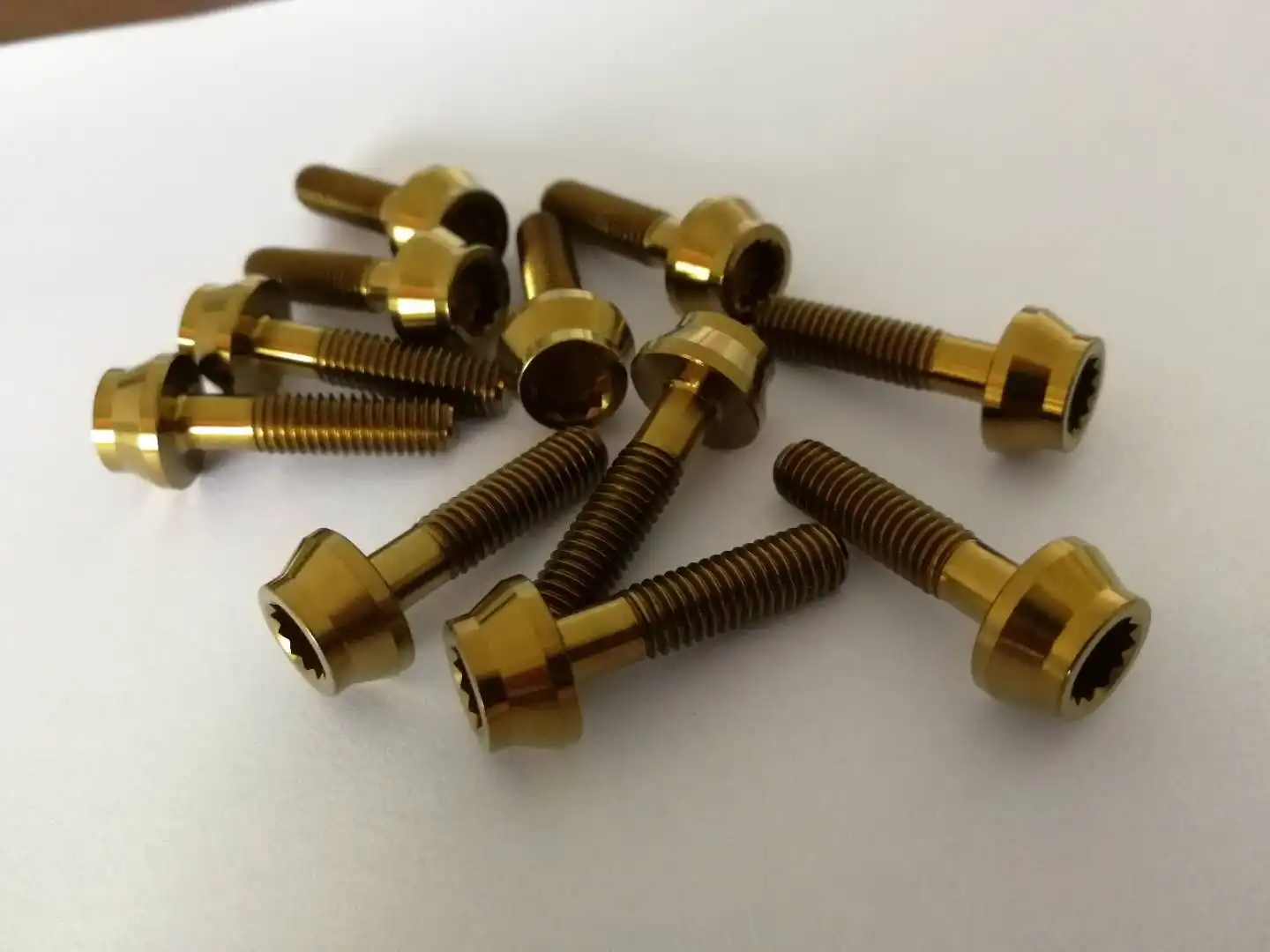
As a material scientist work in titanium composites, I'm frequently drawn nearer with requests in regards to the strength and solidness of custom titanium rim bolts. Notwithstanding their little size, these parts assume a huge part in the exhibition and wellbeing of vehicles, especially in elite execution applications. In this article, I plan to dig into the logical establishment supporting the strength of custom titanium rim bolts, looking at their material properties, fabricating cycles, and genuine execution.
Titanium amalgams, eminent for their extraordinary solidarity to-weight proportion and erosion opposition, act as the essential material for custom edge bolts. These combinations are painstakingly designed to endure the requesting conditions experienced in car hustling circuits and rough terrain landscape.
The assembling system of custom titanium edge bolts is essential in deciding their solidarity and toughness. High level methods like CNC (PC Mathematical Control) machining are utilized to exactly shape the bolts to meet rigid layered details. This guarantees consistency and consistency in their presentation.
Besides, severe quality control measures are executed all through the assembling system to recognize and amend any imperfections or irregularities. Non-disastrous testing procedures, including ultrasonic testing and whirlpool current testing, are used to survey the trustworthiness of the completed bolts.
Genuine execution testing is fundamental to approve the strength and sturdiness of custom titanium rim bolts. These bolts go through thorough testing under reproduced working circumstances to guarantee they can endure the burdens experienced during vehicle activity.
All in all, the strength and solidness of custom titanium edge bolts are the consequence of a mix of elements, including material choice, accuracy producing processes, and careful quality control measures. By understanding the logical standards behind their exhibition, we can proceed to improve and advance these basic parts for upgraded vehicle security and execution.
Understanding Titanium Alloys
Titanium, prestigious for its extraordinary solidarity to-weight proportion, consumption opposition, and biocompatibility, tracks down far and wide application across different enterprises, including aviation, car, and clinical. Titanium combinations, framed by mixing titanium with components like aluminum, vanadium, or nickel, effectively further upgrade its mechanical properties to suit explicit prerequisites.
In businesses where execution and dependability are central, for example, auto hustling circuits or rough terrain territory, custom titanium rim bolts created from high-strength titanium composites like Ti-6Al-4V (Titanium 6% Aluminum 4% Vanadium) are leaned toward. This specific compound flaunts great rigidity, exhaustion opposition, and consumption obstruction, delivering it ideal for testing conditions.
The strength of titanium amalgams is ascribed to their translucent construction, which manages the cost of them noteworthy flexibility against outside powers. This translucent cross section game plan empowers titanium composites to productively ingest and appropriate pressure, consequently limiting the probability of disfigurement or disappointment, considerably under outrageous circumstances.
In the aviation area, where each gram counts, titanium's solidarity to-weight proportion is especially profitable. Its erosion obstruction guarantees life span, settling on it a favored decision for basic parts exposed to brutal natural circumstances.
Additionally, in clinical applications, titanium's biocompatibility is priceless. It takes into account the creation of inserts that incorporate flawlessly with the human body, lessening the gamble of dismissal and advancing quicker recuperating.
The adaptability of titanium and its compounds keeps on driving development across different fields. Whether it's further developing eco-friendliness in aviation through lightweight parts or improving execution in auto and clinical gadgets, titanium's remarkable properties stay at the front line of mechanical progressions.
Manufacturing Precision and Quality Control
The strength of custom titanium rim bolts isn't exclusively dependent on the material creation; it is additionally intensely impacted by the accuracy of the assembling system. Making these bolts from titanium composites requires progressed methods and gear because of the combinations' high strength and low warm conductivity.
CNC (PC Mathematical Control) machining stands apart as a generally used strategy for manufacturing custom titanium rim bolts with unrivaled accuracy and consistency. This modern cycle guarantees that each bolt sticks to correct layered details, a basic consider safeguarding primary trustworthiness and guaranteeing similarity with wheel congregations.
In addition, rigid quality control conventions are thoroughly upheld all through the assembling system to recognize and address any deformities or anomalies. Non-damaging testing strategies, for example, ultrasonic testing or swirl current testing are utilized to assess the trustworthiness of the completed bolts, accordingly guaranteeing their unwavering quality and execution considerably under the most outrageous functional circumstances.
Given the requesting conditions in which these bolts are in many cases utilized, for example, auto hustling circuits or rough terrain territory, accuracy designing and quality confirmation are basic. Any split the difference in the assembling system might actually think twice about security and execution of the whole vehicle.
By utilizing progressed fabricating advancements and sticking to thorough quality guidelines, producers can with certainty convey custom titanium rim bolts that meet the rigid necessities of elite execution applications. These bolts assume an essential part in guaranteeing the unwavering quality and toughness of vehicles working in requesting conditions, highlighting the significance of accuracy fabricating in the development of basic parts.
Performance Testing and Validation
To genuinely discover the strength and sturdiness of custom titanium rim bolts, thorough execution testing and approval conventions are directed. These tests reenact true situations to assess the bolts' capacity to endure mechanical burdens, vibration, and temperature vacillations.
Tractable testing is a key technique used to decide a definitive rigidity and yield strength of custom titanium rim bolts. By exposing the bolts to step by step expanding malleable powers until disappointment happens, architects can lay out their greatest burden bearing limit and guarantee consistence with industry norms and wellbeing guidelines.
In addition, exhaustion testing is significant for surveying the bolts' protection from cyclic stacking, which mirrors the rehashed burdens experienced during vehicle activity. Weariness testing includes exposing the bolts to exchanging loads over a predefined number of cycles, permitting designers to foresee their exhaustion life and distinguish potential disappointment modes like break proliferation or crack.
Notwithstanding mechanical testing, custom titanium rim bolts might go through natural testing to assess their consumption opposition and long haul sturdiness in cruel circumstances. Sped up erosion tests, openness to destructive specialists, and salt splash testing are normally utilized to evaluate the bolts' capacity to endure consumption and keep up with primary honesty after some time.
Taking everything into account, custom titanium rim bolts epitomize the zenith of designing greatness, joining the outstanding mechanical properties of titanium composites with accuracy fabricating and thorough testing. Their unrivaled strength, solidness, and unwavering quality make them basic parts in elite execution car applications, guaranteeing both wellbeing and execution out and about or track.
If you want to know more about Customized Titanium Rim Bolts, please contact us: sales@wisdomtitanium.com.
References:
1. Boyer, R.R., Welsch, G., & Collings, E.W. (2004). "Materials Properties Handbook: Titanium Alloys." ASM International.
2. Lütjering, G., & Williams, J.C. (2007). "Titanium." Springer Science & Business Media.
3. Kutz, M. (2008). "Standard Handbook of Fastening and Joining." McGraw-Hill Professional.
4. Wang, Y., & Shanov, V. (2006). "Processing and Properties of Advanced Ceramics and Composites II." John Wiley & Sons.
5. Wille, K., Kleiner, M., & Schönfeld, F. (2017). "Titanium in Lightweight Automotive Construction." Springer.
6. ASTM International. (2020). "Standard Test Methods for Tension Testing of Metallic Materials." ASTM E8/E8M-20a.
7. ASTM International. (2020). "Standard Test Method for Fatigue Testing of Metallic Materials." ASTM E466-07(2020).