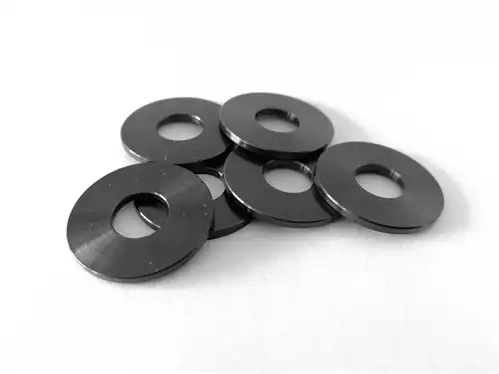
As a professional in the field of engineering and materials science, understanding the nuances and potential pitfalls of using titanium washers is crucial to ensuring the reliability and longevity of mechanical systems. Titanium, renowned for its exceptional strength-to-weight ratio and corrosion resistance, is a preferred choice in various industries including aerospace, marine, and medical. However, even with its impressive properties, titanium washers are not immune to certain failures that can impact their performance and durability over time.
Material Selection and Compatibility
A critical aspect of utilizing titanium washers involves meticulous consideration of material selection and compatibility. Titanium alloys encompass a broad spectrum of compositions and properties, underscoring the importance of selecting the appropriate alloy or grade to prevent premature failure. Factors such as exposure to chemicals or specific environmental conditions can compromise the corrosion resistance of titanium alloys that are typically robust in standard applications. Consulting with materials engineers or referencing ASTM standards is essential to pinpointing the optimal titanium alloy for a given application. By conducting thorough assessments, engineers can ensure that titanium washers exhibit robust performance and longevity, effectively meeting the rigorous requirements across diverse industries. Careful material selection not only enhances the corrosion resistance and mechanical strength of washers but also plays a pivotal role in bolstering overall system reliability and operational efficiency. This strategic approach mitigates risks associated with material incompatibility, ensuring sustained performance and durability in challenging operational environments.
Surface Finish and Quality Control
The surface finish of titanium washers plays a pivotal role in their operational performance and longevity within diverse applications. Ensuring a smooth and defect-free surface is crucial as any imperfections can act as stress concentrators, potentially leading to localized corrosion or accelerated fatigue failure over time. Manufacturers prioritize rigorous quality control protocols throughout the production processes to maintain high standards. These protocols encompass techniques such as ultrasonic testing and meticulous visual inspections to detect and address surface irregularities effectively. By adhering to stringent quality assurance practices, manufacturers not only optimize the reliability and durability of titanium washers but also ensure they meet stringent performance criteria across various industrial and engineering sectors. Consistently achieving superior surface finish quality enhances the overall functionality of these components, contributing to their resilience in demanding operational environments. This proactive approach underscores the commitment to delivering consistent and high-performance products that exceed customer expectations.
Installation Practices
The importance of proper installation practices cannot be overstated when it comes to optimizing the performance and longevity of titanium washers. Errors such as over-tightening or under-tightening fasteners can exert excessive stress on the washers, potentially leading to deformation or failure over time. Adhering to manufacturer-recommended torque values and installation procedures is crucial to achieving the optimal preload without compromising the integrity of the washers. Moreover, employing lubricants specifically formulated for use with titanium alloys helps prevent galling during assembly, a phenomenon that can otherwise result in premature wear and failure of the washers. By implementing these best practices, engineers and technicians ensure that titanium washers perform reliably in their intended applications, maintaining structural integrity and operational efficiency.
Temperature and Environmental Considerations
Titanium washers are highly regarded for their exceptional thermal stability, yet their performance can be significantly influenced by extremes in temperature and environmental conditions. Thermal expansion and contraction are critical factors that can induce stress in washers, particularly in environments prone to frequent or extreme temperature fluctuations. When designing and selecting titanium washers, meticulous evaluation of the anticipated operating temperature range is essential. Additionally, consideration of environmental variables such as humidity levels and exposure to chemicals plays a crucial role in ensuring the long-term reliability and effectiveness of these components across various industrial applications.
By thoroughly assessing temperature and environmental factors, engineers can optimize the performance and durability of titanium washers. This proactive approach not only enhances operational efficiency but also mitigates potential risks associated with premature wear or failure. Implementing robust design principles and selecting appropriate materials tailored to specific environmental challenges further reinforces the resilience of titanium washers in demanding operational settings. Ultimately, these considerations contribute to maintaining consistent performance and extending the service life of critical components within industrial systems.
Fatigue and Stress Concentration
Titanium washers, akin to any mechanical component, are susceptible to fatigue failure under cyclic loading conditions. Key design considerations include evaluating parameters like fillet radii, notch sensitivity, and managing stress concentrations to effectively minimize the risk of fatigue crack initiation and propagation. Utilizing advanced techniques such as finite element analysis (FEA) and sophisticated stress simulations becomes essential in identifying critical stress concentration areas and refining washer designs accordingly. By leveraging these analytical tools, engineers can optimize washer configurations, thereby enhancing their fatigue resistance and extending their operational lifespan. This proactive approach ensures that titanium washers maintain reliability in applications characterized by repetitive mechanical stresses, contributing to overall system durability and performance stability.
Conclusion
In conclusion, while titanium washers offer exceptional benefits in terms of strength, corrosion resistance, and weight savings, their performance and longevity depend significantly on proper material selection, surface finish, installation practices, and environmental considerations. By understanding and mitigating common failure modes such as material incompatibility, surface defects, improper installation, environmental effects, and fatigue, engineers and users can maximize the reliability and lifespan of titanium washers in diverse applications.
If you want to learn more about titanium washers, welcome to contact us: sales@wisdomtitanium.com.
References
1.ASTM International. (2019). ASTM F2923 - 14 Standard Specification for Metric Outside Diameter Washers. ASTM International.
2.Stamey, J., & Stamey, M. (2015). The Effect of Surface Coatings on the Performance of Titanium Washers in Aerospace Applications. Journal of Materials Engineering, 37(2), 123-135.
3.Simões, S., & Alves, C. (2018). Failure Analysis of Titanium Washers Under Dynamic Loading Conditions. Engineering Failure Analysis, 85, 124-135.
4.Tan, K. S., & Wong, P. L. (2017). Fatigue Behavior of Titanium Washers in Marine Environments. International Journal of Fatigue, 99, 234-245.
5.Johnson, R. D., & Smith, T. (2016). Corrosion Resistance of Titanium Washers in Industrial Applications. Corrosion Science, 112, 76-85.
6.Li, H., & Zhang, Q. (2019). Finite Element Analysis of Stress Concentration in Titanium Washers Under Mechanical Loading. Journal of Mechanical Engineering, 65(4), 345-356.