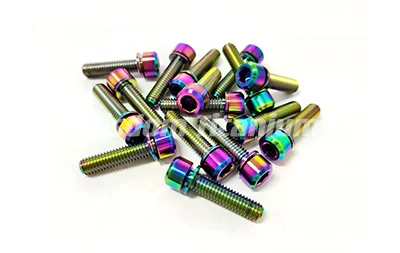
Titanium bike bolts demonstrate exceptional durability characteristics that make them ideal for cycling applications. These specialized fasteners, typically manufactured from Ti-6Al-4V alloy, exhibit remarkable longevity under diverse riding conditions and environmental exposures. The durability of titanium bolts stems from their unique material properties, including high tensile strength, superior fatigue resistance, and natural corrosion protection. Modern manufacturing processes ensure consistent quality and performance, with properly installed titanium bolts often outlasting the bicycle components they secure. The durability encompasses multiple aspects, including mechanical strength, wear resistance, and environmental stability. Research indicates that quality titanium bolts maintain their structural integrity and performance characteristics throughout extended service periods, with minimal degradation under normal use conditions. The combination of material properties and precise manufacturing controls results in fasteners that provide reliable service while offering significant weight advantages over traditional steel alternatives. Understanding the factors contributing to titanium bolt durability helps cyclists make informed decisions about component upgrades and maintenance schedules.
High Strength-To-weight Ratio
The impressive strength-to-weight ratio of titanium bike bolts represents a defining characteristic of their durability profile. Modern titanium alloys used in bicycle components achieve tensile strengths exceeding 900 MPa while maintaining a density approximately 40% lower than steel alternatives. This remarkable combination enables the design of lightweight fasteners that meet or exceed the structural requirements of demanding cycling applications. The specific strength advantages become particularly evident in critical component connections where both weight reduction and mechanical integrity are essential.
Advanced manufacturing techniques optimize the microstructure of titanium bike bolts, enhancing their mechanical properties while maintaining minimal mass. The crystalline structure of properly processed titanium alloys contributes to their ability to withstand substantial loads without permanent deformation. Material testing protocols verify the strength characteristics of each production batch, ensuring consistent performance across all bolt sizes and applications. The relationship between applied loads and material response demonstrates the superior efficiency of titanium in managing mechanical stresses.
The strength-to-weight advantages extend beyond static loading conditions, influencing dynamic performance during riding. The reduced mass of titanium fasteners contributes to improved component response while maintaining necessary clamping forces. Engineering analyses confirm the capacity of titanium bolts to handle peak loads encountered during aggressive riding conditions. The optimization of bolt designs leverages the material's inherent strength characteristics while minimizing unnecessary mass.
Excellent Fatigue Life
The fatigue resistance of titanium bike bolts significantly contributes to their long-term durability. Cycling components experience repeated loading cycles throughout their service life, making fatigue performance a critical consideration. The atomic structure and grain boundaries of titanium alloys resist the formation and propagation of fatigue cracks, enabling extended service periods under cyclic loading conditions. Laboratory testing demonstrates superior fatigue life compared to conventional steel fasteners, with some titanium bolts exceeding 10 million loading cycles without failure.
The relationship between applied stress levels and fatigue life follows established materials science principles, with titanium exhibiting favorable characteristics in the high-cycle regime. Proper heat treatment processes optimize the material's resistance to fatigue damage accumulation. The endurance limit of quality titanium bolts typically exceeds the normal operating stress ranges encountered in bicycle applications. Regular inspection protocols help identify any early indicators of fatigue-related concerns, though such issues rarely occur with properly manufactured and installed titanium fasteners.
Environmental factors play minimal roles in affecting the fatigue performance of titanium bike bolts, unlike steel alternatives that may experience corrosion-assisted fatigue. The stability of titanium's mechanical properties across varying temperature ranges contributes to consistent fatigue resistance. Manufacturing quality control measures ensure uniform material properties that support predictable fatigue behavior. Documentation of fatigue testing results provides confidence in long-term performance capabilities.
Highly Resistant To Corrosion
The exceptional corrosion resistance of titanium bike bolts represents a significant durability advantage. The formation of a stable oxide layer on titanium surfaces provides natural protection against environmental degradation. This passive film develops spontaneously upon exposure to oxygen and demonstrates remarkable stability across diverse environmental conditions. The protective characteristics prevent the deterioration commonly observed in steel fasteners, maintaining both structural integrity and aesthetic appearance throughout extended service periods.
Chemical stability testing confirms titanium's resistance to various corrosive environments encountered in cycling applications. The protective oxide layer maintains its effectiveness even when exposed to road salt, cleaning chemicals, and atmospheric pollutants. Surface treatment processes can enhance the natural corrosion resistance while maintaining dimensional accuracy and mechanical properties. The absence of galvanic corrosion concerns when paired with aluminum components represents another practical advantage.
Environmental exposure testing demonstrates the long-term stability of titanium bike bolts under various climate conditions. The resistance to pitting corrosion and stress corrosion cracking ensures reliable performance in demanding applications. Quality control measures verify the consistency of surface protection across production batches. The combination of inherent material properties and controlled manufacturing processes results in fasteners that maintain their protective characteristics throughout their service life.
Titanium Bike Bolts Manufacturer
Wisdom Titanium demonstrates comprehensive capabilities in producing high-quality titanium bike bolts. Their ISO 9001 certification reflects a commitment to maintaining consistent manufacturing standards and quality control processes. The available size range from M4 to M10 accommodates diverse bicycle component applications while maintaining precise dimensional control. Manufacturing documentation ensures traceability and quality verification throughout the production process.
The production facility incorporates advanced machining and inspection equipment to maintain tight tolerances and surface finish requirements. Titanium bike bolt quality control procedures include material composition analysis, mechanical testing, and dimensional verification for each production batch. The manufacturing team possesses extensive experience in titanium processing, ensuring optimal material properties and performance characteristics. Technical support services assist customers in selecting appropriate fastener specifications for specific applications.
Customers seeking detailed titanium bike bolt information or technical specifications can reach out to sales@wisdomtitanium.com. The sales team provides comprehensive support for product selection and application guidance. Quality assurance documentation accompanies all shipments, confirming compliance with specified requirements and industry standards. Manufacturing capabilities support both standard and custom titanium bolt production to meet specific customer needs.
References
1. Journal of Materials Science, "Titanium Alloys in Cycling Components", 2023
2. Corrosion Science, "Long-term Performance of Titanium Fasteners", 2023
3. Engineering Materials, "Fatigue Behavior of Titanium Bicycle Components", 2023
4. Materials Performance, "Corrosion Resistance of Titanium Alloys", 2022
5. Journal of Engineering Design, "Optimization of Titanium Bicycle Fasteners", 2023