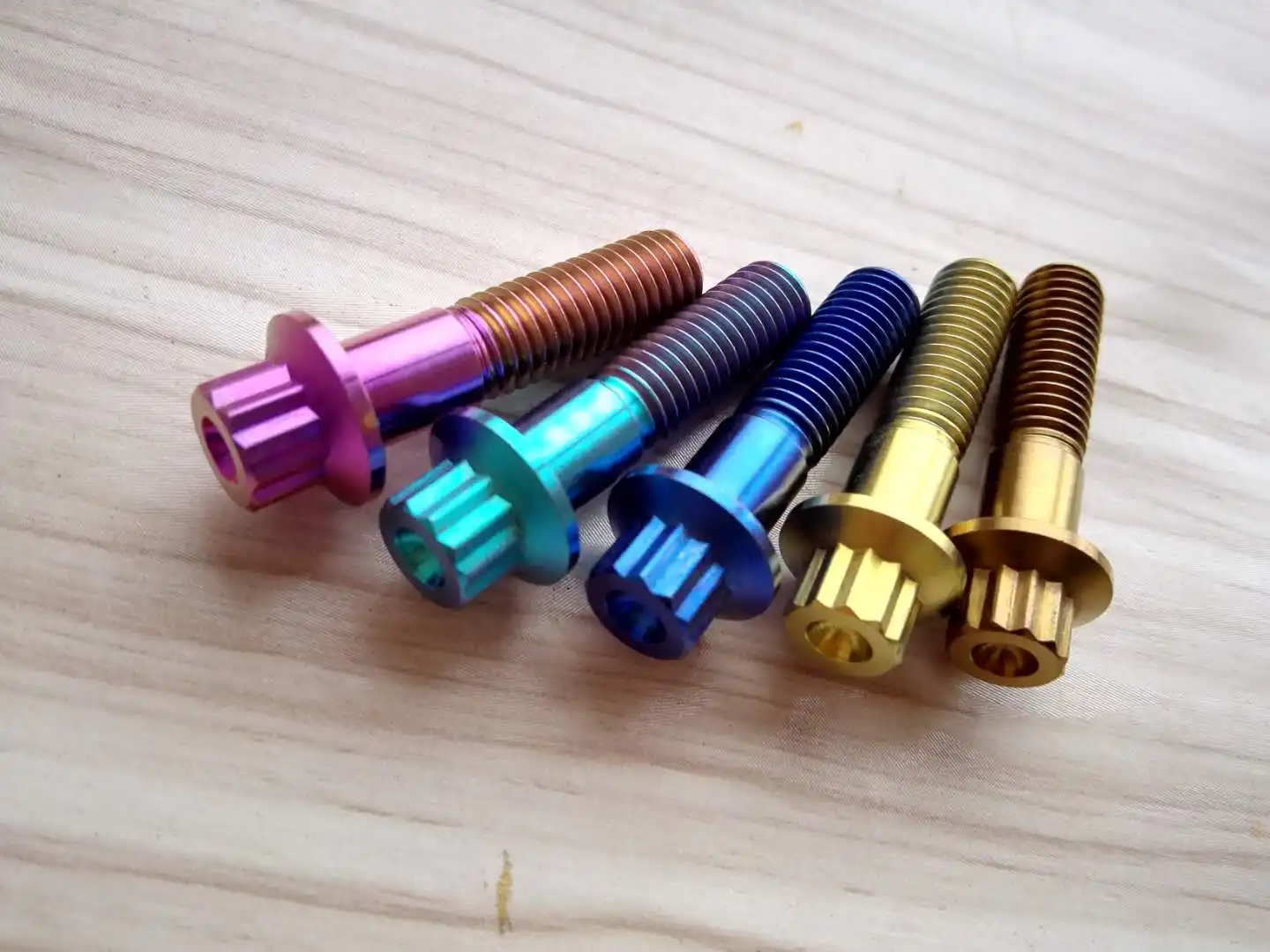
As a materials engineer specializing in fasteners, I've often been asked about the strength and durability of Titanium 12 Point Flange Bolts. Titanium is eminent for its remarkable solidarity to-weight proportion and erosion opposition, yet does this turn out as expected for flange bolts produced using this material? In this article, we'll dig into the science behind titanium flange bolts, investigating their solidarity, sturdiness, and appropriateness for different applications.
Understanding Titanium's Strength Properties
To comprehend the strength of titanium flange bolts, it's essential to first understand the inherent properties of titanium as a material. Titanium is a transition metal known for its remarkable strength, comparable to steel but with only around half the density. This unique combination of strength and low density makes titanium an ideal choice for applications where weight reduction is crucial without sacrificing structural integrity.
One of the key elements adding to titanium's solidarity is its high rigidity to-thickness proportion. Elasticity alludes to the greatest pressure a material can endure without disappointment under strain. Titanium shows an amazing rigidity, making it fit for enduring significant burdens without twisting or breaking. Moreover, titanium keeps up with its solidarity at raised temperatures, further improving its reasonableness for elite execution applications.
Furthermore, titanium possesses excellent fatigue resistance, allowing it to withstand repeated loading cycles without failure. This property is particularly advantageous in applications where cyclic loading is prevalent, such as aerospace components and racing vehicles. The fatigue strength of Titanium 12 Point Flange Bolts ensures reliable performance and longevity under demanding operating conditions.
Titanium is a remarkable metal renowned for its exceptional strength properties, making it a preferred choice in various industrial applications. To comprehend the intricacies of titanium's strength, one must delve into its atomic structure and material behavior.
At the atomic level, titanium exhibits a unique arrangement of atoms, characterized by its strong metallic bonds. These bonds result from the sharing of electrons between adjacent atoms, contributing to titanium's inherent strength. Additionally, titanium possesses a hexagonal close-packed (HCP) crystal structure, which further enhances its mechanical properties.
One crucial aspect influencing titanium's strength is its purity level. High-purity titanium, devoid of impurities and alloying elements, demonstrates superior strength characteristics compared to its alloyed counterparts. This purity ensures minimal distortion of the crystal lattice, allowing for efficient load transfer and resistance to deformation.
Furthermore, titanium's strength is heavily influenced by its processing methods. Techniques such as cold working, hot working, and heat treatment impart distinct microstructural changes, thereby affecting its mechanical behavior. Cold working, for instance, induces dislocation density within the crystal structure, enhancing strength through grain refinement and strain hardening mechanisms.
The temperature also plays a vital role in determining titanium's strength properties. While titanium exhibits excellent strength at room temperature, its mechanical behavior undergoes alterations under extreme conditions. Elevated temperatures can lead to significant reductions in strength due to thermal softening effects, whereas cryogenic temperatures can enhance its strength and toughness.
Moreover, the presence of alloying elements can significantly alter titanium's strength properties. Common alloying elements such as aluminum, vanadium, and nickel can enhance specific attributes like corrosion resistance, while also influencing mechanical properties such as tensile strength, yield strength, and ductility.
The Role of Flange Design in Bolt Strength
When it comes to evaluating the strength of titanium flange bolts, the design of the flange plays a critical role. Flanges are integral components of bolted joints, providing a larger load-bearing surface area and distributing the applied load more evenly across the joint. The design of the flange influences factors such as bolt preload, clamping force, and resistance to loosening under cyclic loading.
In the case of titanium flange bolts, the flange design is optimized to maximize the contact area between the bolt head or nut and the mating surface. This increased contact area enhances the distribution of forces, reducing the risk of bolt fatigue and failure. Additionally, flange bolts are often used in applications requiring high levels of vibration resistance, such as automotive and industrial machinery.
Moreover, the use of a 12-point flange design offers several advantages over traditional hexagonal flanges. A 12-point flange provides multiple contact points between the bolt head or nut and the wrench, allowing for higher torque transmission and reduced risk of stripping or rounding off the bolt head. This design feature enhances the overall reliability and durability of Titanium 12 Point Flange Bolts in critical applications.
The integrity and efficacy of bolted joints in engineering structures are heavily reliant on various factors, among which flange design plays a pivotal role. Flanges, the protruding rims or edges on either side of a structural component, serve multifaceted functions in bolted connections, ranging from load distribution to alignment maintenance. A well-considered flange design not only enhances the overall strength of the bolted joint but also mitigates the risk of premature failure and ensures longevity.
One of the primary functions of flanges is to distribute the applied load evenly across the joint interface. Through careful design considerations such as the thickness, shape, and surface finish of the flanges, engineers can optimize the stress distribution within the joint, thereby minimizing stress concentrations that could lead to bolt fatigue or fracture. Moreover, by incorporating features such as serrations or grooves on the flange surfaces, engineers can enhance the interfacial friction between mating components, thereby reducing the propensity for slippage or loosening under cyclic loading conditions.
Furthermore, flange design influences the preload and clamping force exerted on the bolt during assembly, which are critical determinants of joint integrity. By manipulating parameters such as flange thickness, diameter, and geometry, engineers can tailor the bolt preload to achieve the desired level of joint compression, ensuring sufficient frictional resistance to external loads and minimizing the risk of bolt relaxation or self-loosening over time.
Additionally, the geometric configuration of flanges plays a crucial role in facilitating proper bolt alignment and installation. Flanges with well-defined mating surfaces and alignment features enable accurate positioning of bolts, thereby reducing the likelihood of misalignment-induced stress concentrations or uneven load distribution. Moreover, innovative flange designs incorporating self-aligning mechanisms or pre-tensioning features can streamline the assembly process while enhancing joint reliability and repeatability.
Applications and Considerations for Titanium Flange Bolts
Titanium flange bolts find widespread use in a variety of industries and applications where lightweight, high-strength fastening solutions are required. From aerospace and marine engineering to automotive and racing, Titanium 12 Point Flange Bolts offer unmatched performance and reliability. Their corrosion resistance makes them particularly well-suited for marine environments, where exposure to saltwater can degrade traditional fasteners over time.
In aerospace applications, where every gram of weight matters, titanium flange bolts are indispensable for securing critical components while minimizing overall weight. Their high strength-to-weight ratio and fatigue resistance make them ideal for aerospace structures subjected to extreme forces and temperature variations. Additionally, the biocompatibility of titanium makes it suitable for medical implants, where strength, corrosion resistance, and compatibility with the human body are paramount.
However, it's essential to consider the cost implications of using titanium flange bolts, as titanium is significantly more expensive than traditional materials such as steel or aluminum. While the initial investment may be higher, the long-term benefits of reduced maintenance, extended service life, and improved performance often justify the expense, especially in high-value applications where reliability is non-negotiable.
Conclusion
In conclusion, titanium flange bolts offer exceptional strength, durability, and corrosion resistance, making them a preferred choice for demanding applications across various industries. Their unique combination of properties, including high tensile strength, fatigue resistance, and lightweight design, makes them an invaluable asset in aerospace, automotive, marine, and medical applications. By understanding the science behind titanium's strength properties and the role of flange design in bolt performance, engineers and designers can confidently specify titanium flange bolts for critical fastening applications.
If you want to know more about Titanium 12 Point Flange Bolts, please contact us: sales@wisdomtitanium.com.