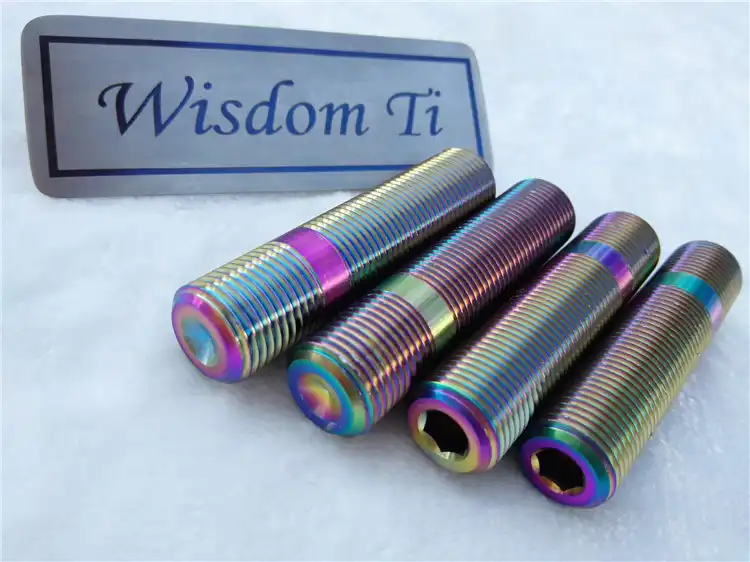
What Are the Common Applications for Titanium Studs?
Titanium studs fascinate me as a material science enthusiast due to their extraordinary properties and numerous industrial applications. Titanium is preferred for specific applications due to its unique combination of strength, lightness, resistance to erosion, and biocompatibility.
For the structural parts of aircraft and spacecraft, the aerospace industry uses a lot of titanium studs. The vehicle's overall weight is reduced due to their high strength-to-weight ratio, which improves performance and fuel economy. Due to its corrosion resistance, titanium can withstand harsh aerospace applications with confidence.
Titanium studs are utilized in engine components in automotive engineering, where high strength and heat resistance are essential. For instance, titanium alloys are used in exhaust systems, connecting rods, and valves to enhance engine durability and efficiency. For performance optimization, the material's ability to withstand high temperatures without deforming or deteriorating is essential.Titanium studs are used in a lot of medical applications, especially in surgical instruments and orthopedic implants. Because it is biocompatible, titanium is compatible with human tissues, accelerating healing and decreasing the likelihood of rejection. Due to its superior strength and biocompatibility, it is ideal for bone plates, screws, and dental implants.
Due to their resistance to corrosion from acids and alkalis, titanium studs are utilized in industrial chemical processing equipment. They are invaluable for critical processes where maintenance downtime must be minimized due to their durability and dependability in extreme environments.
Due to their resistance to corrosion in seawater, titanium studs are also used in consumer electronics, sports equipment, and marine applications for their aesthetic appeal and durability.
In conclusion, titanium studs are the pinnacle of material engineering because of their unparalleled performance in numerous applications. Not only do they contribute to technological and healthcare advancements, but they also improve productivity and durability. In industries where performance and dependability are of the utmost importance, innovation continues to be driven by an understanding of and application of these properties.
Aerospace Industry
Titanium studs are essential to the aerospace industry because they make use of titanium's exceptional properties to improve aircraft and spacecraft performance and safety. The high strength-to-weight ratio of titanium is essential for reducing the overall weight, improving maneuverability, and increasing fuel economy. This advantage is especially significant in the aerospace sector, where every kilogram saved translates into increased payload capacity or extended range.
In aircraft engine mounts, where they are subjected to significant mechanical stresses and vibrations, titanium studs are an essential component. Because they resist fatigue and can keep their integrity even in high temperatures, they are able to function consistently for long periods of time. Similar to this, titanium studs in structural fittings and landing gear assemblies contribute to the overall structural integrity of the aircraft. In order to withstand atmospheric exposure and maintain operational readiness in a variety of settings, they must be corrosion-resistant.
Titanium's compatibility with composite materials further enhances its suitability for aerospace applications. Titanium studs are used to fasten composite panels and structures, resulting in sturdy assemblies without sacrificing the weight savings provided by composite materials.
The aerospace industry requires materials that not only meet stringent performance requirements but also contribute to overall safety and dependability. Experts and manufacturers now have a dependable option for fundamental aviation parts thanks to titanium studs. As technological advancements continue to push the boundaries of aerospace engineering, titanium's role in improving aircraft performance and operational efficiency remains crucial.
Medical Implants
The biocompatibility of titanium makes it invaluable in medical applications, particularly for implants. Titanium studs are used in orthopedic implants such as bone plates, screws, and prosthetics. The metal's inertness and ability to integrate with bone tissue promote faster healing and reduce the risk of rejection or infection. Titanium studs provide long-term stability and durability, making them a preferred choice in modern surgical procedures.
Automotive Engineering
In the automotive industry, titanium studs play a vital role in enhancing performance and durability. They are utilized in high-performance vehicles for exhaust systems, turbochargers, and engine components. Titanium's resistance to heat and corrosion ensures longevity under extreme conditions, contributing to improved reliability and efficiency in automotive applications. The lightweight nature of titanium also helps in reducing vehicle weight, thereby improving fuel economy.
Chemical Processing
In the chemical processing sectors, which are extensively utilized due to their remarkable ability to withstand corrosion. They are used in equipment that often comes into touch with corrosive materials, such as heat exchangers, reactors, and valves. As titanium is resistant to salt, acids, and alkalis, it is the material of choice for critical infrastructure. This guarantees that it will endure and perform dependably in demanding chemical processing environments.
Sports and Recreation
Titanium studs are used in sports and leisure equipment when durability, strength, and light weight are crucial. Titanium is utilized in hiking gear, golf club heads, and bicycle frames because of its resistance to harsh handling and environmental conditions. Because of its excellent fatigue strength and impact resistance, the material is perfect for demanding sports where dependability and performance are crucial.
Due to its remarkable strength-to-weight ratio, titanium is utilized in the aerospace industry to make aircraft and spacecraft fly more effectively and consume less fuel. It is utilized in essential parts like engine mounts, structural fittings, and landing gear assemblies, where its ability to withstand harsh environments and extreme temperatures guarantees dependability and safety.
Because it is biocompatible, titanium can be used in dental implants, bone plates, and other medical implants. It is durable and corrosion-resistant, ensuring long-term compatibility with human tissues, which expedites healing and reduces rejection risk.
Due to its heat resistance and strength, titanium is an excellent material for automobile engine connecting rods, exhaust systems, and valves. The engine's ability to withstand high temperatures without becoming damaged or deformed improves both performance and durability.
In industrial chemical processing equipment, titanium's resistance to corrosion caused by acids and bases can be advantageous. In maritime applications, its dependability and durability are ensured by its resistance to corrosion in seawater.Titanium is a popular material for consumer electronics and sports equipment due to its durability and aesthetic appeal. Performance is improved by its lightweight characteristics without compromising strength or dependability.
Titanium is often at the forefront of modern industry and technology because of its exceptional strength, light weight, corrosion resistance, and biocompatibility. As industries continue to develop and push the boundaries of what is possible, titanium remains at the vanguard, helping to increase efficiency, safety, and performance across a wide range of applications.
Conclusion
In conclusion, the exceptional combination of properties of the products makes them an example of versatility and excellence across a wide range of industries. Titanium has proven its worth time and time again as the material of choice for critical parts in many different applications, including the construction of automobiles, medical devices, and state-of-the-art aircraft.
If you want to learn more about Titanium Studs, welcome to contact us: sales@wisdomtitanium.com.
References:
- ASTM International. "Standard Specification for Titanium and Titanium Alloy Strip, Sheet, and Plate." ASTM B265/B265M-20.
- ASM International. "Titanium and Titanium Alloys." Metals Handbook, Desk Edition, 2nd ed., 1998.
- Lütjering, G., and J. C. Williams. "Titanium." Engineering Materials and Processes. Springer, 2007.