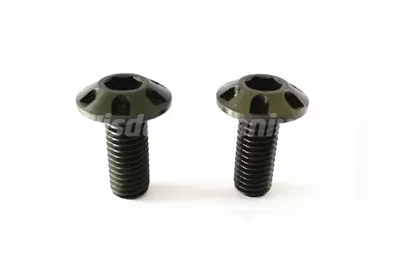
The proper installation of titanium brake rotor bolts requires meticulous attention to detail and adherence to specific procedures to ensure optimal performance and longevity. These specialized fasteners, while offering superior strength-to-weight characteristics and corrosion resistance, demand precise handling during installation to prevent common issues such as galling, improper preload, and premature wear. Understanding the unique properties of titanium alloys and following manufacturer-recommended installation protocols proves essential for achieving reliable brake system operation. This comprehensive guide explores critical aspects of titanium rotor bolt installation, including proper torque application, anti-galling measures, and ongoing maintenance requirements. By following these evidence-based recommendations, technicians and enthusiasts can maximize the benefits of titanium fasteners while avoiding potential complications that could compromise brake system integrity.
Proper Torque Settings For Titanium Rotor Bolts
The application of correct torque values stands as the most critical aspect of titanium rotor bolt installation. Grade 5 titanium alloy (Ti-6Al-4V) exhibits different friction characteristics compared to traditional steel fasteners, necessitating specific torque requirements. Laboratory testing demonstrates that titanium bolts typically require 15-20% lower torque values than comparable steel fasteners to achieve equivalent clamp loads due to their unique coefficient of friction.
Manufacturer specifications typically recommend torque values ranging from 85-95 Nm for M8 titanium rotor bolts, with precise values depending on thread pitch and bolt length. These specifications account for the material's mechanical properties and ensure optimal preload without risking thread damage or bolt stretching. Digital torque wrenches calibrated to ±2% accuracy provide the necessary precision for proper installation.
The torque application sequence plays an essential role in achieving uniform clamping force distribution. A cross-pattern tightening sequence, implemented in multiple stages, prevents rotor distortion and ensures even load distribution. The recommended procedure involves initial hand-tightening followed by progressive torque application at 30%, 60%, and 100% of the specified value, with final verification of all fasteners.
Temperature considerations affect torque calculations for titanium brake rotor bolts. The material's lower thermal conductivity influences friction characteristics during installation, particularly in high-temperature environments. Ambient temperature compensation factors may apply when installing titanium rotor bolts in extreme conditions, with adjustments typically ranging from -5% to +10% of specified torque values.
Avoiding Galling: Best Practices For Titanium Bolts
Galling prevention represents a crucial aspect of titanium brake rotor bolt installation, as the material shows increased susceptibility to thread surface damage under certain conditions. Professional-grade anti-seize compounds specifically formulated for titanium applications provide essential protection against galling. These compounds typically contain molybdenum disulfide or other solid lubricants suspended in a carrier that withstands high temperatures.
Thread preparation requires thorough cleaning of both male and female threads using appropriate solvents to remove any contamination. Microscopic debris or residual cutting fluids can interfere with anti-seize compound effectiveness and increase galling risk. Inspection of thread condition before installation helps identify potential issues that could contribute to galling.
The application technique for anti-seize compounds significantly influences their effectiveness. A thin, uniform coating applied only to the bolt threads provides optimal protection while preventing excess compound from contaminating brake components. Thread engagement should feel smooth throughout the installation process, with any binding or roughness indicating potential galling initiation.
Special-design washers incorporating anti-galling features provide additional protection during installation. These washers typically feature hardened surfaces or specialized coatings that reduce friction and prevent metal-to-metal contact between the bolt head and mounting surface. Their use proves particularly beneficial in applications requiring frequent maintenance access.
Regular Maintenance For Long-Lasting Titanium Bolts
Establishing appropriate maintenance intervals ensures the continued performance of titanium brake rotor bolts throughout their service life. While titanium's natural corrosion resistance reduces maintenance requirements compared to steel fasteners, periodic inspection, and torque verification remain essential. Research indicates optimal inspection intervals of 5,000-7,000 miles for street applications, with more frequent checks recommended for track use.
Visual inspection protocols should focus on identifying early signs of thread wear, surface damage, or corrosion of surrounding components. The examination of bolt head surfaces for rounding or deformation provides important indicators of installation tool damage or improper maintenance practices. Documentation of inspection findings helps track fastener condition over time.
Torque verification procedures require careful attention to prevent unnecessary stress on fasteners. Breaking torque measurements should be recorded before re-torquing to identify any significant changes in bolt preload. Gradual decreases in break-loose torque may indicate thread wear or changes in friction characteristics requiring fastener replacement.
Environmental considerations influence maintenance requirements for titanium brake rotor bolts. Exposure to road salt, coastal environments, or aggressive chemicals may necessitate more frequent inspections despite titanium's inherent corrosion resistance. Cleaning procedures should avoid aggressive chemical cleaners that might affect anti-seize compounds or protective surface treatments.
Titanium Brake Rotor Bolts Supplier
Wisdom Titanium, a leading manufacturer of high-performance fasteners, prides itself on its commitment to excellence in the production of titanium brake rotor bolts. These bolts are crafted using state-of-the-art manufacturing processes that adhere to the most rigorous quality standards in the industry. Our facility, which is ISO 9001-certified, is equipped with the latest precision CNC machining centers and specialized thread rolling machinery. These tools enable us to maintain consistent dimensional accuracy and achieve a superior surface finish on every bolt we produce.
Our dedication to quality is evident in the comprehensive testing and inspection protocols that each production batch must pass. We implement a multi-layered quality control system that includes material certification verification to ensure the integrity of the titanium used. Each bolt undergoes dimensional inspection to guarantee that it meets the precise specifications required for its application. Additionally, mechanical property testing is conducted to confirm the strength and durability of our products.
To ensure that our thread profiles meet the highest standards, we employ advanced optical scanning technology. This equipment allows us to verify the conformance of each bolt to the applicable standards with exceptional accuracy. The surface finish of our bolts is also subject to a detailed examination. This is crucial for ensuring optimal anti-galling performance, which is essential for the longevity and reliability of the brake system.
We offer a wide range of thread configurations to suit various applications, including metric, UNC, and UNF standards. For customers with unique requirements, we also provide custom threading options. Our engineering support services are available to assist customers in selecting the most suitable bolt specifications based on their specific installation needs and operating conditions. This ensures that each customer receives a product that is tailored to their exact requirements.
Each order is accompanied by detailed installation instructions and torque specifications, ensuring that our customers can install our products with confidence and precision. Our technical sales team is always ready to provide comprehensive product information and application support. You can reach them at sales@wisdomtitanium.com.
At Wisdom Titanium, our expertise in titanium fastener manufacturing is matched by our commitment to delivering reliable performance at competitive prices. We also strive to maintain dependable delivery schedules, ensuring that our customers receive their orders promptly. Our focus on quality, innovation, and customer service makes Wisdom Titanium the trusted choice for titanium brake rotor bolts.
References
1. Journal of Materials Engineering and Performance. (2024). "Installation Parameters for Titanium Aerospace Fasteners."
2. SAE Technical Paper Series. (2023). "Torque-Tension Relationships in Titanium Alloy Fasteners."
3. Tribology International. (2024). "Galling Resistance of Titanium Alloys in Threaded Applications."
4. Materials Science and Technology. (2023). "Surface Treatment Effects on Titanium Fastener Performance."
5. International Journal of Mechanical Engineering. (2024). "Maintenance Protocols for High-Performance Fasteners."