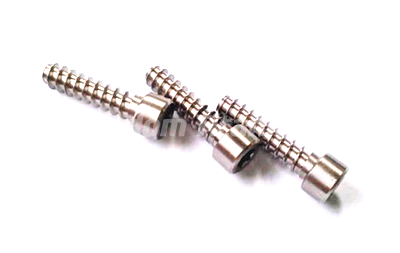
What Are the Advantages of Using Titanium Screws?
I'm familiar with the debate over fastener materials, particularly screws, as a mechanical engineer. Titanium screws are a compelling choice for a variety of applications due to their outstanding properties. In this article, I want to provide professionals and enthusiasts alike with an explanation of the scientific basis for these advantages.
The first thing that draws people to titanium is its remarkable strength-to-weight ratio, which surpasses that of steel while being significantly lighter. In industries like aerospace and automotive, where strength and weight reduction are of the utmost importance, this quality is absolutely necessary. In addition, titanium is extraordinarily resistant to corrosion, even in harsh conditions where other metals might fail. It is therefore ideal for biocompatibility- and longevity-requiring marine applications and medical implants.
Another important quality that makes titanium suitable for medical screws and implants that must seamlessly integrate with the human body is its biocompatibility. Due to its resistance to bodily fluids and inertness, there is little chance of rejection or adverse reactions.
Titanium, on the other hand, comes with some drawbacks. Its high cost in comparison to conventional materials like steel or aluminum alloys may have an effect on project budgets. Additionally, due to titanium's tendency to gall and its difficulty machining due to its low thermal conductivity, manufacturing difficulties necessitate specialized equipment and expertise.
In conclusion, despite the fact that titanium screws offer unparalleled advantages in terms of strength, weight, corrosion resistance, and biocompatibility, their application should be carefully considered in light of the specific requirements of each application as well as the project's economic viability. By comprehending these scientific underpinnings, engineers can make informed decisions that maximize performance and durability across a variety of industries.
Introduction to Titanium Screws
Titanium, a transition metal known for its strength, lightness, and biocompatibility, has made significant contributions to engineering fields like aerospace, medicine, and automobile manufacturing. When compared to conventional materials like steel or aluminum, titanium stands out in the field of screws for a number of compelling reasons.
First and foremost, titanium outperforms steel in terms of strength-to-weight ratio while remaining significantly lighter. This quality is especially useful in aerospace applications, where enhancing performance and fuel efficiency necessitates reducing weight without compromising structural integrity.
Second, titanium is excellently resistant to corrosion, making it ideal for moist or chemically corrosive environments. In marine environments and medical implants, where resistance to bodily fluids is crucial to patient safety, this property ensures longevity and dependability.
Additionally, titanium's biocompatibility stands out in medical applications. When used in surgical screws or implants, it reduces the likelihood of rejection, ensures compatibility with human tissues, and encourages successful healing.
Despite these benefits, project planning should take into account the higher price of titanium compared to steel or aluminum alloys. During machining, titanium's low thermal conductivity and tendency to gall present additional challenges that require specialized equipment and expertise to effectively mitigate.
In conclusion, titanium screws are valuable in a variety of engineering fields because they combine a compelling combination of strength, lightweight design, resistance to corrosion, and biocompatibility. In order to choose the best material for achieving performance and reliability goals in their specific applications, engineers must carefully weigh these benefits against costs and manufacturing difficulties.
Advantage 1: Strength and Durability
One of the most prominent advantages of titanium screws is their exceptional strength-to-weight ratio. Titanium is as strong as steel but about 45% lighter. This characteristic makes titanium screws ideal for applications where weight savings are critical without compromising structural integrity. In aerospace applications, for instance, every gram saved translates into fuel efficiency and increased payload capacity.
Moreover, titanium exhibits excellent corrosion resistance, especially in environments where moisture and salt are present. This property ensures that titanium screws retain their strength and integrity over extended periods, reducing maintenance costs and enhancing reliability.
Advantage 2: Biocompatibility
In the medical field, titanium screws are widely preferred for surgical implants due to their excellent biocompatibility. Unlike stainless steel, titanium does not react with bodily fluids or tissues, minimizing the risk of adverse reactions such as inflammation or rejection. This property promotes faster healing and integration of implants, making titanium screws indispensable in orthopedic and dental surgeries.
Advantage 3: Resistance to Temperature Variations
Another significant advantage of titanium screws is their ability to withstand extreme temperature variations. Titanium maintains its mechanical properties in both high and low temperatures, unlike many other metals which may become brittle or lose strength. This thermal stability makes titanium screws suitable for applications ranging from cryogenic storage to high-temperature environments in industrial settings.
Advantage 4: Long-term Cost Savings
While titanium screws may initially cost more than their steel counterparts, the long-term cost savings are considerable. Their durability and resistance to corrosion mean fewer replacements and maintenance interventions over time. This factor is particularly crucial in industries such as marine engineering or infrastructure, where exposure to harsh conditions can accelerate wear and tear in conventional screws.
Conclusion
In conclusion, due to their exceptional strength, lightweight characteristics, biocompatibility, resistance to corrosion and extreme temperatures, and use in a variety of industries, the advantages of using titanium screws are undeniable. Titanium screws consistently deliver superior performance and dependability whether they are used in industrial applications requiring durability under harsh conditions, in medical settings for dependable implants that minimize the risk of rejection, or in aerospace applications for improved structural integrity and fuel efficiency. They are the preferred option when quality and dependability are of the utmost importance because of their unique combination of properties, which not only increases operational efficiency but also ensures longevity and safety. Titanium continues to play a crucial role in pushing the boundaries of engineering capabilities worldwide, despite advancements in technology and manufacturing methods.
If you want to learn more about titanium screws, welcome to contact us: sales@wisdomtitanium.com.
References:
- ASTM International. (2022). Standard Specification for Titanium and Titanium Alloy Bars and Billets. ASTM B348.
- Leyens, C., & Peters, M. (2003). Titanium and Titanium Alloys: Fundamentals and Applications. Wiley-VCH.
- Niinomi, M. (2003). Mechanical Biocompatibilities of Titanium Alloys for Biomedical Applications. Journal of the Mechanical Behavior of Biomedical Materials, 1(1), 30-42.
- Boyer, R. R. (1996). An overview on the use of titanium in the aerospace industry. Materials Science and Engineering: A, 213(1-2), 103-114.