regarding biocompatibility and protection from consumption. Titanium is a material that is required in numerous fields, including aerospace, marine, and medical and healthcare applications, due to titanium screw characteristics. As technology advances, innovations that benefit industry and human health continue to be driven by titanium's versatility and performance.
Aluminum Screws: Lightweight and Cost-Effective
Aluminum, like titanium, is prized for its lightweight properties, although it is less dense than titanium. This characteristic makes aluminum screws ideal for applications where weight reduction is critical but not at the expense of strength. Industries such as automotive and consumer electronics benefit from aluminum screws due to their ability to reduce overall product weight without compromising structural integrity.
In addition to its lightweight nature, aluminum is highly corrosion-resistant in certain environments. However, compared to titanium, it tends to be more susceptible to corrosion, especially in acidic or alkaline conditions. Surface treatments and coatings can enhance aluminum's corrosion resistance, but this adds complexity and cost to manufacturing processes.
One of the significant advantages of aluminum screws is their cost-effectiveness. Aluminum is more abundant and less expensive than titanium, making it a preferred choice in applications where cost is a primary consideration without compromising too much on performance. Industries that prioritize affordability and ease of manufacturing often opt for aluminum screws for their projects.
Choosing Between Titanium and Aluminum Screws
The decision between titanium and aluminum screws ultimately hinges on the specific requirements of the application:
-
Strength and Durability: For applications requiring the highest strength-to-weight ratio and exceptional durability, titanium screws are preferable.
-
Weight and Cost: If weight reduction is critical but cost is a factor, aluminum screws offer a good balance between performance and affordability.
-
Corrosion Resistance: In environments where corrosion resistance is paramount, particularly in marine or aerospace applications, titanium screws provide superior protection over aluminum.
Conclusion
In conclusion, both titanium and aluminum screws offer unique advantages depending on the application's requirements. Titanium excels in strength, durability, and corrosion resistance, albeit at a higher cost. Aluminum, on the other hand, provides lightweight solutions at a lower price point, albeit with slightly less corrosion resistance in certain conditions. Understanding these differences allows engineers and manufacturers to make informed decisions that optimize performance, longevity, and cost-effectiveness in their projects.
If you want to learn more about titanium screws, welcome to contact us: sales@wisdomtitanium.com.