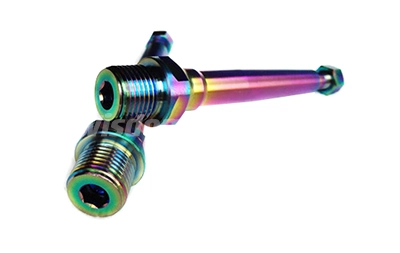
In the realm of cutting-edge cycling technology, titanium pedal spindles stand out as a testament to exceptional engineering and groundbreaking material innovation. These seemingly small yet indispensable components play a vital role as the direct link between the cyclist and the bicycle, showcasing a harmonious blend of meticulous scientific design, mechanical ingenuity, and peak performance enhancement. More than just functional connectors, titanium spindles embody the fusion of advanced technology and craftsmanship, offering a glimpse into the extraordinary possibilities unlocked by modern materials science and precision engineering. Their design and functionality exemplify how even the smallest components can profoundly impact the cycling experience, enhancing efficiency, durability, and overall performance.
Material: Grade 5 Titanium Alloy
Grade 5 titanium alloy, scientifically designated as Ti-6Al-4V, stands as the quintessential material in high-performance cycling components. This extraordinary alloy represents a sophisticated metallurgical achievement, carefully engineered to deliver unparalleled performance characteristics that far surpass traditional materials used in bicycle manufacturing.
The molecular architecture of Grade 5 titanium reveals a complex crystalline structure that endows the material with extraordinary mechanical properties. Its composition of 90% titanium, complemented by 6% aluminum and 4% vanadium, creates a unique metallurgical profile that balances strength, lightweight characteristics, and remarkable durability. The alloy's alpha-beta phase structure provides exceptional mechanical performance, with tensile strengths ranging from 880 to 1,170 MPa—a testament to its superior engineering capabilities.
Comparative studies have demonstrated that Grade 5 titanium outperforms traditional materials across multiple critical parameters. Its specific strength-to-weight ratio is approximately 2.5 times higher than that of standard steel alloys, making it an ideal choice for precision cycling components. The material's inherent corrosion resistance ensures longevity, with minimal degradation even under extreme environmental conditions such as saltwater exposure, high humidity, or temperature variations.
Length: Customizable
The concept of titanium pedal spindle length transcends simple dimensional specifications, representing a nuanced intersection of biomechanical engineering, ergonomic design, and individual cyclist physiology. Modern bicycle fitting has evolved into a sophisticated science that recognizes the critical importance of precise spindle dimensions in optimizing cycling performance and preventing potential physiological strain.
Customizable spindle lengths typically range from 50mm to 65mm, but this range represents more than mere numerical variation. Each millimeter can significantly impact a cyclist's biomechanical efficiency, power transfer, and overall riding comfort. Professional bike fitters employ advanced motion capture technologies, pressure mapping systems, and three-dimensional body scanning to determine the most appropriate spindle length for individual athletes.
Different cycling disciplines demand distinct spindle length strategies. Mountain bike riders might require slightly longer spindles to enhance stability and accommodate wider pedal stance, while road cyclists often prefer marginally shorter spindles to optimize aerodynamic positioning and minimize lateral movement. The customization process involves complex calculations considering factors such as hip width, leg length, pedaling dynamics, and intended cycling discipline.
Diameter: Standard Sizes Available
The diameter of titanium pedal spindles represents a critical engineering parameter that ensures optimal performance, compatibility, and mechanical efficiency. While seemingly straightforward, spindle diameter involves sophisticated considerations of mechanical tolerances, interface dynamics, and precision manufacturing techniques.
Standard diameters ranging from 9mm to 15mm are not arbitrary measurements but the result of extensive research and development in cycling component design. The 9mm and 12mm diameters have emerged as industry standards, reflecting a delicate balance between structural integrity, weight reduction, and compatibility with existing cycling infrastructure. These dimensions are meticulously calculated to minimize friction, maximize power transfer, and ensure seamless integration with various pedal and crank systems.
Precision manufacturing techniques enable extraordinarily tight tolerances, typically within ±0.02mm. This microscopic precision ensures consistent performance across different environmental conditions and cycling applications. Advanced computer numerical control (CNC) machining, combined with sophisticated metrology techniques, allows manufacturers to achieve these exceptional dimensional accuracies.
Weight: Lightweight Design
Weight reduction in cycling components represents a sophisticated engineering challenge that extends far beyond simple mass minimization. Titanium pedal spindles exemplify this principle, offering an unprecedented combination of lightweight design and exceptional structural performance that challenges traditional material engineering paradigms.
A typical titanium pedal spindle weighs between 40-50 grams, representing a significant weight reduction compared to traditional steel alternatives. However, this weight savings is not achieved through material compromise but through advanced metallurgical design. The remarkable strength-to-weight ratio of Grade 5 titanium allows for substantial mass reduction without sacrificing structural integrity or mechanical performance.
The implications of this lightweight design extend beyond mere numerical specifications. Reduced rotational mass translates directly into improved cycling efficiency, reducing energy expenditure and enhancing overall performance. Professional cyclists and biomechanical researchers have demonstrated that even minimal weight reductions can yield measurable improvements in energy conservation, particularly during long-distance or endurance cycling events.
Titanium Pedal Spindle Manufacturer
Choosing a titanium pedal spindle manufacturer is a nuanced and critical decision that demands a thorough assessment of technical expertise, production capabilities, and a steadfast dedication to quality engineering. Leading manufacturers in this field differentiate themselves through an integrated approach that combines cutting-edge research, precision craftsmanship, and a relentless pursuit of innovation.
Among these industry leaders, Wisdom Titanium stands out as a beacon of excellence in the specialized domain of titanium components. Their methodology transcends traditional manufacturing practices, incorporating advanced metallurgical research, state-of-the-art engineering, and a profound understanding of cycling biomechanics. This unique approach ensures that their titanium spindles not only meet but often exceed the expectations of cyclists and manufacturers alike.
Wisdom Titanium also emphasizes accessibility and value by offering competitive pricing and maintaining a robust inventory, enabling seamless supply chains for high-performance cycling components. Their unwavering commitment to quality is evident in every stage of their production process, from meticulous quality control protocols and full material traceability to the continuous adoption of innovative technologies.
For those seeking unparalleled titanium solutions tailored to specific cycling needs, Wisdom Titanium invites inquiries and consultations. Their team of technical experts is ready to assist with personalized recommendations and detailed insights. Connect with them today at sales@wisdomtitanium.com to discover the future of high-performance cycling technology.
References
[1] Boyer, R. R. "An Overview on the Use of Titanium in the Aerospace Industry." Materials Science and Engineering: A, vol. 213, no. 1-2, 1996, pp. 103-114.
[2] Lütjering, G., and J. C. Williams. "Titanium: Microstructure and Properties." Engineering Materials and Processes, Springer, 2007.
[3] Donachie, Matthew J. "Titanium: A Technical Guide." ASM International, 2000.
[4] International Titanium Association. "Technical Resources on Titanium Alloys." Titanium Applications Report, 2019.
[5] Williams, J. C., and E. H. Froes. "Titanium Science and Technology." Springer, 2015.