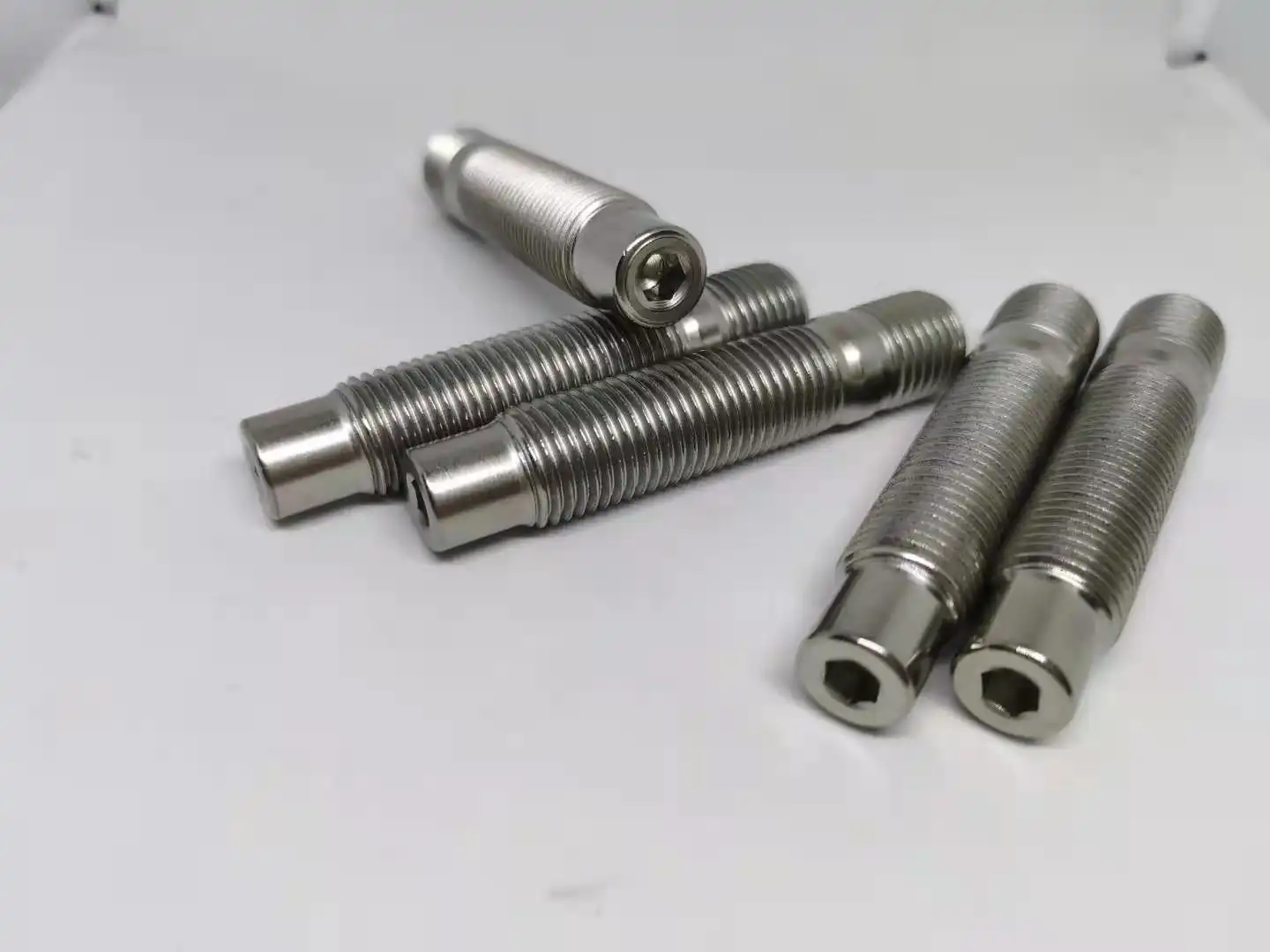
Can Titanium Studs Be Used in High-Temperature Environments?
Due to their effective resistance to high temperatures, titanium studs are useful in industrial applications where heat resistance is essential. The scientific foundation for their performance is provided by the distinctive properties of titanium alloys.
To begin, titanium alloys are better able than many other metals to maintain their strength and structural integrity at high temperatures. This is due to the fact that titanium has a high melting point and can form an oxide layer that seals out air and resists heat better.
Second, the low thermal expansion coefficient of titanium ensures dimensional stability under thermal stress, reducing the likelihood of deformation or failure in high-temperature environments. Applications that require precise aspects and reliable execution greatly benefit from this property.
Thirdly, specific alloying and heat treatment can further enhance the high-temperature properties of titanium alloys. Due to alloying elements like aluminum and vanadium, which can increase strength and heat resistance, titanium studs perform well at temperatures of several hundred degrees Celsius.
In harsh environments where oxidation or chemical reactions could eventually degrade other materials, the corrosion resistance of titanium alloys ensures their long-term viability and dependability.
In industries like aerospace, automotive, and chemical processing, titanium studs are preferred due to their capacity to maintain structural integrity and functionality in extreme heat. They make essential systems and components safer, more reliable, and more effective.
As research into titanium alloys continues, it is anticipated that high-temperature performance will improve further, expanding the range of potential applications for titanium studs. Titanium is the material of choice for demanding industrial applications that require dependable performance in challenging thermal conditions due to its combination of strength, lightness, resistance to corrosion, and heat resistance.
Understanding Titanium's Properties
Titanium is a versatile transition metal that stands out because of its distinctive combination of properties, which make it popular in a variety of sectors. It rivals steel's strength despite being significantly lighter and approximately 45% denser than steel. When it is necessary to lose weight without compromising strength, this quality is critical.
In aerospace engineering, titanium's lightweight but durable properties are essential for increasing fuel efficiency and performance. It makes it possible to make parts for airplanes that are strong and light, which helps cut operational costs and make it possible to carry more payload. Additionally, titanium's corrosion resistance makes it ideal for aerospace applications, ensuring longevity and dependability.
In automotive applications where efficiency and performance are crucial, titanium's lightweight properties help to improve handling and fuel efficiency. In engine parts like valves, connecting rods, and exhaust systems, titanium's advantages of strength and weight allow for improved engine performance and durability.
Additionally, due to its biocompatibility and strength-to-weight ratio, titanium is an excellent material for medical implants and surgical instruments. By speeding up healing and lowering the risk of complications in orthopedic implants, dental implants, and surgical instruments, it ensures patient safety and comfort.
Due to its resistance to corrosion from seawater, lightweight durability, and inertness to numerous chemicals, titanium is utilized in chemical processing in addition to these industries.
As technology advances, the applications of titanium alloys continue to grow across industries. These alloys, which are designed to maximize specific properties like heat resistance, fatigue resistance, and machinability, further enhance the versatility and performance of titanium in demanding applications.
In conclusion, due to its unique combination of low weight and high strength, titanium is a material of choice in industries where performance, durability, and efficiency are crucial. Its ongoing development suggests that it will continue to be creative and have additional applications.
High-Temperature Performance
How titanium will hold up under heat stress is one of the important issues to consider when using it in high-temperature situations. Titanium has exceptional resistance to oxidation, and at high temperatures it forms a protective oxide layer that can prolong its useful life in air up to 500°C (932°F) and in even higher inert atmospheres.
Oxidation Resistance Mechanism
At temperatures above 430°C (806°F), titanium reacts with oxygen to form titanium dioxide (TiO2) on its surface. This oxide layer acts as a barrier, protecting the underlying metal from further oxidation. This phenomenon is crucial in preventing the degradation of titanium studs when exposed to high-temperature operations.
Mechanical Strength at Elevated Temperatures
While titanium retains its structural integrity at high temperatures due to its oxidation resistance, its mechanical strength gradually decreases as temperatures rise. For instance, at temperatures exceeding 300°C (572°F), titanium alloys begin to undergo creep deformation, which can affect their long-term performance in load-bearing applications.
Applications and Limitations
Titanium studs find use in various industries such as aerospace, automotive, and chemical processing, where they are exposed to elevated temperatures during operation. However, it's essential to consider specific alloy compositions and operating conditions to ensure optimal performance and longevity.
Alloy Considerations
The performance of titanium studs in high-temperature environments can vary significantly depending on the alloy used. For instance, titanium alloys like Ti-6Al-4V offer enhanced strength and heat resistance compared to commercially pure titanium (CP Ti). Alloy selection plays a crucial role in determining the maximum temperature capability and mechanical properties required for specific applications.
Conclusion
In conclusion, the exceptional properties of titanium, such as its resistance to oxidation and impressive strength-to-weight ratio, make it an excellent choice for use in environments with high temperatures. Titanium studs can effectively withstand high temperatures thanks to these properties without compromising their structural integrity. However, there are several factors that must be carefully considered to achieve peak performance. First, it's important to choose the right titanium alloy because different alloys have different mechanical and heat resistance levels. Second, determining the studs' long-term durability and dependability requires an understanding of the specific operating temperatures and environmental conditions in which they will be utilized. Lastly, titanium studs' performance and longevity in high-temperature applications are further enhanced by proper installation and maintenance procedures. Titanium studs can consistently meet the stringent requirements of high-temperature environments in a variety of industrial sectors by thoroughly addressing these considerations.
For more information on titanium studs and their applications, feel free to contact us at sales@wisdomtitanium.com.
References:
- ASM International. (2000). Titanium and Titanium Alloys. ASM Handbook, Volume 2.
- Boyer, R., & Welsch, G. (Eds.). (2003). Materials Properties Handbook: Titanium Alloys. ASM International.
- Lütjering, G., & Williams, J. C. (2007). Titanium. Springer Science & Business Media.