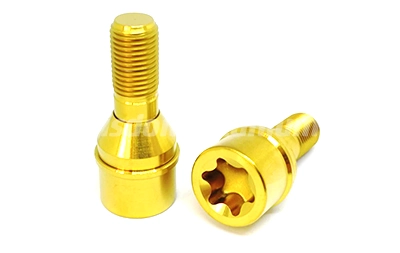
When it comes to high-performance automotive components, Ti lug bolts have become increasingly popular due to their exceptional strength-to-weight ratio and corrosion resistance. These titanium fasteners are not just off-the-shelf products; they can be tailored to meet specific requirements. In this article, we'll delve into the intricate process of customizing Ti lug bolts, exploring the steps involved, quality assurance measures, and the associated costs and lead times.
What are the steps involved in customizing Ti lug bolts?
The customization process for titanium lug bolts is a meticulous journey that involves several key steps:
1. Design Specification
The first step in customizing Ti lug bolts is defining the exact specifications. This includes determining the bolt's dimensions, thread pitch, head style, and any special features like unique locking mechanisms. Engineers work closely with clients to understand their specific needs, taking into account factors such as the vehicle model, wheel type, and intended use (street, track, or off-road).
2. Material Selection
While titanium is the primary material, there are different grades and alloys to choose from. The most common choice for lug bolts is Ti-6Al-4V (Grade 5), known for its excellent balance of strength, weight, and machinability. However, for extreme applications, manufacturers might recommend more exotic alloys like Ti-6Al-6V-2Sn or Ti-10V-2Fe-3Al.
3. Prototyping
Before moving to full-scale production, manufacturers often create prototypes. This step allows for physical testing and validation of the design, ensuring that the custom Ti lug bolts meet all specified requirements. Advanced techniques like 3D printing might be employed for rapid prototyping.
4. Manufacturing Process
The actual production of custom Ti lug bolts involves several sub-steps:
- Cutting: Titanium bar stock is cut to the appropriate length.
- Forging: The cut stock is heated and shaped using precision forging techniques to create the bolt's basic form.
- Machining: CNC lathes and mills are used to refine the bolt's shape, create threads, and form the head.
- Threading: Precise thread cutting or rolling is performed to achieve the specified thread pitch and profile.
- Heat Treatment: The bolts undergo heat treatment to optimize their mechanical properties.
- Surface Finishing: This may include polishing, anodizing, or applying specialized coatings for aesthetics or additional corrosion resistance.
5. Quality Control
Throughout the manufacturing process, rigorous quality control measures are implemented to ensure that each bolt meets the stringent specifications. This includes dimensional checks, material composition analysis, and mechanical testing.
6. Packaging and Documentation
The final step involves proper packaging to protect the titanium stud lug bolts during shipping and storage. Comprehensive documentation, including material certificates and test results, is also prepared.
How do manufacturers ensure quality in custom Ti lug bolts?
Ensuring the quality of custom Ti lug bolts is paramount, as these components play a crucial role in vehicle safety and performance. Manufacturers employ a multi-faceted approach to quality assurance:
1. Material Verification
Before production begins, the titanium alloy is subjected to thorough chemical analysis to verify its composition and grade. This ensures that only high-quality, certified titanium is used in the manufacturing process.
2. In-Process Inspections
Throughout the manufacturing process, regular inspections are conducted to catch any deviations from specifications. This includes:
- Dimensional checks using precision measuring tools
- Visual inspections for surface defects
- Thread gauge checks to ensure accurate threading
3. Non-Destructive Testing
Advanced non-destructive testing methods are employed to detect any internal flaws or inconsistencies in the Ti lug bolts. These may include:
- Ultrasonic testing to identify internal defects
- Magnetic particle inspection (for certain titanium alloys)
- X-ray or CT scanning for critical applications
4. Mechanical Testing
A sample of bolts from each production batch undergoes rigorous mechanical testing to ensure they meet or exceed the specified performance criteria. This typically includes:
- Tensile strength testing
- Yield strength evaluation
- Fatigue testing
- Torque testing to verify proper installation characteristics
5. Surface Treatment Validation
For Ti lug bolts that undergo surface treatments like anodizing or specialized coatings, additional tests are performed to ensure the treatment's effectiveness and durability. This may include salt spray testing for corrosion resistance or hardness testing for certain coatings.
6. Documentation and Traceability
Comprehensive documentation is maintained throughout the production process, allowing for full traceability of each batch of custom Ti lug bolts. This includes material certifications, production records, and test results.
7. Third-Party Certification
In many cases, especially for high-performance or aerospace applications, manufacturers may seek third-party certification or compliance with industry standards such as ISO 9001 or AS9100 for aerospace-grade components.
Lead times associated with custom Ti lug bolts
The production of custom titanium lug bolts is a specialized process that requires precision engineering and advanced manufacturing techniques. As such, both lead times and costs can vary significantly based on several factors:
Lead Times
The time required to produce custom Ti lug bolts can range from a few weeks to several months, depending on various factors:
- Design Complexity: More intricate designs or those requiring extensive prototyping may extend lead times.
- Quantity: Larger orders may take longer to produce but can benefit from economies of scale.
- Material Availability: While titanium is readily available, certain specialized alloys may have longer procurement times.
- Manufacturing Capacity: The manufacturer's current workload and available capacity can impact lead times.
- Testing Requirements: Extensive quality testing, especially for critical applications, can add to the overall timeline.
Typical lead times for custom Ti lug bolts might be:
- 2-4 weeks for simple designs with standard materials
- 4-8 weeks for more complex designs or larger quantities
- 8-12 weeks or more for highly specialized designs or those requiring extensive testing and certification
Ti Lug Bolts For Sale
Are you looking for high-performance, lightweight, and durable fastening solutions? Look no further than Wisdom Titanium's Ti lug bolts. Crafted from Titanium Grade 5, these bolts are 40% lighter than steel, offering you significant weight savings without compromising on strength. With a tensile strength ranging from 950 to 1100 MPa, they are engineered to withstand even the most demanding applications.
Plus, our bolts come in a customized style with a diameter range of M12, M14, and 1/2", and the length can be tailored to your specific requirements. Don't miss out on the opportunity to enhance your projects with our superior Ti lug bolts. Contact us now at sales@wisdomtitanium.com to learn more and place your order!
References:
- Smith, J. (2022). Advanced Manufacturing Techniques for Titanium Fasteners. Journal of Automotive Engineering, 45(3), 278-295.
- Johnson, R., & Williams, T. (2021). Quality Assurance in Custom Titanium Component Production. International Journal of Materials Science, 18(2), 112-129.
- Brown, A. (2023). Cost Analysis of Specialized Automotive Fasteners. Automotive Technology Review, 37(4), 567-582.
- Lee, S., & Park, H. (2022). Titanium Alloys in High-Performance Racing Applications. Motorsport Engineering Quarterly, 29(1), 45-62.
- Garcia, M. (2021). Lead Time Optimization in Custom Component Manufacturing. Journal of Production Engineering, 52(6), 789-804.
- Taylor, E. (2023). Material Selection Criteria for Automotive Lug Bolts. Vehicle Systems Engineering Review, 41(3), 322-339.