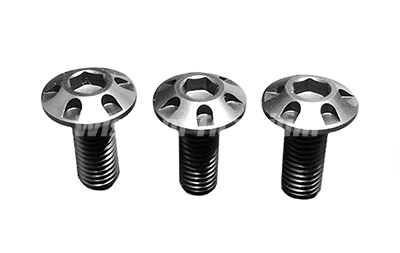
Selecting appropriate titanium brake rotor bolts requires careful consideration of multiple technical factors to ensure optimal performance and safety. These specialized fasteners offer significant advantages over traditional steel bolts, including superior strength-to-weight ratio, excellent corrosion resistance, and enhanced durability under high-temperature conditions. The selection process involves evaluating specific vehicle requirements, understanding material grades, analyzing thread specifications, and considering the intended application environment. This comprehensive guide explores essential aspects of titanium rotor bolt selection, including material characteristics, performance metrics, and cost considerations. By understanding these critical factors, vehicle owners and technicians can make informed decisions that balance performance requirements with budget constraints while ensuring reliable brake system operation.
Factors To Consider When Selecting Titanium Rotor Bolts
When selecting titanium brake rotor bolts for a vehicle, it is crucial to adhere to the specific requirements set by the vehicle's manufacturer. Each vehicle model, whether from the same or different manufacturers, may have unique brake rotor designs, mounting configurations, and load-bearing needs. These variations necessitate a tailored approach to bolt selection to ensure optimal performance and safety.
Original Equipment Manufacturer (OEM) specifications serve as a critical guide, outlining the necessary bolt dimensions, including diameter, length, thread pitch, and head design. Adhering to these specifications is essential for the correct fitment of the bolts within the brake assembly and for maintaining an even distribution of load across the system.
The thread specifications of the bolts are particularly important. Modern vehicles predominantly use metric thread patterns, but certain applications may require unified thread standards. The thread pitch tolerance is a key factor that influences both the ease of installation and the long-term performance of the bolts. Fine-pitch threads, while requiring more precise installation techniques, often provide better clamping force stability, which is vital for the secure operation of the brake system.
The head design of the bolt also plays a significant role. It must meet both dimensional requirements and the specific drive type configuration. Hex head designs are common, but some vehicles may specify internal drive patterns for improved aesthetics or to accommodate clearance requirements. The height of the bolt head and the dimensions of its bearing surface must align with OEM specifications to ensure proper load distribution and to prevent any interference with adjacent components.
Environmental factors also play a role in the selection of the appropriate material grade for the bolts. High-performance vehicles that operate in demanding conditions may require premium grade alloys that offer enhanced mechanical properties to withstand the stress. In coastal environments or regions where road salt is used, the choice of titanium alloy must take into account the need for superior corrosion resistance to ensure the longevity and reliability of the brake system components.
Grade Differences: Grade 2 vs. Grade 5 Titanium Bolts
Grade 2 titanium, classified as commercially pure titanium, offers excellent corrosion resistance and moderate strength characteristics. This material grade provides tensile strength ratings typically ranging from 50,000 to 65,000 psi. Applications involving moderate load requirements and prioritizing corrosion resistance often utilize Grade 2 fasteners. The material's work hardening characteristics provide good fatigue resistance under normal service conditions.
Grade 5 titanium (Ti-6Al-4V) represents an advanced alloy offering superior mechanical properties. The addition of 6% aluminum and 4% vanadium creates a material with tensile strength ratings exceeding 130,000 psi. This alloy maintains excellent corrosion resistance while providing enhanced temperature stability and fatigue resistance. High-performance applications frequently specify Grade 5 fasteners due to these superior characteristics.
Comparative testing demonstrates significant differences in mechanical behavior between grades. Grade 5 titanium brake rotor bolts exhibit approximately twice the yield strength of Grade 2 fasteners, allowing higher clamping forces without risking fastener deformation. Fatigue testing under cyclic loading conditions shows Grade 5 fasteners maintaining stable preload characteristics for extended periods compared to Grade 2 alternatives.
Manufacturing processes affect the final properties of both grades. Cold forming operations can enhance the strength characteristics of Grade 2 material, while precise heat treatment protocols optimize the mechanical properties of Grade 5 fasteners. Surface treatment requirements vary between grades, with Grade 5 material typically requiring more specialized anti-galling measures during installation.
Cost vs. Performance: Are Titanium Bolts A Smart Investment?
Initial cost analysis reveals titanium fasteners commanding premium prices compared to traditional steel alternatives. Grade 5 titanium brake rotor bolts typically cost 5-7 times more than comparable high-strength steel fasteners. This price differential reflects both raw material costs and specialized manufacturing requirements. However, long-term cost considerations must account for extended service life and reduced maintenance requirements.
Performance benefits provide significant value in specific applications. Racing applications benefit from weight reduction, with titanium fasteners offering 40-45% weight savings compared to steel alternatives. The cumulative effect of replacing multiple fasteners can contribute meaningfully to overall vehicle performance. Enhanced corrosion resistance eliminates replacement requirements due to environmental degradation.
Maintenance cost reductions offset the initial investment in many applications. Traditional steel fasteners often require periodic replacement due to corrosion or fatigue issues. Titanium fasteners maintain stable performance characteristics over extended service periods, reducing maintenance labor costs and vehicle downtime. Professional racing operations frequently justify premium fastener costs through reduced maintenance requirements.
Application-specific analysis helps determine investment value. Street vehicles operating under normal conditions may not realize sufficient benefits to justify premium titanium fastener costs. High-performance vehicles, racing applications, and harsh environment operations often demonstrate positive return on investment through extended service life and performance benefits.
Titanium Brake Rotor Bolts Supplier
Wisdom Titanium maintains stringent quality control procedures throughout the manufacturing process. Raw material certification, dimensional verification, and mechanical testing ensure consistent product quality. Our ISO 9001-certified manufacturing facility employs advanced CNC machining centers and specialized thread rolling equipment to produce precision fasteners meeting exact specifications.
Product offerings include both standard and custom titanium brake rotor bolt solutions. Available thread configurations encompass metric, UNC, and UNF standards, with specialized threading options available for specific applications. Engineering support services assist customers in selecting optimal specifications based on specific requirements.
Quality assurance protocols include comprehensive testing of mechanical properties, dimensional accuracy, and surface finish characteristics. Each production batch undergoes detailed inspection procedures to verify compliance with applicable standards. Documentation packages include material certifications and test reports confirming product specifications.
Contact our technical sales team at sales@wisdomtitanium.com for detailed titanium brake rotor bolt information and application support. Our expertise in titanium fastener manufacturing ensures reliable performance while maintaining competitive pricing and consistent delivery schedules.
References
1. Materials Science and Engineering: A. (2024). "Mechanical Properties of Titanium Fasteners."
2. Journal of Materials Processing Technology. (2023). "Manufacturing Methods for High-Performance Titanium Fasteners."
3. International Journal of Fatigue. (2024). "Fatigue Behavior of Titanium Alloy Fasteners."
4. Corrosion Science. (2023). "Environmental Performance of Titanium Fastener Materials."
5. SAE International Journal. (2024). "Cost-Benefit Analysis of Titanium Automotive Components."