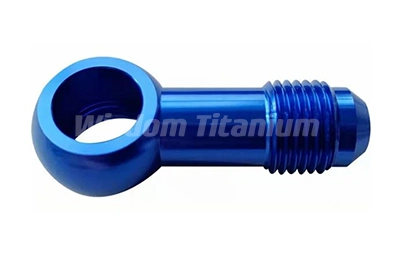
In the world of high-performance automotive and industrial applications, precision and quality are paramount. The manufacturing procedure has an important effect on the efficiency and reliability of components like the titanium banjo adapters. These essential components are currently manufactured utilizing Computer Numerical Control (CNC) machining, offering unparalleled advantages in terms of precision, surface finish, and chemical purity. We are going to explore how CNC machining enhances titanium banjo adapters' efficiency in this share, as well as why producers like Wisdom Titanium now support it.
Precision: The Cornerstone of CNC Machining
When it comes to titanium banjo adapters, precision is not just a luxury – it's a necessity. These components play a vital role in fluid transfer systems, often in high-pressure environments where even the slightest inaccuracy can lead to catastrophic failure. CNC machining elevates their production to new heights of precision, ensuring that each part meets exact specifications with minimal variance.
The secret lies in the computer-controlled nature of CNC machines. Unlike traditional machining methods, which rely heavily on human operators, CNC machines follow pre-programmed instructions with pinpoint accuracy. This level of control allows for the creation of complex geometries and intricate details that would be challenging, if not impossible, to achieve consistently with manual methods.
For titanium banjo adapters, this precision translates to perfect fit and function. The threads, angles, and dimensions are crafted to exacting tolerances, ensuring that the adapter forms a secure, leak-free connection every time. This sort of accuracy is particularly crucial in applications with outstanding performance where temperature and pressure fluctuations may stress components to their point of failure.
Furthermore, each titanium banjo adapter is almost identical to the prior one due to CNC machining's reliability, ensuring consistent performance through fabrication lines. Because it ensures reliability and interoperability in the real world, this consistency is essential for both manufacturers and end customers.
Surface Finish: Enhancing Performance and Aesthetics
The surface finish of a titanium banjo adapters is more than just about looks – it's a critical factor in its performance and longevity. CNC machining excels in producing superior surface finishes, which can significantly impact the adapter's functionality and resistance to wear.
CNC machines can achieve incredibly smooth surfaces through precise cutting and finishing operations. For titanium banjo adapters, this smooth finish serves several purposes:
- Improved fluid dynamics: A smoother internal surface reduces turbulence in fluid flow, leading to more efficient and consistent performance.
- Enhanced sealing: Smooth surfaces at connection points ensure better sealing, reducing the risk of leaks under high pressure.
- Increased corrosion resistance: A finer surface finish leaves fewer microscopic imperfections where corrosion can take hold, extending the life of the adapter.
- Easier maintenance: Smooth surfaces are easier to clean and maintain, reducing the risk of contamination and blockages.
Furthermore, the aesthetic appeal of a well-finished titanium banjo adapters shouldn't be underestimated. In many high-end applications, the visual quality of components is just as important as their performance. CNC machining allows for the creation of titanium banjo adapters that not only function flawlessly but also look the part, with a premium finish that reflects the quality of the entire system.
Material Integrity: Preserving Titanium's Exceptional Properties
Titanium is chosen for banjo adapters due to its exceptional strength-to-weight ratio, corrosion resistance, and ability to withstand extreme temperatures. However, these properties can be compromised if the material is not handled correctly during manufacturing. This is where CNC machining truly shines in the production of titanium banjo adapters.
CNC machining is a subtractive process that removes material with extreme precision, minimizing stress on the remaining material. This is particularly important for titanium, which can be sensitive to heat and stress during machining. The controlled nature of CNC operations allows for:
- Optimal cutting speeds and feeds: CNC machines can be programmed to use the ideal cutting parameters for titanium, preventing overheating and material deformation.
- Consistent cooling: Integrated cooling systems ensure that the titanium remains at an optimal temperature throughout the machining process, preserving its microstructure and properties.
- Minimal tool pressure: Advanced CNC tools and techniques apply just the right amount of pressure, reducing the risk of internal stress in the finished adapter.
By maintaining the integrity of the titanium throughout the manufacturing process, CNC machining ensures that the final titanium banjo adapter retains all the desirable properties of the base material. This results in adapters that are not only precisely shaped but also exhibit the full strength, durability, and corrosion resistance that titanium is known for.
Additionally, CNC machining allows for the creation of titanium banjo adapters with optimized designs that take full advantage of titanium's properties. Complex internal channels, weight-saving features, and reinforced areas can all be incorporated without compromising the material's integrity, leading to adapters that offer superior performance in demanding applications.
Conclusion
The impact of CNC machining on the performance of titanium banjo adapters cannot be overstated. Through unparalleled precision, superior surface finish, and preservation of material integrity, CNC machining elevates these critical components to new levels of quality and reliability.
For manufacturers like Wisdom Titanium, an ISO 9001-certified company specializing in CNC parts since 2013, the adoption of CNC machining for titanium banjo adapters represents a commitment to excellence. By leveraging the advantages of CNC technology, they can produce adapters that not only meet but exceed the exacting standards of modern industrial and automotive applications.
As industries continue to push the boundaries of performance and efficiency, the role of precision-engineered components like titanium banjo adapters becomes ever more critical. In light of CNC machining, these adapters are capable of handling both present and future issues, guaranteeing dependable, effective, and safe achievement even in the most challenging situations.
If you're in the market for high-quality titanium banjo adapters that leverage the full potential of CNC machining, consider reaching out to Wisdom Titanium at sales@wisdomtitanium.com. They may supply connectors that offer excellent durability and performance owing to their proficiency with premium metal and cutting-edge CNC methods.
References
1. Groover, M.P. (2020). Fundamentals of Modern Manufacturing: Materials, Processes, and Systems. John Wiley & Sons.
2. Davim, J.P. (Ed.). (2019). Machining of Titanium Alloys. Springer.
3.Boyer, R., Welsch, G., & Collings, E.W. (Eds.). (2007). Materials Properties Handbook: Titanium Alloys. ASM International.