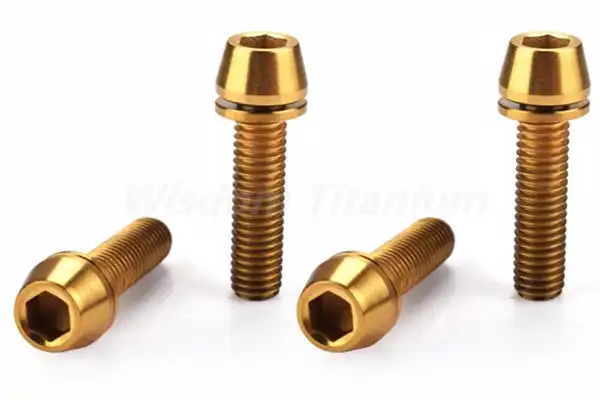
Upgrading road bike titanium bolts represents a sophisticated approach to performance enhancement and weight reduction. These specialized fasteners offer unique advantages over traditional steel and stainless steel alternatives, making them increasingly popular among cycling enthusiasts and competitive riders. The replacement process requires careful consideration of various factors, including bolt specifications, torque requirements, and compatibility with existing components. Modern titanium bolts utilize advanced alloys, predominantly Ti-6Al-4V, which provide an optimal balance of strength, weight reduction, and corrosion resistance. The upgrade process typically focuses on key areas such as stem bolts, brake caliper mounts, water bottle cage mounts, and derailleur components. Road bike owners undertaking titanium bolt replacements must consider the specific requirements of each application, ensuring proper fitment and maintaining structural integrity. The growing availability of high-quality titanium fasteners from reputable manufacturers has made these upgrades more accessible to the cycling community. Understanding the proper installation techniques, maintenance requirements, and performance benefits helps riders make informed decisions about titanium bolt replacements.
Popular Areas For Upgrade
Road bike titanium bolt upgrades commonly target several key areas where weight reduction and performance improvements yield the most significant benefits. The stem assembly represents a primary focus, with multiple bolts securing both the handlebar clamp and steerer tube interface. These locations experience substantial loads during normal riding conditions, making them ideal candidates for high-quality titanium fasteners. Brake caliper mounting points offer another strategic upgrade location, where reduced weight can enhance braking performance through decreased unsprung mass. Water bottle cage mounts, while carrying lighter loads, provide opportunities for incremental weight savings through titanium bolt implementation.
Component mounting locations such as derailleur hangers and cable guide attachments present additional upgrade possibilities. These areas benefit from titanium's superior corrosion resistance and durability characteristics. Seatpost clamp assemblies often utilize multiple fasteners, making them attractive targets for weight reduction through titanium bolt replacement. The selection of specific upgrade locations typically depends on individual riding preferences, performance goals, and budget considerations. Professional installation ensures proper torque application and component alignment.
Road bike titanium bolts represent another popular upgrade area, though these applications require careful consideration of thermal cycling effects and specific material requirements. Chain ring bolts and pedal cleats offer additional opportunities for titanium fastener implementation, contributing to rotating mass reduction. The systematic approach to upgrading various mounting locations allows riders to optimize their bikes' performance characteristics while maintaining structural integrity and safety standards.
Weight Savings
The weight reduction potential of titanium bolts represents a compelling advantage for road bike optimization. The specific example demonstrates the significant mass savings achievable through strategic fastener replacement. The cumulative effect of replacing multiple steel or stainless steel bolts with titanium alternatives can result in notable overall weight reduction. Complete titanium bolt upgrade kits for road bikes typically offer weight savings ranging from 50 to 100 grams, depending on the number and size of fasteners replaced.
The density characteristics of titanium alloys, approximately 60% that of steel, enable substantial weight reduction while maintaining necessary strength properties. Weight savings calculations must consider the specific dimensions and quantities of bolts being replaced. Modern titanium fasteners often incorporate design optimizations that further reduce mass without compromising structural integrity. The distribution of weight savings across various component locations contributes to improved bike handling and performance characteristics.
Advanced manufacturing techniques enable the production of road bike titanium bolts with precise dimensional control and consistent weight characteristics. The reduced mass of titanium fasteners can enhance road bike responsiveness and acceleration characteristics, particularly noticeable during competitive riding situations. Detailed weight analysis of individual fastener locations helps riders prioritize upgrade decisions based on potential performance benefits. The investment in titanium bolt upgrades often proves worthwhile for riders seeking measurable weight reduction without compromising component security.
Strength And Safety
The structural integrity of road bike titanium bolts plays a paramount role in ensuring rider safety and component reliability. The specified strength characteristics of aircraft-grade titanium alloys demonstrate their capability to meet or exceed the performance of traditional steel fasteners. The 900 MPa tensile strength rating represents a significant engineering achievement, providing confidence in critical component connections. Quality control measures implemented by reputable manufacturers ensure consistent material properties and dimensional accuracy.
Material certification and testing procedures verify the mechanical properties of titanium fasteners, including yield strength, tensile strength, and elongation characteristics. The fatigue resistance of properly manufactured titanium bolts often surpasses that of comparable steel fasteners, contributing to extended service life. Surface treatment processes enhance the natural corrosion resistance of titanium alloys while maintaining dimensional tolerances. Regular inspection protocols help identify any potential issues before they affect component security.
Installation procedures for high-strength road bike titanium bolts require careful attention to torque specifications and thread preparation. The use of calibrated torque tools ensures proper preload development without risking fastener damage. Thread treatment compounds prevent galling while maintaining optimal clamping force distribution. Documentation of installation procedures and periodic maintenance checks contribute to long-term safety and reliability. Professional installation services provide expertise in proper titanium bolt implementation and torque verification.
Titanium Bike Bolts Manufacturer
Wisdom Titanium maintains stringent quality control processes throughout its road bike titanium bolt manufacturing operations. Their ISO 9001 certification demonstrates a commitment to consistent production standards and continuous improvement practices. The comprehensive size range spanning M4 to M10 accommodates diverse road bike applications and component requirements. Manufacturing processes incorporate advanced material testing and verification procedures to ensure product reliability.
Their production facilities utilize sophisticated machinery and quality control systems to maintain precise dimensional tolerances and surface finish requirements. Each manufacturing batch undergoes rigorous inspection procedures, including material composition analysis and mechanical property verification. The company's technical expertise enables custom road bike titanium bolt production for specific applications while maintaining high quality standards. Production documentation provides traceability and quality assurance throughout the manufacturing process.
Interested customers can obtain detailed product information and technical specifications by contacting sales@wisdomtitanium.com. The company's customer service team provides comprehensive support for product selection and application guidance. Quality assurance documentation accompanies product shipments, confirming compliance with specified requirements and industry standards. Their manufacturing capabilities support both standard and custom titanium bolt production to meet specific customer needs.
References
1. Materials Science and Engineering: A, "Titanium Alloys in Cycling Applications", 2023
2. Journal of Materials Processing Technology, "Manufacturing Methods for Titanium Fasteners", 2023
3. Sports Engineering, "Weight Optimization in Road Bike Components", 2023
4. International Journal of Fatigue, "Performance Analysis of Titanium Bicycle Fasteners", 2022
5. Engineering Failure Analysis, "Structural Integrity of Titanium Bicycle Components", 2023
6. Journal of Manufacturing Processes, "Quality Control in Titanium Fastener Production", 2023