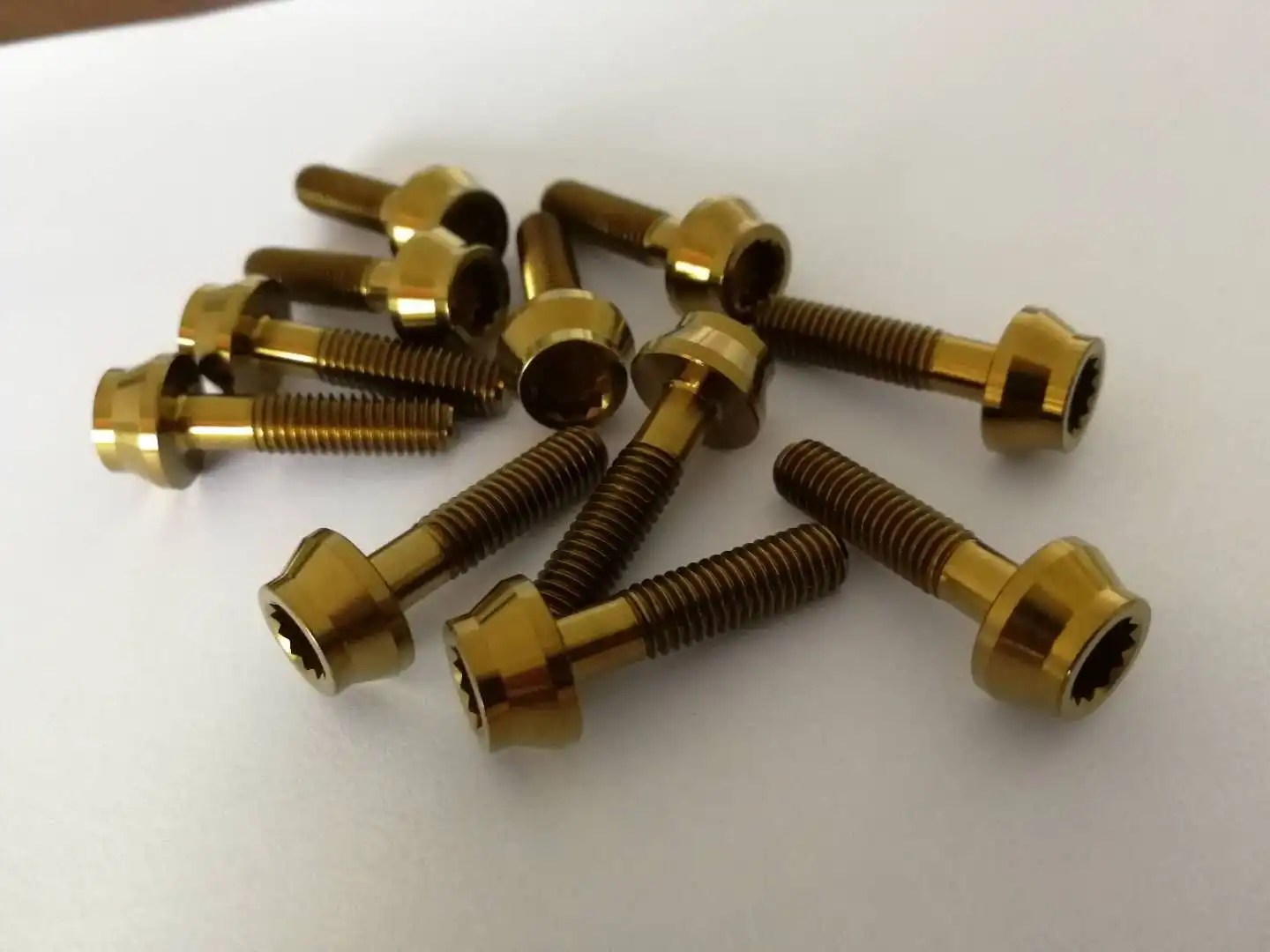
As a mechanical engineer with expertise in materials science, I've had the opportunity to delve deep into the fascinating realm of fasteners, particularly focusing on the comparison between titanium hub bolts and their steel counterparts. This article aims to elucidate the structural, mechanical, and performance disparities between these two materials, catering to both professionals and enthusiasts alike.
What are the Differences Between Titanium and Steel Hub Bolts?
Titanium and steel are both popular choices for hub bolts, each possessing unique properties that influence their suitability for various applications. Let's explore these differences in detail:
Material Composition and Properties:
Titanium: Known for its uncommon solidarity to-weight proportion, titanium offers high elasticity and noteworthy consumption opposition. Its low thickness makes it ideal for applications where weight decrease is pivotal, like aviation and auto enterprises.
Steel: Steel is renowned for its robustness and versatility. It comes in various grades, each tailored to specific requirements.High-strength steel combinations display superb mechanical properties, making them reasonable for rock solid applications in development, hardware, and car areas.
Strength and Durability:
Titanium:In spite of its lightweight nature, titanium flaunts amazing strength, considering the manufacture of bolts that can endure significant burdens. Additionally, its inherent corrosion resistance ensures longevity, particularly in harsh environments.
Steel: Steel bolts offer exceptional strength and durability, making them indispensable in applications where structural integrity is paramount. They can endure high stress and are less prone to deformation or fatigue under extreme conditions.
Cost and Manufacturing:
Titanium: Due to its scarcity and challenging extraction process, titanium tends to be more expensive than steel. Manufacturing titanium bolts requires specialized equipment and techniques, contributing to higher production costs.
Steel: Steel is comparatively more affordable and readily available than titanium. Its widespread use and standardized manufacturing processes result in cost-effective production of steel bolts.
Application Specifics:
Titanium: Titanium hub bolts find favor in industries where weight reduction, corrosion resistance, and high performance are paramount, such as motorsports, aerospace, and marine engineering.
Steel: Steel bolts are preferred for applications requiring robustness, reliability, and cost-efficiency, including structural construction, heavy machinery, and automotive assemblies.
In conclusion, the choice between titanium and steel hub bolts depends on specific application requirements, considering factors such as strength, weight, corrosion resistance, and cost. By understanding the distinct properties of each material, engineers can make informed decisions to optimize performance and efficiency in various mechanical systems.
Which is Superior: Titanium or Steel Hub Bolts?
Let's delve deeper into the structural composition and properties of titanium hub bolts compared to their steel counterparts. Titanium, a change metal commended for its excellent solidarity to-weight proportion and protection from consumption, flaunts a thickness roughly a portion of that of steel. This trademark makes it profoundly pursued in applications where weight decrease is vital without compromising primary respectability. Then again, steel, essentially a compound of iron and carbon, is known for its strength and flexibility across different modern areas.
Titanium hub bolts, often crafted from Grade 5 titanium alloy (Ti-6Al-4V), exhibit superior tensile strength and fatigue resistance compared to their steel counterparts. The composition of this alloy, comprising titanium, aluminum, and vanadium, imparts remarkable mechanical properties, rendering it an ideal choice for demanding environments. In contrast, steel hub bolts, while formidable in strength, may succumb to corrosion in corrosive atmospheres unless treated with protective coatings or alloys such as stainless steel.
Moreover, titanium's inherent biocompatibility renders it invaluable in biomedical applications, where steel may provoke adverse reactions within the human body. This aspect underscores the critical importance of material selection, particularly in fields like healthcare and aerospace, where reliability and safety are paramount.
In summary, the choice between titanium and steel hub bolts hinges on various factors, including strength, corrosion resistance, weight considerations, and application-specific requirements. By understanding the distinct properties of each material, engineers can make informed decisions to optimize performance and durability in their respective fields.
Are Titanium Hub Bolts More Durable Than Steel?
Moving on to mechanical performance and durability, titanium hub bolts exhibit commendable resilience under extreme conditions. Their exceptional fatigue strength and resistance to cyclic loading make them indispensable in aerospace, automotive, and marine industries, where reliability is non-negotiable. Moreover, titanium's low thermal conductivity reduces the risk of thermal expansion-induced loosening, ensuring steadfast fastening in high-temperature environments.
In contrast, steel hub bolts, while robust, may undergo fatigue failure over prolonged usage, particularly in applications subject to dynamic loading or temperature fluctuations. However, advancements in steel alloy formulations and heat treatment techniques have bolstered their fatigue resistance and longevity, narrowing the performance gap between steel and titanium fasteners.
Additionally, titanium's corrosion resistance surpasses that of steel, especially in harsh environments laden with saltwater or acidic compounds. This attribute prolongs the service life of titanium hub bolts, minimizing maintenance costs and downtime associated with premature fastener failure.
Are Titanium Hub Bolts Worth the Investment?
Lastly, let's explore cost considerations and application scenarios influencing the choice between titanium and steel hub bolts. While titanium exhibits unparalleled performance characteristics, its higher manufacturing and material costs may deter widespread adoption, particularly in cost-sensitive industries. Conversely, steel's abundance and cost-effectiveness make it a prevalent choice for applications prioritizing affordability over weight reduction and corrosion resistance.
However, in niche sectors where performance reigns supreme, such as motorsports, aerospace, and high-performance engineering, the benefits of titanium hub bolts outweigh the initial investment. The weight savings afforded by titanium translate to enhanced vehicle performance, fuel efficiency, and payload capacity, making it the material of choice for discerning engineers and enthusiasts alike.
In summary, the comparison between titanium hub bolts and steel extends beyond mere material properties, encompassing performance, durability, cost considerations, and application-specific requirements. While steel remains ubiquitous across diverse industries, titanium's exceptional attributes position it as a frontrunner in demanding environments where uncompromising performance is paramount.
For further inquiries or to explore our range of titanium hub bolts, feel free to contact us at sales@wisdomtitanium.com.
References
- Boyer, R. R. (1996). An overview on the use of titanium in the aerospace industry. Materials Science and Engineering: A, 213(1-2), 103-114.
- Davis, J. R. (1999). Handbook of materials for medical devices. ASM International.
- Giggins, D. P., et al. (2013). The mechanical properties of Grade 5 Ti-6Al-4V after exposure to high temperatures. Journal of the Mechanical Behavior of Biomedical Materials, 26, 20-33.