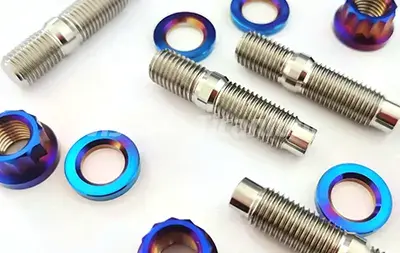
Titanium exhuast bolts have gained popularity in high-performance automotive applications due to their excellent strength-to-weight ratio, corrosion resistance, and ability to withstand high temperatures. However, to ensure these bolts meet the demanding requirements of exhaust systems, rigorous performance testing is essential. This article will explore the various testing methods used to evaluate titanium exhaust bolts, focusing on tensile testing, fatigue testing, and corrosion testing. Understanding these testing procedures can help automotive enthusiasts and professionals make informed decisions when selecting titanium fasteners for their exhaust systems.
Tensile Testing
Tensile testing is a fundamental method used to determine the strength and ductility of titanium exhuast bolts. This test involves applying a gradually increasing axial load to a bolt until it fails. The results provide crucial information about the bolt's mechanical properties, including its yield strength, ultimate tensile strength, and elongation. A typical tensile test for titanium exhaust bolts follows the ASTM F606 standard, which outlines the procedures for testing externally threaded fasteners.
During the test, the bolt is secured in a universal testing machine, and force is applied at a controlled rate. The machine measures the applied force and the bolt's elongation throughout the test. From this data, a stress-strain curve is generated, which provides valuable insights into the bolt's behavior under load.
Key parameters evaluated in tensile testing of titanium exhaust bolts include:
1. Yield strength: This is the stress at which the bolt begins to deform plastically. For titanium alloys commonly used in exhaust bolts, such as Grade 5 (Ti-6Al-4V), the yield strength is typically around 830-924 MPa.
2. Ultimate tensile strength: This is the maximum stress the bolt can withstand before failing. Grade 5 titanium bolts usually have an ultimate tensile strength of about 900-993 MPa.
3. Elongation: This measures the bolt's ductility, or ability to deform without breaking. Titanium exhaust bolts should exhibit sufficient elongation (typically 10-15% for Grade 5) to allow for some plastic deformation before failure, which can help prevent sudden, catastrophic failures.
The results of tensile testing are crucial for ensuring that titanium exhaust bolts can withstand the forces they'll encounter in real-world applications. These tests also help manufacturers optimize their production processes and quality control measures.
Fatigue Testing
While tensile testing provides valuable information about a bolt's static strength, fatigue testing is essential for evaluating how titanium exhuast bolts perform under repeated loading cycles. This is particularly important for exhaust system applications, where bolts are subjected to continuous vibrations and thermal cycling. The ASTM E466 standard often guides these tests, providing procedures for conducting force-controlled fatigue tests of metallic materials.
There are several key aspects of fatigue testing for titanium exhaust bolts:
1. Stress amplitude: This is the varying stress applied to the bolt during each cycle. For exhaust applications, the stress amplitude is often set to simulate the forces experienced during engine operation and thermal expansion/contraction.
2. Mean stress: This is the average stress applied during the test. In exhaust applications, bolts are typically under a constant tensile load (preload) in addition to the cyclic stresses.
3. Frequency: The rate at which load cycles are applied. This is often set to match the vibration frequencies typically encountered in automotive applications, which can range from a few Hz to several hundred Hz.
The results of fatigue testing are typically presented as an S-N curve (stress vs. number of cycles to failure), also known as a Wöhler curve. This curve helps engineers determine the fatigue limit or endurance limit of the titanium bolts, which is the stress level below which the bolt can theoretically withstand an infinite number of cycles without failing.
Titanium alloys, particularly those used in exhaust bolts, generally exhibit excellent fatigue resistance. Grade 5 titanium, for example, typically has a fatigue strength of about 510 MPa at 10^7 cycles. This high fatigue strength, combined with titanium's low density, makes it an excellent choice for exhaust system fasteners.
Corrosion Testing
Corrosion resistance is one of the key advantages of titanium in exhaust system applications. However, it's still crucial to conduct thorough corrosion testing to ensure that titanium exhuast bolts can withstand the harsh chemical environment they'll encounter in service. Several standardized corrosion tests are commonly used for titanium exhaust bolts:
1. Salt Spray Test (ASTM B117): This test exposes the bolts to a salt fog atmosphere, simulating a marine or road salt environment. While titanium is highly resistant to chloride attack, this test can reveal any potential weak points in the bolt's design or manufacturing process.
2. Cyclic Corrosion Testing (ASTM G85): This test combines various environmental factors, including salt spray, high humidity, and dry conditions in a cyclic manner. It provides a more realistic simulation of real-world conditions than the constant salt spray test.
3. Exhaust Condensate Test: This specialized test exposes bolts to a synthetic exhaust condensate solution, which mimics the corrosive environment inside an exhaust system. The solution typically contains a mixture of sulfuric acid, nitric acid, and chlorides.
During these tests, bolts are periodically inspected for signs of corrosion, such as pitting, crevice corrosion, or stress corrosion cracking. Weight loss measurements and tensile testing of exposed bolts can provide quantitative data on the extent of corrosion and its impact on mechanical properties.
Titanium's excellent corrosion resistance stems from its ability to form a stable, protective oxide layer (primarily TiO2) on its surface. This layer quickly reforms if damaged, providing continuous protection. In corrosion tests, titanium exhaust bolts typically show minimal weight loss and maintain their mechanical properties, even after extended exposure to corrosive environments.
Titanium Exhuast Bolts For Sale
For those in the market for high-quality titanium exhuast bolts that have undergone rigorous performance testing, Wisdom Titanium offers a range of options. Their main sizes for titanium exhaust manifold stud kits include M8x1.25x45mm and M10x1.25x45mm, which are common sizes for many vehicle applications.
Wisdom Titanium's commitment to quality and performance is reflected in their rigorous testing procedures. Their titanium exhaust bolts undergo tensile testing to verify strength and ductility, fatigue testing to ensure long-term durability under cyclic loading, and corrosion testing to confirm resistance to harsh exhaust environments.
If you're in the process of choosing a titanium exhaust bolt manufacturer, you can contact Wisdom Titanium at sales@wisdomtitanium.com for more information about their products and testing procedures. They can provide detailed specifications and test results to help you make an informed decision.
References
1. ASTM International. (2016). ASTM F606/F606M-16 Standard Test Methods for Determining the Mechanical Properties of Externally and Internally Threaded Fasteners, Washers, and Rivets.
2. ASTM International. (2015). ASTM E466-15 Standard Practice for Conducting Force Controlled Constant Amplitude Axial Fatigue Tests of Metallic Materials.
3. ASTM International. (2019). ASTM B117-19 Standard Practice for Operating Salt Spray (Fog) Apparatus.
4. ASTM International. (2019). ASTM G85-19 Standard Practice for Modified Salt Spray (Fog) Testing.
5. Peters, M., Kumpfert, J., Ward, C. H., & Leyens, C. (2003). Titanium Alloys for Aerospace Applications. Advanced Engineering Materials, 5(6), 419-427.