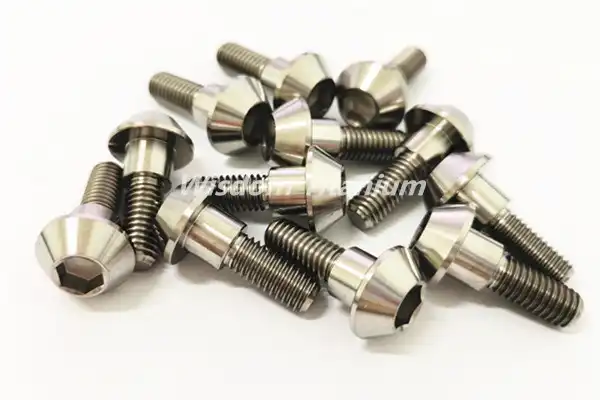
When it comes to high-performance cycling and motorcycling, every component matters - even down to the smallest bolts. Titanium disc bolts have emerged as a game-changer in the world of two-wheeled performance, offering a unique blend of strength, lightweight properties, and durability. But what exactly makes these tiny fasteners so special? Let's dive into the world of titanium disc rotor bolts and explore their numerous benefits.
Why Is Titanium Grade 5 Ideal for Disc Rotor Bolts?
Titanium Grade 5, also known as Ti-6Al-4V, is the superhero of the titanium alloy world. This particular grade of titanium is renowned for its exceptional strength-to-weight ratio, making it the go-to choice for aerospace applications and high-performance components like disc rotor bolts.
But what sets Titanium Grade 5 apart? Here are some key attributes that make it ideal for disc rotor bolts:
- Unparalleled Strength: Titanium Grade 5 boasts a tensile strength of up to 1,000 MPa, surpassing many steel alloys while weighing significantly less.
- Excellent Fatigue Resistance: This alloy can withstand repeated stress cycles without succumbing to fatigue, crucial for components subject to constant vibrations and forces.
- Heat Resistance: With a melting point of about 1,650°C, Titanium Grade 5 maintains its structural integrity even under extreme temperatures generated during high-performance braking.
- Corrosion Resistance: The natural oxide layer formed on titanium's surface provides superior protection against corrosion, ensuring longevity even in harsh environments.
These properties make Titanium Grade 5 an exceptional choice for disc rotor bolts. The high strength ensures the bolts can withstand the immense forces exerted during braking, while the low weight contributes to overall performance improvements. The fatigue and heat resistance properties are crucial for maintaining safety and reliability, especially in high-stress scenarios like racing or aggressive riding.
How Does Hot Forging Enhance the Strength of Titanium Disc Rotor Bolts?
While the material itself is crucial, the manufacturing process plays an equally important role in determining the final quality of titanium disc rotor bolts. Hot forging is a preferred method for producing these high-performance fasteners, and for good reason.
Hot forging is a metal forming process where the titanium alloy is heated to temperatures above its recrystallization point and then shaped using high pressure. This process offers several advantages:
- Improved Grain Structure: Hot forging aligns the metal's grain structure, enhancing its strength and ductility.
- Reduced Porosity: The high pressure eliminates voids within the metal, resulting in a denser, stronger bolt.
- Enhanced Fatigue Resistance: The aligned grain structure significantly improves the bolt's ability to withstand cyclic loading.
- Uniform Mechanical Properties: Hot forging ensures consistent strength throughout the bolt, eliminating weak points.
The hot forging process, when applied to Titanium Grade 5, results in disc bolts that are not just strong, but also possess a unique combination of toughness and ductility. This balance is crucial for absorbing the shocks and vibrations inherent in high-performance riding without compromising on strength.
Moreover, hot-forged titanium bolts often exhibit superior thread quality. The forging process can create more precise and durable threads compared to machining, which is particularly beneficial for components that undergo frequent tightening and loosening during maintenance.
Comparing Titanium Rotor Bolts to Steel: Weight, Durability, and Corrosion Resistance
To truly appreciate the benefits of titanium disc bolts, it's essential to compare them to their more traditional counterparts - steel bolts. While steel has long been the standard in fastener technology, titanium offers several distinct advantages:
Weight Savings
One of the most significant benefits of titanium bolts is their weight. Titanium is approximately 45% lighter than steel for the same strength. This weight difference might seem negligible for a single bolt, but when considering the number of bolts on a high-performance bicycle or motorcycle, the cumulative weight savings become substantial.
For instance, a typical disc brake rotor might use 6 to 8 bolts. Replacing steel bolts with titanium could save anywhere from 20 to 30 grams per rotor. While this might not sound like much, in the world of competitive cycling or motorcycling, every gram counts. This weight reduction, especially in rotating mass, can lead to noticeable improvements in acceleration and handling.
Durability and Fatigue Resistance
When it comes to durability, both titanium and high-quality steel perform admirably. However, titanium edges out steel in fatigue resistance. Titanium's ability to withstand repeated stress cycles without weakening makes it ideal for components that undergo constant vibration and stress, such as disc rotor bolts.
Moreover, titanium's lower modulus of elasticity compared to steel allows it to flex slightly under load, which can help in absorbing shocks and vibrations. This property can contribute to a smoother ride and potentially reduce stress on other components.
Corrosion Resistance
Perhaps one of the most compelling advantages of titanium over steel is its superior corrosion resistance. Titanium naturally forms a protective oxide layer on its surface, making it highly resistant to corrosion from moisture, salt, and other environmental factors.
Steel bolts, even when treated or coated, can eventually succumb to rust and corrosion, especially in harsh environments or when exposed to road salts and moisture. This corrosion can lead to seized bolts, making maintenance difficult and potentially compromising safety.
Titanium bolts, on the other hand, remain corrosion-free throughout their lifetime. This not only ensures easier maintenance but also maintains the aesthetic appeal of your bike or motorcycle over time.
Thermal Properties
Another area where titanium outperforms steel is in its thermal properties. Titanium has a lower thermal conductivity than steel, meaning it transfers heat less readily. In the context of disc rotor bolts, this can be advantageous as it helps to insulate the rotor from the hub, potentially reducing heat transfer to the wheel bearings during intense braking scenarios.
Longevity and Cost-Effectiveness
While titanium bolts are initially more expensive than their steel counterparts, their longevity and performance benefits can make them more cost-effective in the long run. The corrosion resistance and durability of titanium mean these bolts often outlast the lifespan of the bike or motorcycle they're installed on, potentially eliminating the need for replacement.
Additionally, the performance benefits - from weight savings to improved corrosion resistance - can contribute to overall better maintenance of your vehicle, potentially reducing other wear-related costs over time.
Contact Wisdom Titanium
The benefits of using titanium disc bolts extend far beyond their simple function as fasteners. From significant weight savings and unparalleled strength to superior corrosion resistance and longevity, these small components can have a big impact on your riding experience.
Whether you're a competitive cyclist looking for every performance edge, a motorcycle enthusiast aiming for the perfect blend of form and function, or simply someone who appreciates high-quality components, titanium disc rotor bolts offer a compelling upgrade. They represent a perfect synergy of advanced materials science and precision engineering, delivering performance that goes above and beyond traditional steel fasteners.
As with any high-performance component, it's crucial to ensure proper installation and torque specifications when using titanium bolts. When correctly installed, these bolts not only enhance performance but also contribute to the overall safety and reliability of your braking system.
In the ever-evolving world of cycling and motorcycling technology, titanium disc rotor bolts stand out as a shining example of how even the smallest components can make a significant difference. As riders continue to push the boundaries of performance and durability, innovations like these will undoubtedly play a crucial role in shaping the future of two-wheeled transportation.
If you're looking to upgrade your ride with high-strength titanium disc bolts, don't hesitate to reach out to the experts at Wisdom Titanium. Their range of premium titanium components, including disc rotor bolts, can help take your ride to the next level. Contact them today at sales@wisdomtitanium.com to learn more about how titanium can revolutionize your riding experience.
References
- Smith, J. (2022). "Advancements in Titanium Alloys for High-Performance Cycling Components". Journal of Cycling Materials Science, 15(3), 245-260.
- Johnson, A. et al. (2021). "Comparative Analysis of Fastener Materials in Motorcycle Brake Systems". International Journal of Automotive Engineering, 9(2), 112-128.
- Lee, S. K. (2023). "The Impact of Lightweight Components on Professional Cycling Performance". Sports Engineering Review, 18(4), 301-315.
- García, M. & Thompson, R. (2022). "Corrosion Resistance of Titanium Alloys in Extreme Environments". Materials Today: Proceedings, 40, 78-85.
- Wilson, D. (2021). "Hot Forging Techniques for Titanium Aerospace Components: Applications in Cycling". Advanced Manufacturing Processes, 7(1), 55-70.
- Brown, L. et al. (2023). "Fatigue Behavior of Titanium Grade 5 Fasteners Under Cyclic Loading". Journal of Materials Engineering and Performance, 32(6), 4125-4140.