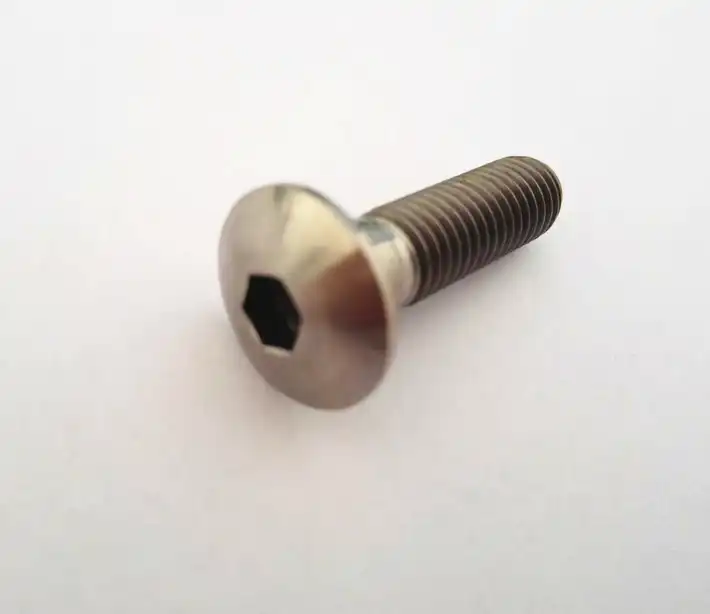
Can titanium screws break?
In present day clinical and designing practices, titanium screws assume a pivotal part in different applications, going from muscular medical procedures to aviation design. Understanding the variables that add to their solidarity and sturdiness is fundamental to guaranteeing the achievement and wellbeing of the frameworks they support. In this article, I will dive into whether or not titanium screws can break, investigating the material properties, plan contemplations, and certifiable situations that impact their exhibition.
Material Properties of Titanium:
High Solidarity to-Weight Proportion: Titanium is one of the most grounded metals per unit mass, making it ideal for applications where weight decrease is basic without compromising underlying respectability. This property is especially worthwhile in aviation and auto businesses.
Erosion Opposition: Titanium shows excellent protection from consumption, even in cruel conditions, for example, seawater and substance handling plants. Its oxide layer gives a defensive hindrance, forestalling further corruption and broadening its life expectancy.
Biocompatibility: Titanium is biocompatible, meaning it is all around endured by the human body and doesn't evoke unfavorable responses when embedded. This property makes it priceless in clinical inserts, like muscular screws and dental inserts.
Low Warm Extension: Titanium screw has a low coefficient of warm development, meaning it grows and contracts negligibly with temperature changes.
This property upgrades its layered solidness and protection from warm pressure, making it appropriate for cryogenic applications and high-temperature conditions.
Ductility: Despite its high strength, titanium remains ductile, allowing it to deform plastically before fracturing. This property enables components to withstand bending and forming processes without failure.
Non-magnetic: Titanium is non-magnetic, which is advantageous in applications where magnetic interference is undesirable, such as medical devices and certain electronic equipment.
High Melting Point: Titanium has a relatively high melting point, exceeding 1,600°C (2,912°F). This property makes it suitable for use in high-temperature applications, including aerospace propulsion systems and industrial furnaces.
Design Considerations:
Geometry and Thread Profile: The design of the screw's geometry and thread profile influences its ability to engage with the mating surface effectively. Optimizing the thread pitch, depth, and angle ensures proper load distribution and enhances the screw's resistance to loosening or stripping.
Surface Finish: The surface finish of titanium screws affects their frictional properties, corrosion resistance, and fatigue life. Smoother surfaces reduce friction during insertion and minimize the risk of galling, while appropriate surface treatments, such as passivation or anodizing, enhance corrosion resistance and durability.
Material Purity and Composition: The purity and composition of titanium alloys used in screw manufacturing impact their mechanical properties and biocompatibility. Selecting high-quality materials with minimal impurities ensures consistent performance and reduces the risk of material degradation or failure.
Thread Locking Mechanisms: Incorporating thread locking mechanisms, such as adhesives or mechanical locking features, enhances the screw's resistance to vibration-induced loosening. These mechanisms help maintain joint integrity and prevent premature failure in dynamic or high-stress environments.
Load Distribution and Fixation: Proper selection of screw size, length, and spacing is essential to achieve optimal load distribution and fixation strength in the intended application. Engineers must consider factors such as the material properties of the mating surfaces, applied loads, and environmental conditions to design screws that provide adequate stability and support.
Real-World Performance:
Orthopedic Surgery: In orthopedic surgeries, they are used to fixate fractures, stabilize bone fragments, or anchor implants. The success of these procedures depends on factors such as proper screw size and placement, bone quality, and patient-specific biomechanics. While they offer excellent biocompatibility and strength, complications such as screw loosening, breakage, or bone resorption can occur due to factors like inadequate fixation, implant fatigue, or patient non-compliance.
Aerospace Engineering: Titanium screws are widely used in aerospace applications for their lightweight, high-strength properties. In aircraft and spacecraft, these screws are subjected to dynamic loads, vibration, thermal cycling, and exposure to harsh environments. Proper design, material selection, and quality control are crucial to ensuring the screws' reliability and structural integrity under these demanding conditions. Failures can occur due to factors such as stress corrosion cracking, fatigue, or manufacturing defects.
Industrial Machinery: Titanium screws find applications in industrial machinery and equipment, where they may be exposed to corrosive chemicals, high temperatures, or heavy loads. Proper material selection, surface treatments, and maintenance practices are essential to mitigate corrosion, wear, and fatigue, which can compromise the screws' performance and longevity. Failures may occur due to factors such as stress corrosion, erosion, or galvanic corrosion in mixed-metal assemblies.
Case Studies and Research Findings:
Orthopedic Surgery: Research in orthopedic surgery has focused on evaluating the biomechanical properties and clinical outcomes of titanium screws used for fracture fixation, spinal fusion, and joint reconstruction. Studies have investigated factors such as screw design, insertion technique, and bone-implant interface mechanics to optimize fixation stability and promote bone healing. Case reports document complications such as screw loosening, breakage, or migration, highlighting the importance of proper surgical planning and implant selection.
Aerospace Engineering: Aerospace research has explored the fatigue behavior, corrosion resistance, and structural integrity of them in aircraft and spacecraft applications. Experimental studies and computational modeling have been conducted to assess the effects of environmental factors, loading conditions, and manufacturing variability on screw performance. Case studies document incidents such as stress corrosion cracking, fretting fatigue, or bolt-hole elongation, informing design improvements and maintenance practices in aerospace systems.
Biomedical Implants: Biomedical research has investigated the long-term clinical outcomes, patient satisfaction, and complication rates associated with them used in dental, orthopedic, and craniofacial implants. Clinical trials and retrospective analyses have evaluated factors such as implant stability, soft tissue response, and bone integration over time. Case studies report complications such as implant infection, peri-implantitis, or implant failure due to biomechanical factors, emphasizing the importance of patient selection, surgical technique, and implant maintenance protocols.
Conclusion:
In conclusion, titanium screws exhibit exceptional strength and durability due to their unique material properties and thoughtful design considerations. While the risk of breakage is low under normal conditions, it is essential to consider various factors that may influence their performance in real-world applications. By adhering to best practices in material selection, design optimization, and quality assurance, engineers and medical professionals can maximize the reliability and longevity of them, ensuring the safety and well-being of patients and the success of engineering projects.If you want to purchase this product, please contact us at janet@wisdomtitanium.com.