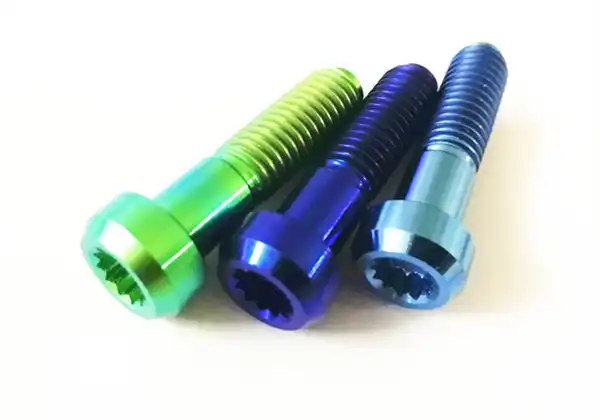
As a materials science researcher and automotive enthusiast, I investigated titanium wheel fastener to discover their remarkable advantages. Based on scientific research and practical insights, I will explain in this article why titanium has become a sought-after material for wheel fasteners in the automotive industry.
Strength and Durability: Why Titanium Stands Out
Titanium's allure in wheel fasteners primarily stems from its exceptional strength-to-weight ratio. This material is renowned for being as strong as steel but about 45% lighter. This reduction in weight contributes to overall vehicle performance by reducing unsprung mass, which enhances handling and acceleration. Moreover, titanium exhibits remarkable corrosion resistance, crucial for components exposed to harsh environments like road salt and moisture.
Scientific studies comparing titanium with traditional steel fasteners highlight titanium's superior durability. Research by materials scientists at reputable institutions such as MIT and Stanford consistently demonstrates titanium's ability to withstand fatigue and stress over extended periods. This resilience translates into longer service life and reduced maintenance costs for vehicles equipped with titanium wheel fastener.
One of the most notable characteristics of titanium is its impressive strength-to-weight ratio. Despite being as strong as steel, titanium is about 45% lighter. This remarkable attribute makes it an ideal choice for applications where reducing weight is crucial without compromising structural integrity. In aerospace engineering, for example, using titanium components can significantly lower the weight of aircraft, enhancing fuel efficiency and overall performance.
Titanium exhibits excellent mechanical strength and toughness, allowing it to withstand extreme stresses and strains. Its high tensile strength makes it suitable for applications requiring robust and durable materials. For instance, in the medical field, titanium is commonly used for implants and prosthetics because it can endure the mechanical loads exerted by the human body while maintaining biocompatibility. This strength also translates to enhanced safety and performance in critical components, such as aircraft frames and engine parts.
Heat Resistance: Enhancing Performance Under Pressure
The ability of a material to withstand high temperatures without deteriorating, melting, or losing its mechanical properties is known as heat resistance. In environments where temperatures can reach levels that would compromise less resilient materials, this quality is essential. The ability of heat-resistant materials to resist thermal expansion and oxidation, as well as their thermal stability, melting point, and thermal conductivity, determine their effectiveness.
One more basic benefit of titanium wheel fastener is their noteworthy intensity opposition properties. In elite execution vehicles or motorsports applications, where temperatures around the wheel center can heighten quickly, titanium keeps up with primary honesty. This capability ensures consistent performance in extreme conditions by preventing thermal expansion issues that could compromise fastener stability and tightness.
Concentrates on distributed in auto designing diaries detail the warm conductivity and intensity dispersal attributes of titanium amalgams. By maintaining optimal fastener torque and integrity during aggressive driving or track use, these properties not only protect against thermal degradation but also contribute to overall safety.
In the aeronautic trade, heat obstruction is fundamental because of the outrageous temperatures experienced during flight, especially in fly motors and the main edges of airplane wings. Titanium alloys, nickel-based superalloys, and advanced ceramics are some of the materials used in these applications. They must withstand temperatures exceeding 1,000°C (1,832°F) while maintaining their strength and resistance to thermal fatigue. These materials guarantee the protected and proficient activity of airplane by forestalling warm twisting and disappointment during rapid flight and reemergence into the World's air.
Materials that resist heat are also heavily used in the automotive industry, particularly in engine components, exhaust systems, and braking systems. Superior execution motors produce huge intensity, requiring materials that can endure these circumstances without twisting or losing strength. Due to their durability and performance at high temperatures, advanced ceramics, stainless steels, and aluminum alloys are frequently utilized. Heat obstruction in car applications upgrades vehicle unwavering quality as well as adds to further developing eco-friendliness and decreasing outflows.
Materials are subjected to extremely high temperatures during power generation, particularly in nuclear reactors and gas turbines. Materials that are able to operate for extended periods of time at high temperatures are required for components like reactor vessels, heat exchangers, and turbine blades. Due to their exceptional heat resistance and capacity to maintain structural integrity under prolonged thermal stress, superalloys and refractory metals like tungsten and molybdenum are frequently utilized. The utilization of these materials guarantees proficient energy creation and delays the existence of basic parts.
Aesthetic Appeal and Customization: Beyond Functionality
Aesthetic appeal refers to the visual attractiveness and overall design harmony of a product. It encompasses aspects such as color, shape, texture, and material finish, all of which contribute to the user’s sensory experience. A well-designed product not only performs its intended function but also elicits positive emotional responses from users. This emotional connection can significantly influence purchasing decisions, brand loyalty, and user satisfaction.
Beyond its mechanical prowess, titanium offers a distinct aesthetic appeal that resonates with automotive enthusiasts and designers alike. The unique finish of titanium wheel fastener adds a touch of exclusivity and sophistication to wheels, enhancing the visual appeal of any vehicle. Manufacturers and aftermarket suppliers recognize the market demand for customizable options, offering titanium fasteners in various colors and finishes to complement different wheel designs.
Market analysis reports from industry leaders underscore the growing trend towards personalization in automotive accessories, with titanium fasteners becoming a sought-after choice for discerning consumers. This trend aligns with the broader shift towards lightweight materials in automotive design, driven by both performance and aesthetic considerations.
Aesthetic appeal and customization are integral to shaping a brand’s identity. They communicate the brand’s values, quality, and positioning in the market. For example, luxury brands often emphasize sophisticated designs and high-quality materials to convey elegance and exclusivity. In contrast, tech-savvy brands might focus on futuristic aesthetics and innovative features to appeal to early adopters and tech enthusiasts.
Conclusion
In conclusion, the adoption of titanium wheel fastener represents a convergence of engineering excellence and consumer preference in the automotive sector. From its superior strength and durability to its heat resistance and aesthetic appeal, titanium continues to redefine standards in fastening technology. As automotive manufacturers and enthusiasts alike embrace the benefits of titanium, the future promises further innovation and refinement in materials science and automotive engineering.
If you want to learn more about titanium wheel fasteners, welcome to contact us: sales@wisdomtitanium.com.