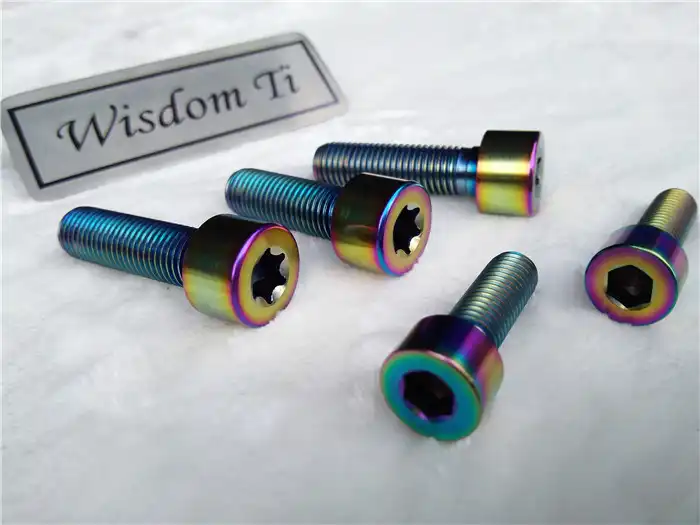
In the contemporary landscape of rapid manufacturing, prioritizing efficiency is of utmost importance. Every facet of the assembly process demands optimization to guarantee the swift and precise production of goods. While many elements are scrutinized for efficiency, the selection of fasteners is occasionally neglected. Although traditional steel bolts have historically been the go-to choice, the prospect of utilizing titanium allen head bolts as a superior alternative warrants exploration. This article embarks on a comprehensive exploration of the scientific underpinnings that underlie the potential efficiency enhancements associated with integrating titanium allen head bolts into assembly processes. By delving into this inquiry, we aim to shed light on the viability of this alternative and its capacity to elevate the overall efficiency and productivity of modern manufacturing operations.
With a background in the manufacturing sector, I recognize the pivotal significance of meticulous component selection in assembly operations. Bolts serve as linchpins in consolidating diverse elements of machinery, equipment, and structures, underscoring their indispensable role in ensuring structural integrity. The material composition of these bolts emerges as a crucial determinant, exerting a profound influence on the efficiency of the assembly process and the ultimate functionality and durability of the end product. Optimal material selection aligns with enhanced operational efficiency, bolstering the reliability and longevity of assembled components. By prioritizing the judicious choice of bolt materials, manufacturers can fortify the overall quality of their products, mitigate risks of premature failure, and cultivate a reputation for excellence in delivering robust and enduring solutions across industrial sectors.
Historically, steel has enjoyed primacy as the preferred material for bolts owing to its robustness and longevity. Nevertheless, titanium has surfaced as a compelling substitute replete with distinct advantages. Notably, titanium allen head bolts have garnered attention for their exceptional characteristics that render them particularly suitable for specific applications. The distinctive properties of titanium, including its superior strength-to-weight ratio, corrosion resistance, and biocompatibility, position it as a formidable contender in the realm of fastening solutions. This shift towards titanium underscores an evolving landscape in which innovation and performance drive material selection, prompting industries to reassess conventional choices and embrace advanced alternatives that promise heightened efficacy and reliability. As titanium gains prominence for its unparalleled attributes, the versatility and specialized benefits of titanium allen head bolts continue to captivate engineers and manufacturers seeking optimal solutions for diverse assembly requirements.
What are the key advantages of titanium allen head bolts in industrial applications?
A standout benefit of titanium allen head bolts lies in their remarkable strength-to-weight ratio, a hallmark of titanium's inherent properties. Renowned for its extraordinary lightweight nature coupled with exceptional strength, titanium presents a compelling advantage over traditional materials. This unique characteristic enables titanium bolts to deliver equivalent strength levels to steel counterparts while markedly reducing overall weight. Such a disparity in weight is pivotal in assembly contexts where weight considerations hold significance, notably in industries like aerospace and automotive manufacturing. The utilization of titanium bolts not only ensures robust structural integrity but also contributes to substantial efficiency enhancements by alleviating the burden of excess weight. In high-performance sectors where precision and efficiency are paramount, the adoption of titanium allen head bolts emerges as a strategic choice, offering a potent combination of strength and lightness that elevates operational effectiveness and performance standards.
Moreover, titanium allen head bolts showcase exceptional corrosion resistance, setting them apart from their steel counterparts. While steel bolts are susceptible to rust and corrosion, especially in challenging environments, titanium bolts demonstrate a remarkable ability to withstand corrosion, even in hostile conditions. This heightened resistance to corrosion not only ensures the prolonged longevity of the bolts themselves but also safeguards the equipment they secure, thereby diminishing the necessity for frequent maintenance and replacement. Consequently, this corrosion-resistant attribute not only fortifies the durability and reliability of the assembled components but also contributes significantly to operational efficiency by curtailing downtime associated with maintenance activities. The utilization of titanium allen head bolts, with their innate capacity to endure harsh environmental conditions, emerges as a judicious investment, aligning with the overarching objective of bolstering efficiency and minimizing lifecycle costs across diverse industrial applications.
An additional merit of titanium allen head bolts lies in their exceptional high temperature resistance, distinguishing them from conventional steel bolts. Titanium exhibits the ability to endure significantly elevated temperatures without compromising its structural integrity or strength, a trait that surpasses the capabilities of steel counterparts. This heightened temperature resilience positions titanium bolts as optimal choices for applications necessitating exposure to high temperatures, notably in environments like engines or industrial machinery where thermal stress is prevalent. The utilization of titanium bolts capable of withstanding such extreme conditions engenders seamless and efficient assembly processes by mitigating the likelihood of bolt failure under thermal duress. This inherent capacity of titanium to maintain performance in high-temperature settings not only ensures operational continuity but also underscores the critical role of advanced materials in enhancing reliability and operational efficacy across diverse industrial sectors reliant on resilient fastening solutions.
Moreover, titanium allen head bolts present outstanding biocompatibility, rendering them well-suited for utilization in medical instruments and devices. In contrast to steel bolts, which may induce allergic responses or tissue rejection in certain individuals, titanium bolts demonstrate biological inertness, minimizing the likelihood of eliciting adverse reactions. This exceptional biocompatibility broadens the scope of application for titanium bolts in medical assembly procedures, especially in contexts where precision and dependability hold utmost importance. The compatibility of titanium with biological systems not only mitigates potential health concerns but also signifies a pivotal advancement in promoting the integration of advanced materials within critical medical settings, underscoring the pivotal role of titanium allen head bolts in enhancing the safety, reliability, and performance of medical equipment and devices.
Conclusion
In summary, the empirical foundation underscores the capacity of titanium allen head bolts to elevate operational efficiency within assembly procedures. Their remarkable strength-to-weight ratio, corrosion resistance, high temperature resilience, and biocompatibility collectively position them as a persuasive option across diverse applications. Opting for titanium allen head bolts empowers manufacturers to enhance the operational efficiency, dependability, and efficacy of their assembly operations, culminating in superior product outcomes and heightened customer contentment. The utilization of these advanced bolts not only bolsters performance metrics but also underlines a commitment to leveraging cutting-edge materials to drive operational excellence. By integrating titanium allen head bolts into assembly frameworks, enterprises stand to optimize their processes, amplify product quality, and foster enhanced customer satisfaction, thereby solidifying the pivotal role of these bolts in catalyzing advancements within industrial realms.
References
-
Boyer, R. R. (1996). An overview on the use of titanium in the aerospace industry. Materials Science and Engineering: A, 213(1-2), 103-114.
-
Leyens, C., & Peters, M. (2003). Titanium and titanium alloys: fundamentals and applications. John Wiley & Sons.
- Niinomi, M. (2003). Mechanical biocompatibilities of titanium alloys for biomedical applications. Journal of the Mechanical Behavior of Biomedical Materials, 1(1), 30-42.
If you want to learn more about titanium allen head bolts, welcome to contact us: sales@wisdomtitanium.com.