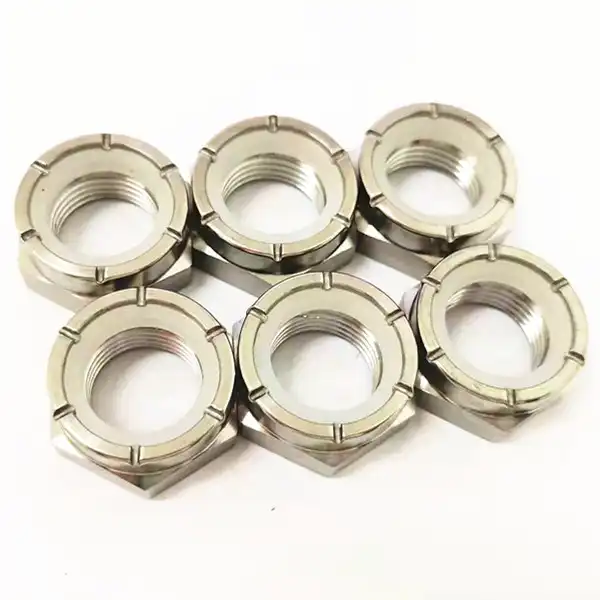
In the field of automotive engineering, prioritizing safety is of utmost importance as every element, including material choices like nuts, significantly impacts a vehicle's overall safety. Despite their seemingly small size, nuts play a vital role in upholding the structural integrity of a vehicle. With continuous progress in materials science, the automotive sector has been exploring alternatives to traditional steel nuts. Titanium, renowned for its exceptional strength-to-weight ratio and resistance to corrosion, has emerged as a promising candidate in this regard. The question arises: can titanium lock nuts truly elevate safety levels in automotive applications? To answer this query, a deeper exploration into the scientific aspects of titanium's properties and performance within automotive settings is essential to ascertain the potential benefits and enhancements that titanium lock nuts may offer in bolstering safety standards in vehicle construction.
To begin, it is crucial to comprehend the pivotal roles played by lock nuts in automotive applications. These nuts are employed to secure a wide array of components such as wheels, steering systems, suspension parts, and crucial assemblies. Their primary function is to counteract loosening caused by vibration, thereby guaranteeing the enduring tight fastening of these components throughout the vehicle's operational lifespan. Any lapses in this capacity could result in severe repercussions, impacting not only the vehicle's performance but, more significantly, its safety. Therefore, the reliability and effectiveness of lock nuts are paramount, making the choice of materials for these components a critical consideration in ensuring the overall safety and functionality of automobiles.
In the past, lock nuts have predominantly been crafted from steel alloys owing to their cost-effectiveness and satisfactory mechanical characteristics. Nevertheless, steel is not without its shortcomings, particularly in challenging automotive settings. Considerations such as weight, susceptibility to corrosion, and thermal expansion can impact the operational effectiveness and durability of steel lock nuts, potentially posing safety risks. This is where titanium comes into play, offering an alternative that addresses these concerns and presents an opportunity to enhance the safety and reliability of lock nuts in automotive applications. With its exceptional strength-to-weight ratio and superior resistance to corrosion and thermal expansion, titanium emerges as a compelling candidate for elevating the performance and safety standards of lock nuts in the automotive industry.
Titanium: Revolutionizing Automotive Performance and Durability
Titanium presents various clear benefits over steel when applied in auto settings. Principally, its remarkable solidarity to-weight proportion positions it as an ideal choice for parts requiring weight decrease without compromising underlying respectability. Explicitly concerning lock nuts, this infers that titanium nuts can convey identical security to steel nuts while outstandingly decreasing generally weight. This reduction in unsprung mass can possibly improve vehicle taking care of, dependability, and eco-friendliness. Thus, the utilization of titanium secure nuts in auto applications tends to somewhere safe and secure worries as well as adds to more extensive execution upgrades, lining up with the business' constant quest for further developed productivity and usefulness.
Furthermore, titanium showcases exceptional corrosion resistance, especially in challenging environments like exposure to saltwater and acidic surroundings. Within automotive uses, where encounters with road salt, moisture, and diverse chemicals are unavoidable, the demand for materials resistant to corrosion is substantial. Through the utilization of titanium lock nuts, automakers can effectively reduce the potential for failures stemming from corrosion, consequently bolstering the overall safety and durability of their vehicles. By integrating titanium components known for their resilience against corrosion, automotive manufacturers not only enhance the longevity of their products but also prioritize the safety and reliability of their vehicles, aligning with industry standards for high-performance and long-lasting automotive solutions.
Titanium's resistance to thermal expansion represents another crucial attribute. Unlike steel, which is prone to substantial expansion and contraction in response to temperature variations, titanium maintains a relatively stable profile. This feature proves especially advantageous in automotive settings where components endure extreme temperatures during operation. Through the adoption of titanium lock nuts, manufacturers can guarantee consistent and dependable fastening performance across diverse operating conditions, thereby diminishing the risk of loosening and potential failure. By leveraging the stability of titanium in the face of thermal fluctuations, automotive industry professionals can enhance the reliability and safety of their vehicles, addressing a critical aspect of performance under varying environmental and operational circumstances.
Additionally, titanium showcases exceptional fatigue resistance, rendering it exceptionally durable when subjected to cyclic loading conditions. Within automotive applications, where components endure repeated vibrations and stresses, the risk of fatigue failure is a notable concern. Through the incorporation of titanium lock nuts, manufacturers can effectively prolong the fatigue life of vital assemblies, consequently bolstering the overall safety and dependability of vehicles. By harnessing the superior fatigue resistance inherent in titanium, automotive industry professionals can elevate the longevity and performance of their products, addressing a critical aspect of reliability in the face of continual mechanical stress and operational demands.
While titanium presents a plethora of advantages, it is essential to acknowledge the accompanying challenges, particularly concerning cost and manufacturing intricacies. Notably, titanium commands a considerably higher price tag compared to steel, influencing the overall production expenses in the automotive sector. Moreover, the machining of titanium demands specialized equipment and skilled expertise, further complicating the manufacturing process. Despite these hurdles, continuous progress in manufacturing technologies and the realization of economies of scale are steadily rendering titanium more attainable and cost-efficient for automotive purposes. As advancements persist, the accessibility and viability of utilizing titanium in vehicle production are progressively improving, paving the way for enhanced performance, durability, and safety in automobiles while navigating the complexities associated with integrating this exceptional material.
Conclusion
In summary, incorporating titanium lock nuts in automotive settings holds promise for substantial improvements in safety and performance. Titanium's remarkable strength-to-weight ratio, corrosion resistance, thermal stability, and fatigue resistance present notable advantages over conventional steel nuts. By harnessing these attributes, automotive manufacturers have the opportunity to enhance the dependability, longevity, and safety of their vehicles. Despite existing challenges related to cost and manufacturing intricacies, the potential advantages warrant continued investigation and integration of titanium lock nuts within the automotive sector. Through ongoing exploration and adoption of this advanced material, the industry can potentially unlock enhanced vehicle performance, durability, and safety, underscoring the significance of considering titanium as a valuable and impactful component in advancing automotive engineering and design.
References
- Boyer, R. (1996). An overview on the use of titanium in the aerospace industry. Materials Science and Engineering: A, 213(1-2), 103-114.
- Lütjering, G., & Williams, J. C. (2003). Titanium. Springer Science & Business Media.
- Niinomi, M. (2003). Mechanical properties of biomedical titanium alloys. Materials Science and Engineering: A, 243(1-2), 231-236.
If you want to learn more about titanium lock nuts, welcome to contact us: sales@wisdomtitanium.com.