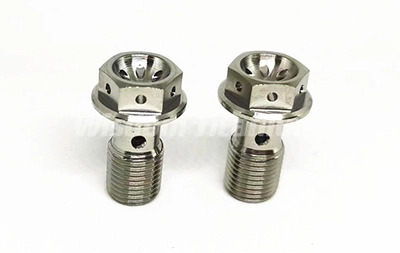
Titanium banjo bolts stand out as crucial parts in a variety of high-performance applications in the field of precision engineering. These specialty fasteners are essential to fluid transfer systems in a variety of industries because of their strength, portability, and resistance to corrosion. We'll examine every stage of the intriguing titanium banjo bolt production process today, from raw material to final product.
Material Preparation And Pretreatment
The meticulous selection and preparation of the raw material is the first step in the creation of a titanium banjo bolt. Because of its remarkable strength-to-weight ratio and durability, Grade 5 titanium alloy (Ti-6Al-4V) is typically used by manufacturers. This alloy is perfect for high-stress applications because of its remarkable tensile strength, which ranges from 900 to 1050 MPa (130,000 to 152,000 psi).
The material preparation process involves several crucial steps:
- Purchasing Materials: Reputable vendors offer premium titanium alloy in the shape of bars or rods.
- Inspection: To make sure it satisfies the necessary requirements, every batch of raw materials is subjected to stringent quality checks.
- Cutting: To enable machining, the titanium stock is divided into smaller pieces, usually a little longer than the finished bolt length.
- Heat Treatment: Depending on the specific requirements, the titanium may undergo heat treatment to optimize its mechanical properties.
This painstaking preparation procedure is essential in laying the groundwork for the subsequent precision machining, guaranteeing that every titanium banjo bolt starts with the best possible start. Prior to being precisely cut and shaped to the necessary specifications, the raw titanium material must first be carefully chosen and inspected. From dimensional accuracy to surface smoothness, every detail is carefully examined to prevent any flaws that might jeopardize the finished product. This meticulous preparation reduces the possibility of mistakes during the machining process, enabling more reliable outcomes. Each bolt is assured to be uniform in quality with an emphasis on strict standards and high tolerances, guaranteeing optimal performance in its intended application.
Machining: Where Precision Meets Performance
The machining step is crucial to the production of titanium banjo bolts. Here, the complex shape that characterizes a banjo bolt is formed from raw titanium. To attain the highest level of accuracy and consistency, modern manufacturers use cutting-edge CNC (Computer Numerical Control) equipment.
The machining process typically involves these key steps:
- Turning: The bolt's outer diameter has the proper shape and dimensions.
- Drilling: To give the bolt its distinctive banjo-like shape that permits fluid passage, precise holes are drilled through it.
- Milling: The bolt body is milled to include extra features like flats or hex heads.
- Threading: The threads are rolled onto the bolt or carefully cut. Because of their exceptional strength and resistance to fatigue, rolled threads are used by many premium manufacturers, such as Wisdom Titanium.
To guarantee that each titanium banjo bolt is machined to precise specifications, computer-controlled equipment—in particular, CNC (Computer Numerical Control) machines—is essential. By precisely controlling the cutting, shaping, and finishing procedures, CNC technology makes sure that every bolt satisfies the necessary tolerances. Beyond accuracy, CNC machines make it possible to create intricate geometries that would be difficult, if not impossible, to accomplish using conventional manual machining techniques. These devices can accurately and consistently reproduce complex designs, lowering the possibility of human error and speeding up production. CNC technology guarantees the flexibility and scalability required to satisfy the demands of contemporary manufacturing by rapidly adapting to various designs and specifications, and producing dependable, high-quality components.
Post-Processing And Quality Control: Ensuring Excellence
After the primary machining is complete, titanium banjo bolts undergo several post-processing steps to refine their performance and appearance:
- Deburring: To guarantee smooth operation and guard against possible harm to mating components, any sharp edges or burrs left over from machining are carefully removed.
- Surface Finishing: To improve their look and resistance to corrosion, the bolts may be polished, anodized, or coated, depending on the application.
- Cleaning: The bolts are prepared for final inspection and packaging by thoroughly cleaning them to get rid of any remaining machining oils or debris.
For titanium banjo bolts to be produced, quality control is crucial. To confirm its dimensions, thread quality, and general compliance with specifications, every bolt is subjected to a thorough inspection. This could consist of:
Visual examination for flaws on the surface
Dimensional checks with instruments for precise measurement
Testing with a thread gauge to guarantee correct fit and operation
Testing the tensile strength of bolt samples from every production batch
Numerous top producers, like Wisdom Titanium, uphold ISO 9001 certification, indicating their dedication to constant quality and client satisfaction. This certification guarantees adherence to globally accepted quality management standards at every stage of the manufacturing process, from material selection to final inspection.
Wisdom Titanium: Craftsmanship Meets Innovation
The combination of cutting-edge technology and expert craftsmanship is demonstrated by the production process of titanium banjo bolts. Every stage, from the rigorous quality control and precise CNC machining to the careful selection of Grade 5 titanium alloy, helps to create a component with exceptional performance and dependability.
Titanium banjo bolts continue to be at the forefront of engineering solutions as industries continue to demand components that are stronger, lighter, and more durable. Knowing the complex process that goes into making these specialty fasteners can help you recognize their value and make wise choices for your projects, whether you work in the automotive, aerospace, or any other industry that needs high-performance fluid transfer systems.
Manufacturers like Wisdom Titanium provide experience supported by ISO 9001 certification and cutting-edge production capabilities for individuals looking for premium titanium banjo bolts. Their 200-piece minimum order quantity (MOQ) allows them to accommodate both small- and large-scale orders. Please contact their sales team at sales@wisdomtitanium.com to learn more about how their titanium banjo bolts can improve your upcoming project.
The secret to advancing your engineering solutions to new levels of dependability and performance may lie in embracing the accuracy and potential of titanium banjo bolts.
References
1. ASM International. (2015). Titanium and Titanium Alloys: Fundamentals and Applications.
2.Lutjering, G., & Williams, J. C. (2007). Titanium (Engineering Materials and Processes).
3.Budynas, R. G., & Nisbett, J. K. (2020). Shigley's Mechanical Engineering Design.
4. International Organization for Standardization. (2015). ISO 9001:2015 Quality management systems — Requirements.