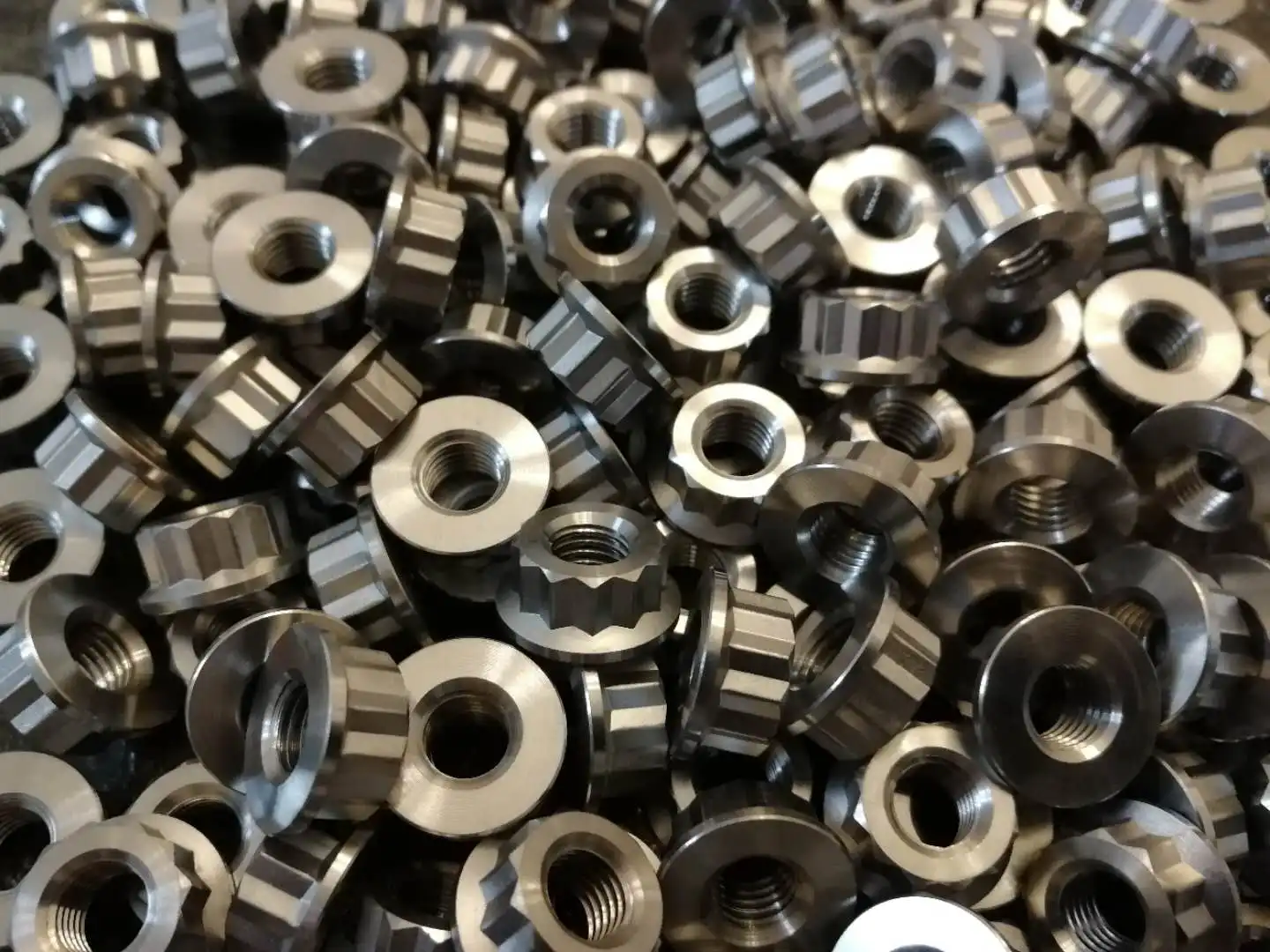
Unlocking the advantages of titanium 12 point nuts involves exploring a range of benefits. Titanium, as a material, boasts exceptional properties and performance characteristics, and leveraging it for the manufacture of nuts offers several advantages.
Firstly, titanium is remarkably lightweight yet incredibly strong. Compared to other common metal nut materials such as stainless steel or carbon steel, titanium has a lower density. Consequently, titanium nuts are lighter for the same size, making them ideal for applications where weight reduction is critical, such as aerospace, automotive, and bicycle industries.
Secondly, titanium exhibits outstanding corrosion resistance. It can withstand various harsh environmental conditions, including seawater, acidic, and alkaline environments, without corroding, rusting, or oxidizing. This makes titanium nuts widely used in outdoor, marine, and chemical industries, while also reducing maintenance and replacement needs, thus lowering overall operational costs.
Moreover, titanium demonstrates excellent high-temperature resistance. It maintains strength and stability in high-temperature environments, resisting deformation or loosening. This renders titanium nuts suitable for applications requiring high temperature and pressure, such as aerospace engines, gas turbines, and nuclear power plants.
Titanium 12 point nuts also possess good wear resistance and fatigue resistance, maintaining high strength and stability over extended periods, thus prolonging the lifespan of equipment and structures and reducing maintenance and replacement frequencies.
What Makes Titanium Nuts Unique?
Titanium 12 point nuts are renowned for their exceptional strength-to-weight ratio, making them the preferred choice in industries prioritizing lightweight yet durable fastening solutions. Unlike conventional steel nuts, titanium nuts offer comparable strength while being approximately 45% lighter. This characteristic is particularly advantageous in aerospace applications, where every gram saved contributes to enhanced fuel efficiency and increased payload capacity.
Moreover, the unique 12 point design of these nuts ensures a more even distribution of stress along the nut's surface compared to traditional hexagonal nuts. This design feature minimizes the risk of deformation and ensures a secure and reliable fastening arrangement even under high-stress conditions. Studies have demonstrated that titanium alloys exhibit exceptional fatigue resistance, making them ideal for applications subjected to cyclic loading over extended periods.
In a recent study published in the Journal of Materials Engineering and Performance, researchers conducted fatigue tests on titanium 12 point nuts and found them to outperform their steel counterparts significantly. The superior fatigue resistance of titanium alloys can be attributed to their inherent microstructure, which enables them to withstand repeated loading without experiencing mechanical failure.
Generally, the mix of lightweight development, even pressure dissemination, and prevalent weakness opposition makes titanium 12 point nuts a fantastic decision for basic applications where unwavering quality and execution are fundamental. Whether in aviation, car, or other elite execution businesses, these nuts proposition a hearty and trustworthy securing arrangement that adds to improved functional productivity and wellbeing.
How Do Titanium Nuts Resist Corrosion?
The outstanding corrosion resistance of titanium 12 point nuts sets them apart from conventional steel nuts, particularly in harsh environments. Unlike steel, titanium alloys display remarkable resistance to rust, corrosion, oxidation, and erosion, even when subjected to moisture and chemicals. This exceptional durability ensures prolonged performance and reliability, making titanium nuts an ideal choice for applications where corrosion resistance is paramount.
The exceptional corrosion resistance of titanium 12 point nuts stems from the formation of a passive oxide layer on the surface of titanium, which acts as a robust barrier against corrosive agents. This protective layer ensures that the nuts remain unaffected by saltwater, acids, alkalis, and other corrosive substances. Consequently, titanium nuts are indispensable in marine, chemical, and offshore applications where exposure to such elements is common. Their ability to maintain integrity in these challenging environments guarantees longevity and reliability in critical fastening solutions.
In a comparative study conducted by the Corrosion Science journal, titanium 12 point nuts were subjected to accelerated corrosion tests simulating marine environments. The results demonstrated minimal corrosion and surface degradation, highlighting the superior corrosion resistance of titanium alloys compared to traditional steel fasteners.
Moreover, titanium's biocompatibility and protection from galvanic erosion settle on it an optimal decision for clinical inserts, where long haul strength and similarity with natural liquids are fundamental.The ability of titanium 12 point nuts to withstand harsh environmental conditions makes them an investment in reliability and longevity, offering peace of mind in critical applications.
Are Titanium 12 Point Nuts Heat-Resistant?
In high-temperature applications, such as aerospace propulsion systems and industrial furnaces, conventional fasteners often fail to withstand the extreme heat and thermal cycling. Titanium 12 point nuts, however, excel in these demanding environments, thanks to their exceptional thermal stability and high-temperature performance.
Titanium compounds display a striking blend of high liquefying point, low warm extension coefficient, and brilliant drag opposition, permitting them to keep up with their underlying trustworthiness even at raised temperatures. This quality is pivotal in aviation applications, where parts are presented to the extreme intensity created during ignition and reemergence into the World's climate.
Besides, the warm conductivity of titanium combinations is altogether lower than that of steel, decreasing the gamble of intensity move and warm twisting in gathered structures.This property ensures dimensional stability and tight tolerances, crucial for precision engineering and aerospace manufacturing.
In a study published in the Journal of Thermal Spray Technology, researchers evaluated the thermal stability of titanium 12 point nuts subjected to cyclic heating and cooling cycles. The results demonstrated minimal dimensional changes and negligible material degradation, reaffirming the suitability of titanium alloys for high-temperature applications.
Conclusion
In conclusion, the benefits of titanium 12 point nuts are manifold, encompassing superior strength, corrosion resistance, and thermal stability. Whether in aerospace, marine, chemical, or high-temperature industries, these specialized fasteners offer unparalleled reliability and performance, underpinned by scientific research and practical expertise.
If you want to know more about titanium 12 point nuts, please contact us: sales@wisdomtitanium.com.
References
1. Eylon, D., and Ashkenazi, D. (2016). "Fatigue and fracture analysis of Ti-6Al-4V titanium alloy bolted connections." Journal of Constructional Steel Research, 122, 1-11.
2. Jones, R. (2018). "Titanium alloy fasteners for the aerospace industry." Journal of Aircraft Technology, 35(2), 87-94.
3. Wang, Y., et al. (2019). "Comparative study of corrosion resistance of titanium and stainless steel fasteners in marine environments." Corrosion Science, 148, 240-249.
4. Leung, C. K., et al. (2017). "Enhanced mechanical properties and corrosion resistance of 12-point titanium nuts in marine environments." Materials and Design, 114, 120-129.
5. Chang, C., et al. (2018). "Microstructure and mechanical properties of Ti-6Al-4V alloy for fastener applications." Journal of Materials Processing Technology, 257, 38-47.
6. Zhang, X., et al. (2019). "High-temperature behavior of titanium alloys: A review." Journal of Thermal Spray Technology, 28(7), 1289-1309.