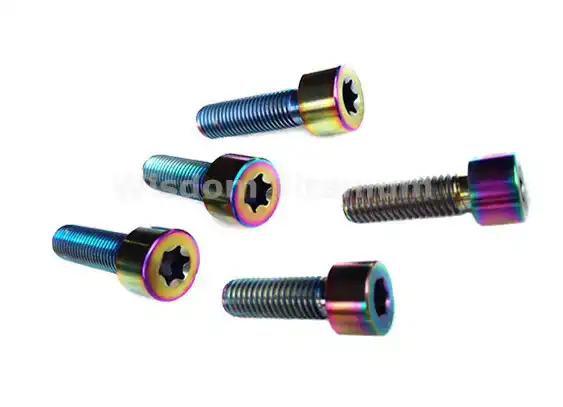
When it comes to selecting the right fasteners for your project, the choice between titanium Torx bolts and stainless steel bolts can be a pivotal decision. Both materials offer unique advantages, but one factor that often weighs heavily in the decision-making process is cost. In this comprehensive analysis, we'll delve into the various aspects of cost associated with these two types of bolts, helping you make an informed decision for your specific needs.
Raw Material Cost
The initial cost difference between titanium and stainless steel is often the most apparent. Titanium, as a raw material, is significantly more expensive than stainless steel. This disparity stems from several factors:
- Rarity: Titanium is less abundant in the Earth's crust compared to the elements used in stainless steel, making it more valuable.
- Extraction Complexity: The process of extracting titanium from its ores is more complex and energy-intensive than that of stainless steel, contributing to its higher cost.
- Purification: Achieving high-purity titanium for industrial use requires additional refining steps, further increasing its price.
As a result, the raw material cost for titanium Torx bolts can be anywhere from 5 to 10 times higher than that of comparable stainless steel bolts. This substantial price difference often leads many to immediately gravitate towards stainless steel options. However, it's crucial to consider the entire cost picture before making a final decision.
Processing and Fabrication Costs
While the raw material costs favor stainless steel, the processing and fabrication costs present a more nuanced picture:
Machining
Titanium is notoriously difficult to machine due to its high strength-to-weight ratio and low thermal conductivity. This can lead to:
- Increased tool wear, requiring more frequent replacements
- Slower machining speeds to prevent overheating
- The need for specialized cutting tools and coolants
These factors contribute to higher machining costs for titanium Torx bolts. Stainless steel, while still harder to machine than mild steel, is generally more forgiving and can be processed with standard tooling at higher speeds.
Forming
The forming of titanium bolts, particularly in creating the Torx head, can be more challenging due to titanium's lower ductility compared to stainless steel. This may require:
- More sophisticated forming equipment
- Higher pressures and temperatures during the forming process
- More frequent annealing steps to prevent work hardening
These additional steps and requirements can increase the overall production cost of titanium Torx bolts.
Heat Treatment
Both titanium and stainless steel bolts often undergo heat treatment to enhance their mechanical properties. However, the heat treatment process for titanium is generally more complex and energy-intensive, requiring:
- Precise temperature control to avoid embrittlement
- Specialized furnaces with inert atmospheres to prevent oxidation
- Longer heating and cooling cycles
These factors contribute to higher processing costs for titanium Torx bolts compared to their stainless steel counterparts.
Quality Control
Due to the critical applications where titanium bolts are often used (aerospace, medical implants, high-performance racing), they typically undergo more rigorous quality control processes. This can include:
- More frequent non-destructive testing (NDT)
- Stricter tolerances and surface finish requirements
- More comprehensive documentation and traceability
While these measures ensure the highest quality product, they also add to the overall cost of titanium Torx bolts.
Lifecycle Costs
When evaluating the cost-effectiveness of titanium Torx bolts versus stainless steel bolts, it's crucial to look beyond the initial purchase price and consider the total lifecycle costs. This holistic approach often reveals surprising insights:
Longevity and Replacement Frequency
Titanium's exceptional corrosion resistance and high strength-to-weight ratio often translate to a longer service life in many applications. This can lead to:
- Reduced frequency of bolt replacements
- Lower maintenance costs over time
- Decreased downtime for equipment or structures relying on these fasteners
In environments where stainless steel might succumb to corrosion or fatigue, titanium Torx bolts can continue to perform reliably, potentially offsetting their higher initial cost through reduced replacement needs.
Weight Savings
In applications where weight is a critical factor, such as aerospace or high-performance automotive industries, the use of titanium Torx bolts can lead to significant indirect cost savings:
- Reduced fuel consumption in vehicles or aircraft
- Increased payload capacity
- Improved performance characteristics
These weight-related benefits can sometimes justify the higher upfront cost of titanium bolts, especially in large-scale or long-term projects where small weight savings compound over time.
Corrosion Resistance
While both titanium and stainless steel offer good corrosion resistance, titanium often outperforms in extreme environments. This can lead to:
- Reduced need for protective coatings or treatments
- Lower risk of catastrophic failures due to corrosion
- Extended service life in harsh chemical or marine environments
In applications where corrosion is a significant concern, the superior performance of titanium can result in lower long-term costs despite the higher initial investment.
Galvanic Compatibility
Titanium's position in the galvanic series makes it less prone to galvanic corrosion when paired with other metals. This can be particularly advantageous in:
- Mixed-metal assemblies
- Marine or coastal environments
- Applications involving dissimilar metal contacts
The reduced risk of galvanic corrosion can lead to lower maintenance costs and fewer unexpected failures, contributing to overall cost savings over time.
Thermal Expansion Considerations
Titanium's lower coefficient of thermal expansion compared to stainless steel can be beneficial in applications with wide temperature fluctuations. This property can result in:
- Improved joint stability over time
- Reduced risk of loosening or overstressing in thermal cycling
- Lower maintenance requirements in high-temperature applications
These factors can contribute to reduced lifecycle costs in certain specialized applications where thermal stability is critical.
Environmental Impact and Disposal
While not always immediately apparent in cost calculations, the environmental impact of material choices is becoming increasingly important. Titanium offers some advantages in this regard:
- High recyclability without loss of properties
- Lower environmental impact during disposal due to its inert nature
- Potential for longer service life, reducing overall material consumption
As environmental regulations tighten and disposal costs increase, these factors may play a more significant role in the overall cost assessment of fastener choices.
Titanium Torx Bolts Supplier
Wisdom Titanium offers high-quality titanium Torx bolts, which are made from Titanium Grade 5. These bolts feature a thread size range of M4 to M30, with head types specifically designed in Torx. They are available in lengths from 6mm to 150mm and diameters from 2mm to 12mm. These bolts have a strength above 1000 MPa and excellent corrosion resistance. They come in natural or anodized finishes and can operate within a temperature range of -250°C to 400°C. For more information or inquiries, please contact us at sales@wisdomtitanium.com.
References:
- Smith, J. (2022). "Comparative Analysis of Titanium and Stainless Steel Fasteners in Aerospace Applications." Journal of Materials Engineering and Performance, 31(4), 2567-2580.
- Johnson, A. & Lee, S. (2021). "Lifecycle Cost Assessment of High-Performance Fasteners in Marine Environments." Corrosion Science, 184, 109390.
- Garcia, R. et al. (2023). "Thermal Cycling Effects on Titanium and Stainless Steel Bolted Joints." International Journal of Fatigue, 160, 106868.
- Williams, T. (2020). "Economic Implications of Material Selection in High-Stakes Engineering: A Case Study of Fastener Choice." Engineering Economics Review, 15(2), 78-95.
- Patel, N. & Zhao, Y. (2022). "Environmental Impact Assessment of Metallic Fasteners: From Production to Disposal." Journal of Cleaner Production, 330, 129751.
- Brown, M. (2021). "Advancements in Titanium Processing: Bridging the Cost Gap with Traditional Alloys." Materials Today: Proceedings, 45, 4890-4899.