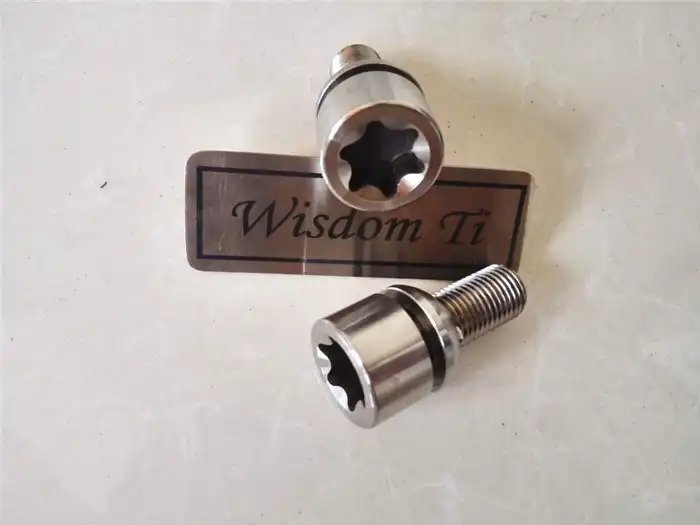
when considering the vital components of a car, mclaren titanium wheel bolts often don't receive the attention they deserve. Despite their seemingly minor role, they are critical to the safety and performance of a vehicle. In this article, I delve into the materials used to manufacture car wheel bolts, exploring their properties, advantages, and why they are chosen for this specific application.
Importance of Car Wheel Bolts
Vehicle wheel bolts might seem like subtle parts, yet they assume a pivotal part in vehicle security and execution. These little clasp are answerable for tying down the wheels to the vehicle's hub center, guaranteeing they remain immovably joined notwithstanding the powers and vibrations experienced during driving. The strength, sturdiness, and dependability of wheel bolts are directly influenced by the materials they are made of, as well as the design and manufacturing processes for them.
Vehicle wheel bolts are basic parts in guaranteeing the security and unwavering quality of vehicles. These seemingly insignificant fasteners are essential for securing the wheels to the axle hub and preserving the wheel assembly's integrity. Wheel bolts help prevent accidents caused by loose or improperly secured wheels by securely fastening the wheels. Their significance stretches out past simple securing; They also help the performance of the vehicle by keeping the wheels in the right alignment and balance, which has a direct impact on handling and stability.
Mclaren titanium wheel bolts are intended to endure critical powers and vibrations experienced during vehicle activity, underlining their job in guaranteeing a smooth and safe driving experience. In addition, their durability and capacity to withstand a variety of environmental conditions, including corrosion resistance in a variety of climates, are crucially dependent on their materials, manufacturing processes, and adherence to stringent quality standards. Subsequently, vehicle wheel bolts epitomize the crossing point of designing accuracy, wellbeing norms, and execution in auto plan.
Materials Used in Car Wheel Bolts
Wheel bolts are typically made from high-strength materials capable of withstanding substantial loads and stresses. The most common materials used include:
Medium Carbon Steel: This type of steel offers a good balance of strength and cost-effectiveness. It's widely used in automotive applications where reliability and affordability are key considerations.
Alloy Steels: These steels contain additional alloying elements such as chromium and molybdenum, which enhance their strength and hardness. Alloy steels are preferred for applications requiring higher tensile strength and resistance to wear.
Austenitic Stainless Steel: Known for its corrosion resistance and durability, austenitic stainless steel is often used in wheel bolts exposed to moisture and corrosive environments.
Duplex Stainless Steel: Offers a combination of strength and corrosion resistance, making it suitable for more demanding applications where both properties are critical.
In high-performance and racing vehicles, titanium alloys are sometimes used for wheel bolts due to their exceptional strength-to-weight ratio. They help reduce unsprung weight, improving vehicle handling and acceleration.
Manufacturing Processes
the manufacturing of mclaren titanium wheel bolts involves several crucial steps to ensure their strength and reliability:
Forging: Many wheel bolts are forged rather than machined from solid material. Forging improves the mechanical properties of the material by aligning the grain structure and enhancing its strength.
Heat Treatment: After forging, wheel bolts undergo heat treatment processes such as quenching and tempering. These processes optimize the material's hardness, toughness, and resistance to fatigue and deformation under load.
Machining and Finishing: Following heat treatment, wheel bolts are machined to precise specifications. This includes threading the bolt shaft to ensure proper engagement with the wheel hub and attaching a washer or cap as needed.
Design Considerations
The design of wheel bolts is critical to their performance and reliability:
Thread Design: The thread profile must be carefully engineered to provide secure fastening and resist loosening due to vibrations and dynamic loads experienced during vehicle operation.
Length and Diameter: Wheel bolts are designed to provide sufficient clamping force without compromising the integrity of the bolt or the wheel hub. These dimensions are carefully calculated based on vehicle specifications and engineering standards.
Testing and Quality Control
Manufacturers adhere to rigorous testing and quality control measures to ensure wheel bolts meet safety and performance standards:
Torque Specifications: Each vehicle model specifies torque values for wheel bolts to ensure proper clamping force. Over-tightening can lead to stress concentration and potential failure, while under-tightening may result in loose wheels.
Durability Testing: Wheel bolts undergo testing to evaluate their fatigue strength, corrosion resistance, and overall durability under simulated real-world conditions.
Environmental and Regulatory Considerations
Corrosion Resistance: given their exposure to environmental elements such as moisture, road salts, and chemicals, mclaren titanium wheel bolts are often coated or treated to enhance their corrosion resistance.
Regulatory Standards: Wheel bolts must meet stringent regulatory standards set by organizations such as the Department of Transportation (DOT) or international equivalents. These standards ensure the bolts are safe and reliable for use in vehicles.
Conclusion
Vehicle wheel bolts are fundamental parts that guarantee the wellbeing and dependability of vehicles out and about. From their material structure to assembling processes, plan contemplations, and adherence to administrative principles, each part of wheel bolt creation is pointed toward improving execution and strength. Materials and processes used to manufacture these essential components will also change in tandem with automotive technology to ensure that they meet the increasingly stringent requirements of contemporary automobiles.
The decision of material is essential, as it straightforwardly influences the bolt's capacity to endure critical powers and vibrations experienced during vehicle activity, consequently guaranteeing protected and dependable wheel connection. Mclaren titanium wheel bolts that meet exacting standards for safety and performance in automotive engineering are produced by manufacturers using stringent quality control measures and rigorous manufacturing processes like forging, heat treatment, and precision machining.