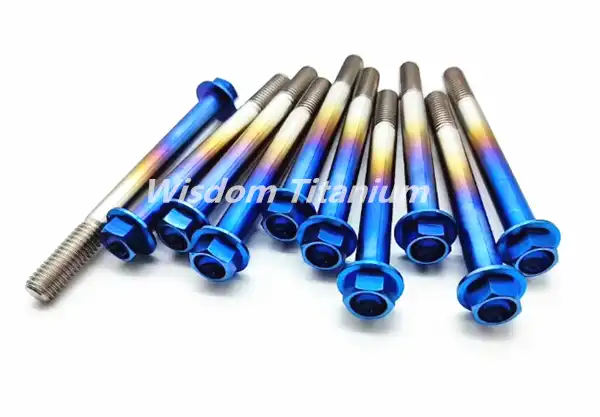
Can Titanium Bolts Replace Steel in Automotive Applications?
In the field of automotive engineering, the material selection of each component is crucial to ensuring safety, performance, and efficiency. Despite their common appearance, bolts are essential for maintaining vehicle structural integrity and dependability. Due to its high strength and durability, which are essential for withstanding the rigors of automotive environments, steel has historically been the material of choice for bolts.However, interest in titanium as a viable alternative to steel bolts has been sparked by advancements in metallurgical sciences. Titanium is appealing for automotive applications due to a number of advantages. It has a high strength-to-weight ratio, is significantly lighter than steel, and has a strength that is comparable to that of steel. Improved vehicle performance and fuel efficiency may result from this weight reduction.In addition, titanium has excellent resistance to corrosion, which is particularly advantageous in automotive applications where road salts and harsh weather can accelerate corrosion. This characteristic contributes to the overall durability and dependability of the vehicle by extending the bolts' lifespan and reducing the need for maintenance.The disadvantages of titanium bolts outweigh these benefits. They can affect manufacturing costs because they typically cost more than steel counterparts. Because titanium has a lower modulus of elasticity than steel, it may not be as effective in applications requiring a high clamping force or preload.In conclusion, although titanium bolts offer compelling advantages in automotive engineering such as weight savings and corrosion resistance, replacing steel bolts with them necessitates careful consideration of cost, specific application requirements, and performance trade-offs. Research and development may further enhance titanium's suitability and expand its use in automotive manufacturing as technology and materials advance.
Introduction to Titanium and Steel Bolts
Steel bolts have long been used to make automobiles because they are strong and cheap. They provide the strength and dependability necessary to withstand the demands of vehicle operation, ensuring performance and safety. Steel is used in a lot of bolts because it is strong, durable, and relatively cheap compared to other materials.However, due to its distinctive properties, titanium has emerged as a compelling alternative. Titanium is well-known for its excellent strength-to-weight ratio, which allows it to be significantly lighter than steel while maintaining a strength that is comparable. In automotive applications, where reducing vehicle weight can boost fuel efficiency and overall performance, this weight reduction potential is especially useful.titanium bolts also has a high resistance to corrosion, which is important for automotive components that are exposed to salt, moisture, and other environmental factors. This quality contributes to the longevity and dependability of vehicles by reducing the need for maintenance and extending the life of bolts.In spite of these benefits, titanium bolts have issues that need to be taken into consideration. The fact that titanium typically costs more than steel does can have an effect on manufacturing costs. Additionally, it lacks the elasticity of steel, which could have an impact on its performance in applications requiring a high clamping force or preload.In conclusion, while titanium offers distinct advantages that make it an appealing alternative, steel bolts continue to be the most popular choice in automotive manufacturing due to their robustness and cost-effectiveness. The ongoing research and development of titanium may further enhance its feasibility and expand its use in automotive applications as technology advances and materials science develops, potentially opening up new opportunities for improved vehicle design performance and efficiency.
Strength and Durability Comparison
Strength is one of the most important factors to consider when selecting bolts for automotive applications. Steel bolts, which are normally made of combinations like carbon steel or hardened steel, have a high return and elasticity. As a result, they are suitable for crucial tasks like assembling the chassis and mounting the engine.
Titanium has similar strength properties to steel, despite being significantly lighter than steel. Titanium alloys like Ti-6Al-4V, which are composed of 6% aluminum and 4% vanadium, are frequently used in industries that require high strength and resistance to corrosion. These alloys are half the weight and have the same strength as some grades of steel. This can help reduce the overall weight of the vehicle.
Corrosion Resistance and Environmental Factors
Corrosion of metal components in automobiles can be accelerated by a variety of environmental conditions, such as moisture, salt, and chemicals. Steel bolts, particularly those made of stainless steel, are known to some extent for their resistance to corrosion. However, titanium outperforms steel in this regard due to its inherent capacity to form an oxygen-resistant oxide layer. Even in harsh environments, titanium is highly resistant to corrosion thanks to this oxide layer.
Weight Reduction and Fuel Efficiency
In recent years, automobile manufacturers have increased their focus on weight reduction in an effort to cut emissions and boost fuel economy. Titanium's light weight may play a significant role in achieving these goals. By substituting titanium bolts for steel ones, manufacturers may be able to reduce the vehicle's overall weight without jeopardizing its structural integrity, thereby enhancing performance and fuel efficiency.
Cost Considerations and Manufacturing Challenges
Titanium has a lot going for it in terms of strength, weight, and corrosion resistance, but pricing and manufacturing challenges keep it out of the automobile market. Titanium is more costly than steel in terms of the raw ingredients and production techniques involved. Furthermore, titanium has different machining and forming qualities from steel, necessitating the employment of specialist equipment and knowledge.
Conclusion: The Future of Titanium Hex Bolts in Automotive Applications
In conclusion, despite the fact that titanium bolts have a higher strength-to-weight ratio, are resistant to corrosion, and have the potential to be lighter than steel, their widespread use in automotive applications faces difficulties related to cost and manufacturing complexity. However, titanium may become a viable option for some high-performance automotive components as a result of ongoing advancements in metallurgy and manufacturing techniques.
In the end, in automotive applications, choosing between steel bolts and titanium bolts depends on balancing performance requirements, costs, and technological viability. Materials and technologies that are driving innovation in vehicle design and manufacturing will also evolve in tandem with automotive engineering's continuing development.
If you want to learn more about titanium bolts, welcome to contact us: sales@wisdomtitanium.com.
References:
- ASM International Handbook Committee. (1993). ASM Handbook, Volume 2: Properties and Selection: Nonferrous Alloys and Special-Purpose Materials. ASM International.
- Boyer, R. R. (1996). An overview on the use of titanium in the aerospace industry. Materials Science and Engineering: A, 213(1-2), 103-114.
- Davis, J. R. (Ed.). (1998). ASM Specialty Handbook: Titanium and Titanium Alloys. ASM International.
- Lütjering, G., & Williams, J. C. (2007). Titanium. Springer Science & Business Media.