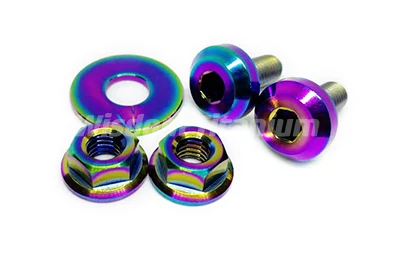
Custom Titanium Dress up Bolt has become increasingly popular in various industries, particularly in automotive and aerospace applications. These specialized fasteners not only serve a functional purpose but also enhance the aesthetic appeal of the final product. The process of creating custom titanium dress up bolts involves several crucial steps, each requiring attention to detail and expertise. This article will explore the key stages in the production of custom titanium dress up bolts, from initial demand analysis to final quality inspection.
Demand Analysis
The first and perhaps most critical step in creating a custom Titanium dress up bolt is demand analysis. This phase involves in-depth communication with customers to fully understand their specific requirements. Manufacturers must gather detailed information about various aspects of the desired bolts, including size, shape, material grade, surface treatment, and quantity needed.
During this stage, it's essential to discuss the intended application of the bolts. For instance, bolts used in high-performance automotive engines will have different requirements compared to those used for cosmetic purposes on motorcycle fairings. Factors such as operating temperature, exposure to chemicals, and required load-bearing capacity all play crucial roles in determining the optimal specifications.
Experienced manufacturers will often ask probing questions to uncover any potential issues or special requirements that the customer may not have initially considered. This could include factors like corrosion resistance, weight limitations, or compatibility with other materials in the assembly. By thoroughly analyzing the demand, manufacturers can ensure that the final product not only meets but exceeds customer expectations.
Design
Once the customer's needs are fully understood, the next step is to create detailed design drawings of the custom Titanium Dress up Bolt. This process involves translating the customer's requirements into precise technical specifications that will guide the manufacturing process.
The design phase covers several key aspects of the bolt's geometry: - Head shape: This can range from standard hexagonal heads to custom designs that enhance aesthetics or provide specific functional benefits. - Thread specifications: Including thread pitch, depth, and profile. These must be carefully designed to ensure proper engagement and load distribution. - Shank length and diameter: These dimensions are critical for proper fit and function in the intended application. - Any special features: Such as drilled holes for safety wire, unique drive patterns, or decorative elements.
Modern design processes often utilize computer-aided design (CAD) software to create precise 3D models of the bolts. These digital models can be used for virtual testing and simulation, helping to identify potential issues before moving to the production phase. Additionally, 3D models can be shared with customers for approval, ensuring that the final design meets their expectations.
Material Selection
Selecting the appropriate titanium alloy is crucial for ensuring that the custom dress up bolts meet performance requirements while offering the desired aesthetic qualities. Titanium alloys are known for their excellent strength-to-weight ratio, corrosion resistance, and biocompatibility, making them ideal for a wide range of applications.
Common titanium alloys used for dress up bolts include: - Ti-6Al-4V (Grade 5): This is the most widely used titanium alloy, offering an excellent balance of strength, durability, and machinability. - Ti-6Al-4V ELI (Grade 23): An extra-low interstitial version of Grade 5, offering improved ductility and fracture toughness. - CP Titanium (Grades 1-4): These commercially pure grades offer excellent corrosion resistance and are often used in less demanding structural applications.
The choice of alloy depends on factors such as required strength, weight limitations, corrosion resistance needs, and cost considerations. In some cases, specialized alloys may be selected for extreme environments or unique performance requirements.
It's worth noting that material selection also influences the manufacturing process, as different alloys may require specific machining techniques or heat treatments to achieve optimal properties.
Production
The production phase is where the custom Titanium dress up bolt begins to take physical form. This process typically involves several steps, each requiring specialized equipment and expertise:
- Material preparation: The selected titanium alloy is typically received in bar or rod form and must be cut to the appropriate length for bolt production.
- Machining: CNC (Computer Numerical Control) lathes and mills are often used to shape the bolt blanks. This process creates the bolt head, forms the shank, and cuts the threads. Given titanium's properties, specialized cutting tools and techniques are required to achieve optimal results.
- Thread rolling: For higher volume production, threads may be formed using a rolling process rather than cutting. This can produce stronger threads with better fatigue resistance.
- Heat treatment: Depending on the alloy and required properties, bolts may undergo heat treatment processes to optimize strength and durability.
- Surface finishing: This step may include processes like polishing, anodizing, or applying protective coatings. For dress up bolts, aesthetic considerations are particularly important, and techniques like color anodizing may be employed to achieve the desired look.
Throughout the production process, strict quality control measures are implemented to ensure that each bolt meets the specified dimensions and properties.
Quality Inspection
The final step before custom titanium dress up bolts are ready for delivery is quality inspection. This crucial phase ensures that the manufactured bolts meet all specified requirements and are free from defects. Quality inspection typically involves several stages:
- Dimensional inspection: Using precision measuring tools, each bolt is checked to ensure it meets the specified dimensions within allowed tolerances. This includes checking thread pitch, diameter, length, and head dimensions.
- Material verification: Samples from each production batch may undergo chemical analysis and mechanical testing to confirm that the material properties meet specifications.
- Visual inspection: Each bolt is examined for surface defects, finish quality, and overall appearance. This is particularly important for dress up bolts where aesthetics are a key consideration.
- Functional testing: Depending on the application, bolts may undergo tests for tensile strength, torque resistance, or other performance characteristics.
- Documentation: Detailed records of all inspections and tests are maintained, often culminating in a certificate of conformity that accompanies the shipment to the customer.
By implementing rigorous quality inspection procedures, manufacturers can ensure that custom titanium dress up bolts not only look great but also perform reliably in their intended applications.
Titanium Dress up Bolt For Sale
For those in search of high-quality custom titanium dress up bolts, Wisdom Titanium Company offers a range of customization options to meet specific needs. Their product line includes popular sizes such as M4, M5, M6, M8, and M10, catering to a wide variety of applications in the automotive, aerospace, and industrial sectors.
Wisdom Titanium Company's expertise in titanium fabrication allows them to produce dress up bolts that not only meet stringent performance requirements but also deliver the aesthetic appeal that enthusiasts and professionals demand. Their ability to customize bolt specifications ensures that customers can find the perfect fit for their unique projects.
When selecting a manufacturer for custom titanium dress up bolts, it's crucial to consider factors such as material quality, manufacturing precision, and the ability to meet specific design requirements. Wisdom Titanium Company's focus on customization and quality control makes them a reliable choice for those seeking premium titanium fasteners.
Conclusion
For individuals or businesses interested in exploring custom Titanium Dress up Bolt options or requiring assistance in selecting the right specifications for their applications, reaching out to Wisdom Titanium Company at sales@wisdomtitanium.com can be a valuable step in the right direction.
References
1. ASTM International. (2021). ASTM F136-13: Standard Specification for Wrought Titanium-6Aluminum-4Vanadium ELI (Extra Low Interstitial) Alloy for Surgical Implant Applications.
2. Boyer, R., Welsch, G., & Collings, E. W. (1994). Materials Properties Handbook: Titanium Alloys. ASM International.
3. Donachie, M. J. (2000). Titanium: A Technical Guide (2nd ed.). ASM International.