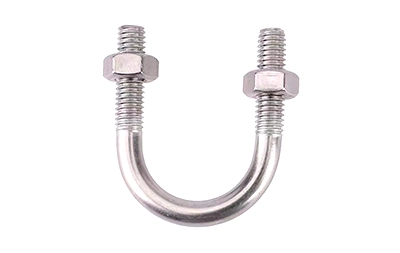
How do titanium U-bolts compare to other materials in terms of weight?
As a designer profoundly engaged in the realm of materials science, the quest for the ideal material for explicit applications is much the same as a tireless pursuit of flawlessness. In this article, I dive into the domain of attaching frameworks, particularly focusing on Titanium U Bolts, and look at the lightweight miracle of titanium against its counterparts. From steel to aluminum, every material has its unique arrangement of qualities, and through a meticulous assessment, we uncover which material rules in the space of weight proficiency.
Introduction: Understanding the Significance of Weight in Fastening Systems
In the complicated universe of designing, where accuracy and execution are paramount, the meaning of weight in securing frameworks couldn't possibly be more significant. Each part, every material decision, and each plan choice resonates through the whole structure, influencing its proficiency, durability, and ultimately, its success in the field.
Consider a situation where a vehicle hurtles down the interstate or an airplane takes off through the sky. In these powerful conditions, overabundance weight can hinder execution, increment fuel consumption, and compromise wellbeing. This is where the significance of lightweight attaching frameworks, such as Titanium U Bolts, becomes clear.
U-bolts, those unassuming yet crucial parts, assume an essential part in securing various components of hardware, structures, and gatherings. From securing pipes in industrial settings to supporting basic parts in automotive and aviation applications, these clasp bear critical loads and endure tenacious powers.
The quest for ideal execution drives designers to investigate materials with the best mix of solidarity, durability, and weight effectiveness. In this pursuit, the decision of material for U-bolts turns into a point of convergence of examination and development.
Titanium U-Bolts: The Lightweight Champion
Titanium U Bolts stand as the encapsulation of designing ingenuity and material greatness in the domain of attaching frameworks. Prestigious for their wonderful solidarity to-weight proportion, these lightweight heroes offer unparalleled execution and flexibility across a horde of utilizations.
At the core of titanium's superiority lies its phenomenal properties. Flaunting a thickness roughly a portion of that of steel, titanium conveys substantial weight investment funds without thinking twice about strength or durability. This trademark is particularly advantageous in weight-delicate industries such as aviation, automotive hustling, and marine designing, where each ounce saved means upgraded productivity and execution.
Past its lightweight nature, titanium shows excellent consumption obstruction, making it impervious to the desolates of rust and corruption, even in cruel conditions. This inborn versatility ensures the life span and dependability of titanium U bolts, safeguarding basic associations and structural honesty overstretched times of administration.
Also, titanium's natural biocompatibility and hypoallergenic properties pursue it an optimal decision for applications in clinical gadgets and inserts, where security and similarity with the human body are paramount contemplations.
Steel U-Bolts: The Stalwart of Tradition
Steel U-bolts, the stalwart of tradition in the realm of fastening systems, embody a legacy of reliability, durability, and versatility that has withstood the test of time. With a history rooted in industrial applications and engineering practices, steel U-bolts continue to serve as steadfast anchors in a wide array of industries and settings.
One of the defining characteristics of steel U-bolts is their robustness and resilience. Fabricated from high-strength steel alloys, these fasteners exhibit exceptional mechanical properties, including impressive tensile and yield strength. This inherent strength allows steel U-bolts to withstand substantial loads and forces, making them indispensable in heavy-duty applications where durability is paramount.
Furthermore, steel U-bolts offer a cost-effective solution for fastening challenges, providing a balance between performance and affordability. Their widespread availability and ease of manufacturing make them a preferred choice for a diverse range of projects, from construction and infrastructure to automotive and machinery.
Aluminum U-Bolts: The Featherweight Challenger
Aluminum, celebrated for its featherlight demeanor, presents a compelling alternative to traditional materials. In this section, we shed light on the unique characteristics of aluminum U-bolts, exploring its lightweight allure and its implications for diverse applications. Despite its undeniable appeal, we scrutinize aluminum's limitations in terms of strength and durability, offering a balanced perspective in our evaluation.
Comparative Analysis: Weighing the Options
Weight Efficiency:
Titanium U Bolts: Offers the highest weight efficiency, with a density approximately half that of steel and significantly lower than aluminum.
Aluminum: Provides substantial weight savings compared to steel, making it a competitive choice for lightweight applications.
Steel: While durable and robust, steel U-bolts are the heaviest option, which may be a limiting factor in weight-sensitive applications.
Strength and Durability:
Titanium: Flaunts outstanding solidarity to-weight proportion, making it inconceivably solid and durable regardless of its lightweight nature. Shows superior erosion opposition.
Steel: Known for its high strength and durability, steel U-bolts succeed in hard core applications where dependability is paramount. Susceptible to erosion without appropriate covering or treatment.
Aluminum: Offers great solidarity to-weight proportion, but by and large not so solid as steel or titanium. Requires careful thought in destructive conditions, although naturally impervious to erosion due to the arrangement of an oxide layer.
Cost:
Steel: Ordinarily the most financially savvy choice due to its far and wide accessibility and moderately low manufacturing costs.
Aluminum: Decently valued, falling among steel and titanium concerning cost. Can offer long haul reserve funds through reduced fuel consumption and support in weight-touchy applications.
Titanium U Bolts: The most costly choice due to its shortage and testing manufacturing processes. In any case, its excellent presentation and life span might justify the higher starting interest in specific applications.
Application Suitability:
Titanium: Ideal for aviation, marine, and superior execution applications where weight reduction, strength, and consumption opposition are paramount.
Aluminum: Appropriate for automotive, marine, and sporting applications where weight reserve funds and erosion obstruction are significant contemplations.
Steel: Liked for hard core industrial, construction, and infrastructure projects where strength, durability, and cost-adequacy are focused on over weight reserve funds.
Conclusion:
Navigating the Maze of Material Selection
In the labyrinth of material selection for fastening systems, the quest for the perfect balance between weight, strength, and durability is perpetual. In this conclusive segment, we reflect on the insights gleaned from our comparative analysis and offer pragmatic recommendations for engineers and designers alike. Whether it be the lightweight allure of titanium, the stalwart reliability of steel, or the featherlight demeanor of aluminum, each material presents a spectrum of possibilities, awaiting discerning minds to chart the course towards engineering excellence.If you want to purchase this product, please contact us at janet@wisdomtitanium.com.
References:
"Titanium Alloys in Aerospace Engineering" - https://www.nasa.gov/centers/langley/news/factsheets/Titanium.html
"Steel as a Material for Fasteners" - https://www.engineeringtoolbox.com/steel-bolts-strength-d_1481.html
"Aluminum Fasteners: Benefits and Limitations" - https://www.boltdepot.com/fastener-information/materials-and-grades/aluminum.aspx