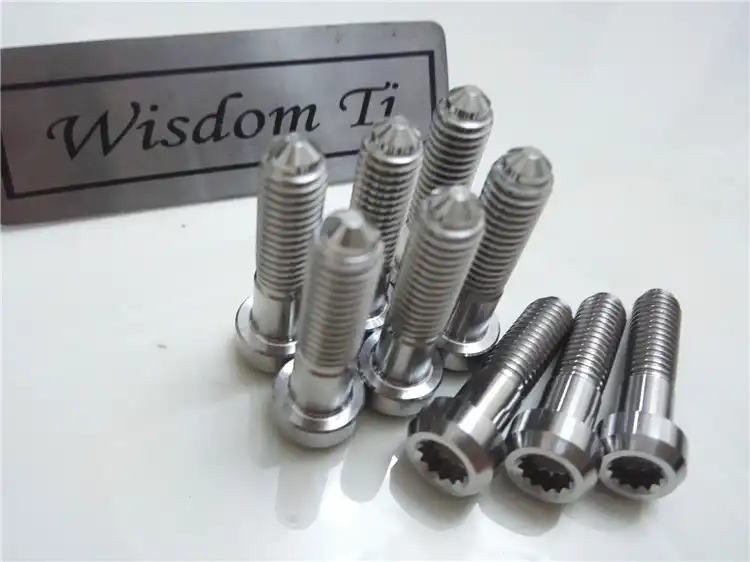
As an automotive enthusiast and someone deeply involved in the racing community, I've always been fascinated by the materials that make up crucial components of high-performance vehicles. One such component that often gets overlooked but plays a critical role is the wheel fastener. In recent years, titanium has gained popularity as a material choice for these fasteners due to its exceptional strength-to-weight ratio and corrosion resistance. But just how durable are titanium wheel fastener? Let's delve into the science behind their durability and performance.
Understanding Titanium's Strengths and Properties
Titanium is well-known for its remarkable strength, which is comparable to that of steel but is roughly half as heavy. This property alone makes it a positive material for applications where weight reserve funds are essential, like in aviation and elite execution auto businesses. Titanium amalgams utilized in latches are ordinarily Grade 5 titanium, otherwise called Ti-6Al-4V, which comprises of titanium, aluminum, and vanadium. This alloy is ideal for wheel fasteners subjected to high stress and demanding conditions due to its balance of strength, lightness, and durability.
Titanium wheel fastener's remarkable strength-to-weight ratio is one of its most distinctive characteristics. In spite of being around 50% of the thickness of steel, titanium combinations like Grade 5 (Ti-6Al-4V) display rigid qualities equivalent to certain prepares. This high strength makes titanium especially worthwhile in applications where weight decrease is basic without forfeiting mechanical execution. For instance, titanium's strength enables lighter aircraft structures, resulting in improved fuel efficiency and performance in the aerospace industry.
Durability Under Extreme Conditions: Heat, Corrosion, and Fatigue
One of the primary concerns with wheel fasteners is their ability to withstand extreme conditions without compromising safety or performance. Titanium exhibits excellent heat resistance, maintaining its mechanical properties at elevated temperatures that would weaken or deform other metals. This characteristic is particularly critical in racing applications where brakes can generate intense heat.Titanium alloys, especially those like Ti-6Al-4V, can withstand temperatures up to 600°C (1112°F) without significant loss of strength. This thermal stability is crucial in applications such as jet engines, spacecraft, and high-performance automotive components, where materials are routinely exposed to intense heat. Unlike some metals that become brittle or lose integrity at high temperatures, titanium maintains its robustness, ensuring reliable performance and longevity in demanding thermal conditions.
Corrosion resistance is another significant advantage of titanium wheel fastener. Unlike steel, titanium does not rust or corrode easily, even when exposed to moisture and road salts. This corrosion resistance ensures longevity and reliability, crucial for maintaining wheel security over time.Titanium’s natural resistance to corrosion significantly enhances its durability in harsh environments. The metal forms a thin but extremely stable oxide layer on its surface when exposed to oxygen. This layer protects against various corrosive agents, including seawater, chlorine, and acidic compounds. Consequently, titanium is extensively used in marine applications, chemical processing plants, and medical implants. In marine environments, for instance, titanium resists saltwater corrosion far better than stainless steel, ensuring longer service life and reduced maintenance. In medical applications, its resistance to bodily fluids prevents degradation, making it ideal for long-term implants.
Furthermore, titanium alloys have excellent fatigue resistance, which is the ability to withstand cyclic loading without failure. This property is essential in wheels subjected to constant vibrations and stress during operation. Titanium's fatigue strength is comparable to that of steel, ensuring that the fasteners can endure prolonged use without succumbing to fatigue-induced failure.The metal forms a thin but extremely stable oxide layer on its surface when exposed to oxygen. This layer protects against various corrosive agents, including seawater, chlorine, and acidic compounds. Consequently, titanium is extensively used in marine applications, chemical processing plants, and medical implants. In marine environments, for instance, titanium resists saltwater corrosion far better than stainless steel, ensuring longer service life and reduced maintenance. In medical applications, its resistance to bodily fluids prevents degradation, making it ideal for long-term implants.
Performance in Lightweighting and Efficiency
The automotive industry is increasingly focused on lightweighting to enhance fuel efficiency and overall performance. Titanium wheel fastener contribute to this goal by reducing the overall weight of the vehicle without compromising strength or safety. Every gram saved in rotating mass, such as wheels and fasteners, translates to improved acceleration, handling, and braking performance, especially in high-speed and competitive racing environments.
Lightweight materials improve overall vehicle dynamics and performance metrics. In automotive applications, reduced weight leads to better handling, agility, and acceleration. Vehicles equipped with lighter components can achieve higher speeds more efficiently and handle corners with greater stability. In aerospace, lightweight materials contribute to increased payload capacity, longer flight ranges, and improved maneuverability of aircraft.
Lightweighting also aligns with sustainability goals by reducing the environmental impact of transportation and manufacturing. Vehicles with lower fuel consumption emit fewer greenhouse gases and pollutants, contributing to cleaner air and reduced carbon footprint. Additionally, the use of lightweight materials often involves efficient manufacturing processes that minimize waste and energy consumption, further enhancing sustainability across the supply chain.
Despite their reduced weight, advanced lightweight materials maintain high levels of structural integrity and safety. Materials like carbon fiber composites and titanium offer exceptional strength-to-weight ratios, ensuring robust performance under various operational conditions. This reliability is critical in ensuring passenger safety in automotive and aerospace applications.
Lightweight materials enable designers to explore new possibilities in product design and innovation. They allow for more streamlined and aerodynamic vehicle shapes in automotive design, reducing drag and improving efficiency further. In aerospace, lightweight materials facilitate the design of aircraft with novel configurations that optimize fuel consumption and performance metrics.
Conclusion
In conclusion, performance-oriented vehicles benefit greatly from the lightweighting, strength, and durability that titanium wheel fasteners provide in a compelling combination. They are safe and reliable because they can withstand extreme conditions like heat, corrosion, and fatigue. It represent a significant advancement in material technology, and they can be used by professional racers, automotive engineers, or enthusiasts who want to improve vehicle performance.
To get more familiar with titanium wheel latches, welcome to reach us: sales@wisdomtitanium.com.